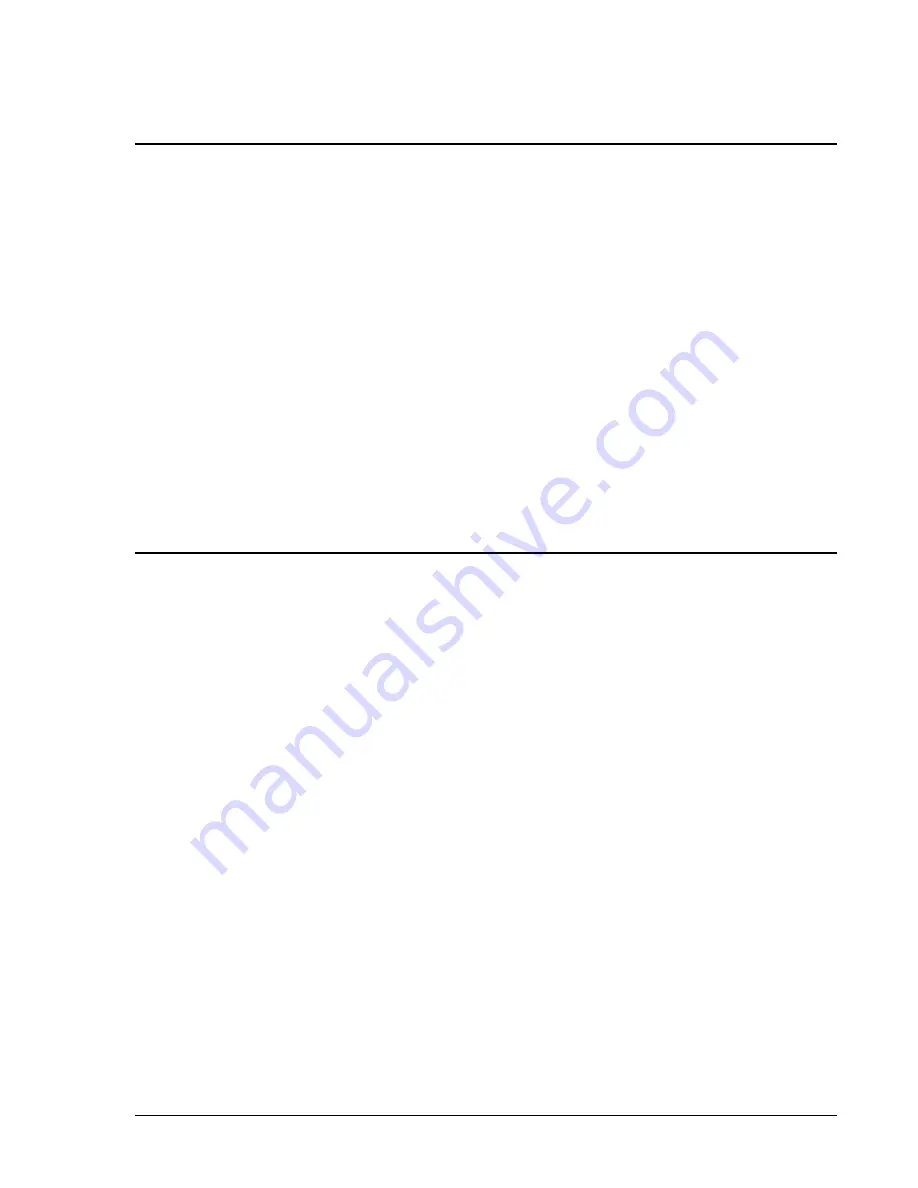
BE1-BPR General Information
1-1
SECTION 1 • GENERAL INFORMATION
DESCRIPTION
BE1-BPR Breaker Protection Relays are three-phase and neutral, microprocessor based relays designed
to provide power systems with protection and security against monitored breaker failure or to initiate multiple
shot breaker reclosings.
These relays incorporate a powerful means of programming internal relay logic to satisfy a wide range of user
requirements without making any relay hardware changes. Microprocessor based design provides the basic
features of a programmable logic controller (PLC) combined with an instantaneous overcurrent module.
Cased in either a 19 inch rack-mount or a vertical panel mount , the relay offers installation versatility. A wide
temperature, 2 line by 16 character display provides diagnostic and setup information. Two RS-232 serial
ports (one each front and rear) and one RS-485 serial port (rear) provide remote communication and relay
control.
Built-in diagnostics and monitoring features provide information for both the health of the relay and the health
of the breaker being monitored. Relay diagnostics include continuous background monitoring of the power
supplies, analog-to-digital (A/D) converter, random-access memory (RAM), read-only memory (ROM), and
electrically-erasable programmable ROM (EEPROM). A dedicated alarm (ALM) relay output provides power
supply, microprocessor, and software alarm status. Breaker diagnostics include a timing diagnostic log,
breaker contact duty monitoring, breaker resistor protection, and breaker arc detection. Other monitoring
features include oscillographic fault records and fault summary logs. BE1-BPR relays use the Inter-Range
Instrumentation Group (IRIG), Format B for high timing accuracy and resolution.
APPLICATION - STANDARD MODELS
Breaker Failure
BE1-BPR relays are intended to provide a preprogrammed solution for most breaker failure relaying
applications. Breaker failure relaying is the use of a current monitoring relay to determine whether or not
current continues to flow into a faulted circuit after a breaker has been instructed to interrupt the circuit. If
current continues to flow into the faulted circuit after a defined period of time has elapsed (sufficient for the
breaker to have interrupted the current), the circuit breaker is considered to have failed. Steps must then
be taken to trip the next set of breakers in the power system to prevent system damage. Breaker failure
schemes must be designed to isolate both the faulted circuit and the failed breaker.
Several reasons why a breaker fails to clear a fault are:
&
Trip circuit is open (broken wire, blown fuse, open trip coil).
&
Interrupting mechanism stuck, leaving a single phase of a three-phase circuit connected.
&
Interrupter flash-over due to the loss of dielectric strength through contamination or damage.
&
Operating mechanism failed to operate.
Breaker failure relays detect these conditions and initiate backup procedures.
Breaker failure relays are applied on a per breaker basis. That is, one breaker failure relay for each breaker
in the substation. BE1-BPR relay outputs must be arranged to initiate the tripping of all the circuit breakers
necessary to isolate the fault if the protected circuit breaker fails to operate. The relay may also need to
initiate transfer tripping of remote breakers to accomplish this task. Transfer tripping of the remote line end
for a breaker failure should also block reclosing of the remote circuit breakers. External lockout relays are
typically used to trip and block reclosing of the backup breakers because they normally require a positive
operator action to reset them.
Typically, breaker failure protection is applied to transmission and subtransmission systems. However,
breaker failure protection may be applied to any portion of the power system where failure of a circuit breaker
to operate properly could result in severe system damage or instability. Breaker failure protection can also
be used to selectively clear a failed breaker in a station with multiple buses without clearing the entire station.
Summary of Contents for BE1-BPR
Page 31: ...BE1 BPR Application 2 17...
Page 42: ...3 4 BE1 BPR Human Machine Interface Figure 3 4 BE1 BPR Relay Vertical Mount Front View...
Page 43: ...BE1 BPR Human Machine Interface 3 5 Figure 3 5 BE1 BPR Relay Vertical Mount Rear View...
Page 49: ...4 6 BE1 BPR Functional Description Figure 4 2 Enhanced BE1 BPR Menu Display Screens...
Page 50: ...BE1 BPR Functional Description 4 7 Figure 4 3 Standard BE1 BPR Menu Display Screens...
Page 94: ...5 4 BE1 BPR BESTlogic Figure 5 1 BESTlogic Function Blocks...
Page 121: ...BE1 BPR Installation 7 3 Figure 7 3 Overall Dimensions Vertical Mount...
Page 122: ...7 4 BE1 BPR Installation Figure 7 4 Overall Dimensions Side View Vertical Mount...
Page 123: ...BE1 BPR Installation 7 5 Figure 7 5 Panel Drilling Diagram Vertical Mount...