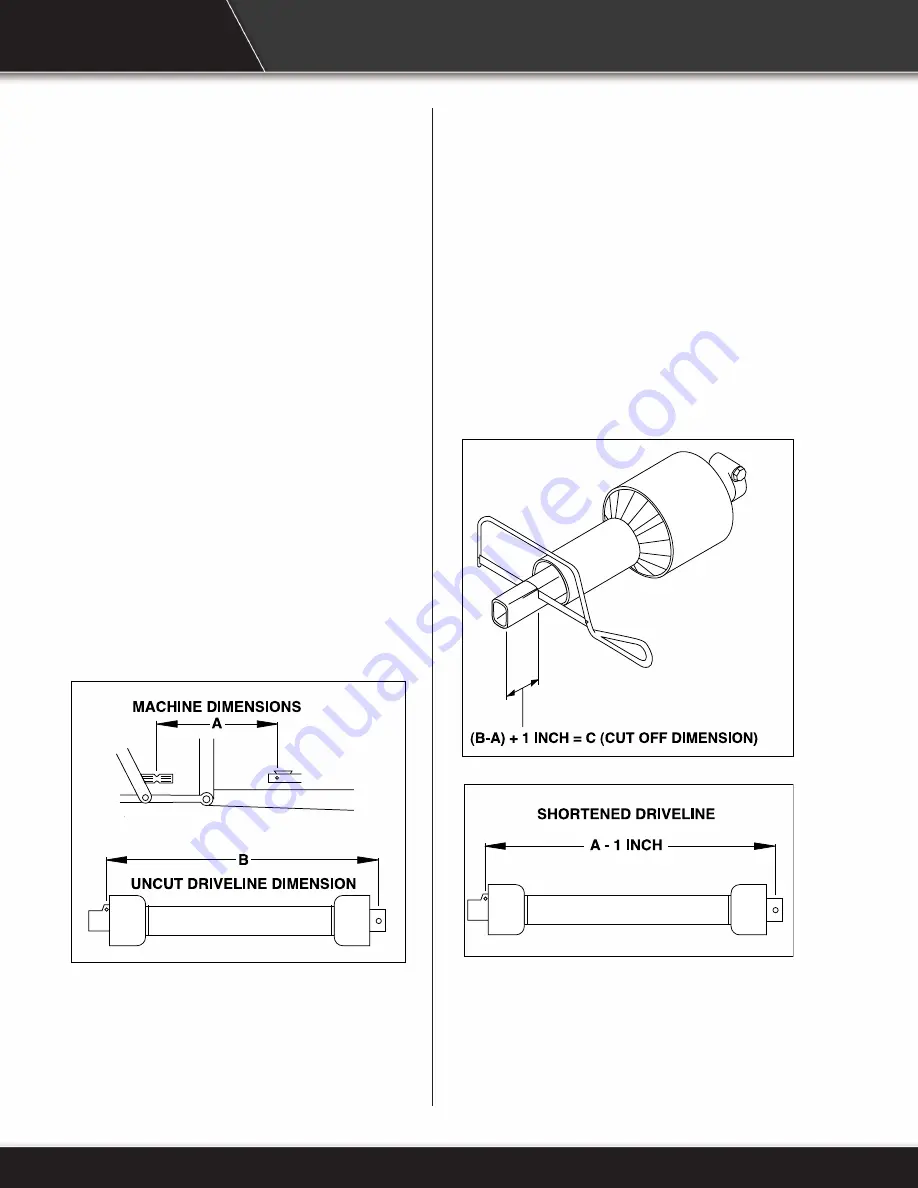
4.3 Driveshaft Dimension
To accompany the variety of 3 point hitch geometry
available today, the driveshaft can be too long for
some machines or too short for others. It is very
important that the driveshaft be free to telescope
but not to bottom out when going through its
working range. If the driveshaft bottoms out, the
bearings on both the machine and tractor PTO
shaft will be overloaded and fail in a short time.
To determine the proper length of the driveshaft,
follow this procedure:
1. Attach stump grinder to tractor but do not
attach driveshaft.
2. Raise grinder until the input shaft is level with
tractor PTO shaft.
3. Measure dimension (A) between locking
grooves on tractor PTO shaft and grinder input
shaft.
4. Measure same dimension (B) on compressed
driveshaft.
5. If compressed driveshaft dimension (B)
exceeds the machine dimension (A), driveshaft
must be cut.
When cutting driveshaft, follow this procedure:
1. Subtract machine dimension (A) from uncut
driveshaft dimension (B). This dimension
determines how much too long the driveshaft
is.
2. Add 1 in. (25 mm) to the dimension to be sure
it doesn’t bottom out, to determine cut off
dimension (C).
3. Use a hacksaw to cut dimension (C) from both
ends. Cut both plastic tubes and metal cores.
4.
Use a file to remove burrs from cut edges.
5. Assemble shaft.
6. Make sure shaft can telescope freely. If it does
not, separate and inspect for burrs or cuttings
on shaft ends. Be sure it telescopes freely
before installing.
12