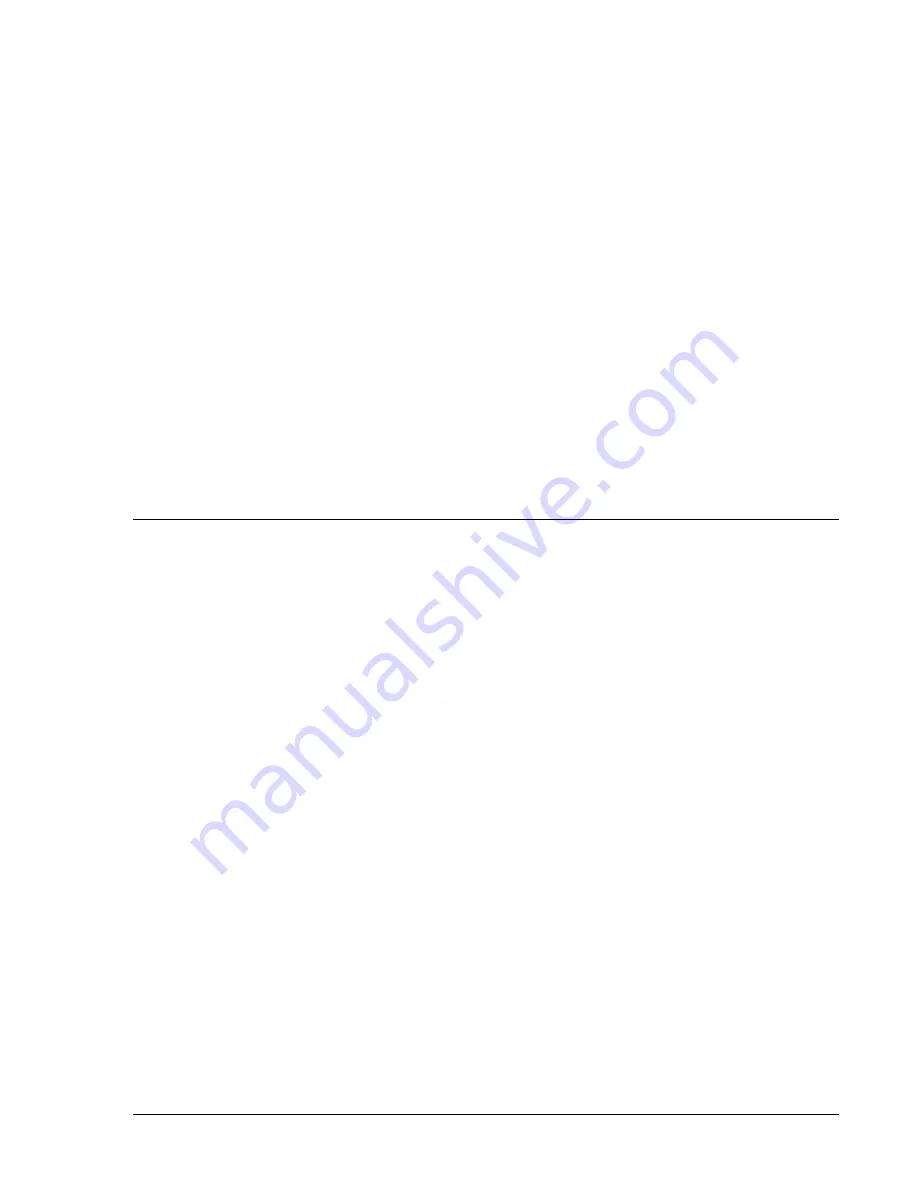
9365200990 Rev F
BE1-CDS240 General Information
1-7
The ASCII command interface is optimized to allow automating the procedure for setting the relay
by allowing settings files to be captured from the relay and edited using any software that
supports *.txt file format. These ASCII *.txt files can then be used to set the relay using the send
text file function of the communications software.
Modbus™ and other common protocols are optionally available for the RS-485 communications
port. A separate instruction manual appropriate for the protocol comes with each unit. Consult the
product bulletin or the factory for availability of these options and instruction manuals.
Installation
The BE1-CDS240 is available in two, fully draw-out, case styles; MX vertical can be mounted as
an M1, M2, FT31, or an FT32. MX horizontal units can be panel mounted or 19" rack mounted.
Relay terminals are clearly marked on the rear panel.
Testing and Maintenance
Four (4) testing methods are covered in this manual: acceptance testing, commissioning testing,
periodic testing, and functional testing.
The relay also provides a virtual testing function that allows the user to isolate a portion of the
logic program and test it by using a set of switches.
BESTCOMS Software
BE1-CDS240 BESTCOMS is a 32-bit Windows
based graphical user interface (GUI). It provides
the user with point-and-click capability for applying settings to the relay. This facilitates setting the
relay by eliminating the need for the user to be thoroughly knowledgeable of the ASCII
commands associated with the relay settings.
PRIMARY APPLICATIONS
The BE1-CDS240 Current Differential System provides percentage restrained differential protection along
with multiple overcurrent elements and is intended for use in any low impedance current differential
protection application including transformer, generator, motor, reactor, and bus protection. Its unique
capabilities make it ideally suited for applications with the following requirements.
Applications that require low burden to extend the linear range of CTs.
Applications where dedicated CTs for the differential are not available. Unlike traditional
differential relays, dedicated CT circuits are not required because each CT input is isolated from
the others and phase shift compensation can be accomplished internally.
Applications that require high accuracy across a wide frequency range such as motor, generator,
and generator step-up transformer protection or in co-generation facilities.
Applications that require the flexibility provided by wide settings ranges, multiple setting groups
and multiple coordination curves in one unit.
Applications that require the economy and space savings provided by a multifunction, multi-phase
unit. This one unit can provide all of the protection, as well as, the local and remote indication,
metering and control required on a typical circuit.
Applications that require harmonic restraint to aid security for the differential.
Applications that require communication capability and protocol support.
Applications where the optional case configurations facilitate modernizing protection and control
systems in existing substations.
Applications where the capabilities of a digital multifunction relay are required, yet draw-out
construction is also desirable.
Applications where bus protection is provided by a high-speed overcurrent-blocking scheme on
the transformer bus mains instead of dedicated bus differential circuit.
Applications where the capabilities of intelligent electronic devices (IEDs) are used to decrease
relay and equipment maintenance costs.
Summary of Contents for BE1-CDS240
Page 2: ......
Page 8: ...vi BE1 CDS240 Introduction 9365200990 Rev F This page intentionally left blank ...
Page 38: ...1 28 BE1 CDS240 General Information 9365200990 Rev F This page intentionally left blank ...
Page 40: ...ii BE1 CDS240 Quick Start 9365200990 Rev F This page intentionally left blank ...
Page 152: ...ii BE1 CDS240 Metering 9365200990 Rev F This page intentionally left blank ...
Page 226: ...iv BE1 CDS240 Application 9365200990 Rev F This page intentionally left blank ...
Page 286: ...ii BE1 CDS240 Security 9365200990 Rev F This page intentionally left blank ...
Page 290: ...9 4 BE1 CDS240 Security 9365200990 Rev F This page intentionally left blank ...
Page 292: ...ii BE1 CDS240 Human Machine Interface 9365200990 Rev F This page intentionally left blank ...
Page 306: ...10 14 BE1 CDS240 Human Machine Interface 9365200990 Rev F This page intentionally left blank ...
Page 308: ...ii BE1 CDS240 ASCII Command Interface 9365200990 Rev F This page intentionally left blank ...
Page 342: ...11 34 BE1 CDS240 ASCII Command Interface 9365200990 Rev F This page intentionally left blank ...
Page 349: ...Figure 12 5 Horizontal Rack Mount Front View 9365200990 Rev F BE1 CDS240 Installation 12 5 ...
Page 361: ...Figure 12 17 Typical DC Connection Diagrams 9365200990 Rev F BE1 CDS240 Installation 12 17 ...
Page 372: ...12 28 BE1 CDS240 Installation 9365200990 Rev F This page intentionally left blank ...
Page 468: ...13 92 BE1 CDS240 Testing and Maintenance 9365200990 Rev F This page intentionally left blank ...
Page 512: ...14 42 BE1 CDS240 BESTCOMS Software 9365200990 Rev F This page intentionally left blank ...
Page 544: ...ii BE1 CDS240 Terminal Communication 9365200990 Rev F This page intentionally left blank ...
Page 550: ...ii BE1 CDS240 Settings Calculations 9365200990 Rev F This page intentionally left blank ...
Page 578: ...D 28 BE1 CDS240 Settings Calculations 9365200990 Rev F This page intentionally left blank ...
Page 579: ......