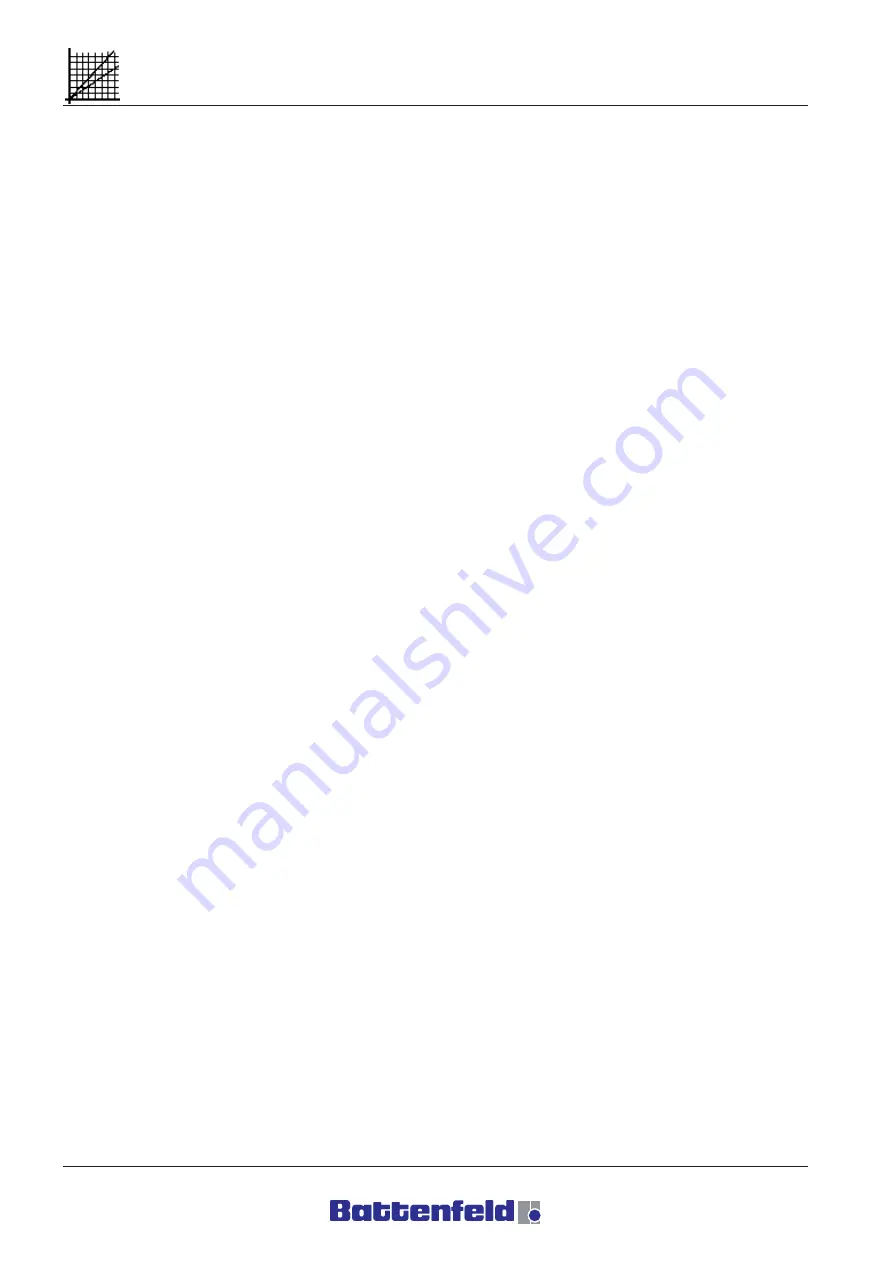
A: R82GB0CA.PDM
B: R82DE0CA.PDM
E: 080403 / T. Wenger
G: 020403 / TCS
Section 3
Page 8
Specifications
05/16 Ejector forward (from IMM)
IMM signals that the ejector is forward.
06/16 Core pullers released, HD can move
in (IMM)
The IMM signals to the HD that the core pullers
are in position to allow the removal device to
enter (regardless of the position of the mounting
plate).
07/16 Core pullers in removal position
(IMM)
The IMM signals to the HD that the core pullers
are in position to remove the casting.
08/16 Defective casting (from IMM)
The IMM signals to the HD that the removed
casting is defective. The signal must be
triggered by ”Tool open” and can be reset by
”Close tool”.
10/16 IMM Fully automatic mode (from IMM)
The IMM signals to the HD that the operating
mode selector is set to ”Fully automatic”.
12/16 Tool closed (IMM)
The IMM signals to the HD that the closing
sequence has been completed. The ”Start
closing” signal is then cancelled.
3.10.3 Handling device signals
17/32 Start Tool close sequence (by HD)
Activate Tool close: The contact is closed when
the HD has been extended to the point where
the tool can be closed and when other HD
control devices activate the Tool close
sequence.
This contact is only bypassed automatically
when the IMM is operated without the HD.
It must not be possible to activate the Tool close
action when closing the guard door, in manual
operation or by using the ”OR” function button.
The signal is activated during the closing
sequence. If the signal is cancelled, the closing
movement must be interrupted.
18/26 Tool area monitoring free (HD)
Open/close tool monitoring: The contact is
made by the limit switch on the positioning slide.
The limit switch is activated when the
positioning slide leaves its starting position in the
IMM area (before it enters the tool area). If the
link is open, the IMM can neither be opened or
closed. The contact can also be made without
the HD.
Summary of Contents for UNILOG B2
Page 4: ...A PB2GBI1A P65 B PB2DEI1A P65 E 180202 Ruder G 190202 G Krajnik Section IN1 Page 2 Index...
Page 10: ......
Page 14: ...A R82GB0AA PDM B R82DE0AA PDM E 080403 T Wenger G 020403 TCS Section 1 Page 4 General...
Page 16: ...A R82GB0AA PDM B R82DE0AA PDM E 080403 T Wenger G 020403 TCS Section 1 Page 6 General...
Page 32: ...A R82GB0CA PDM B R82DE0CA PDM E 080403 T Wenger G 020403 TCS Section 3 Page 10 Specifications...
Page 118: ...A R82GB0HA PMD B R82DE0HA PMD E 080403 T Wenger G 020403 TCS Section 7 Page 16 Maintenance...