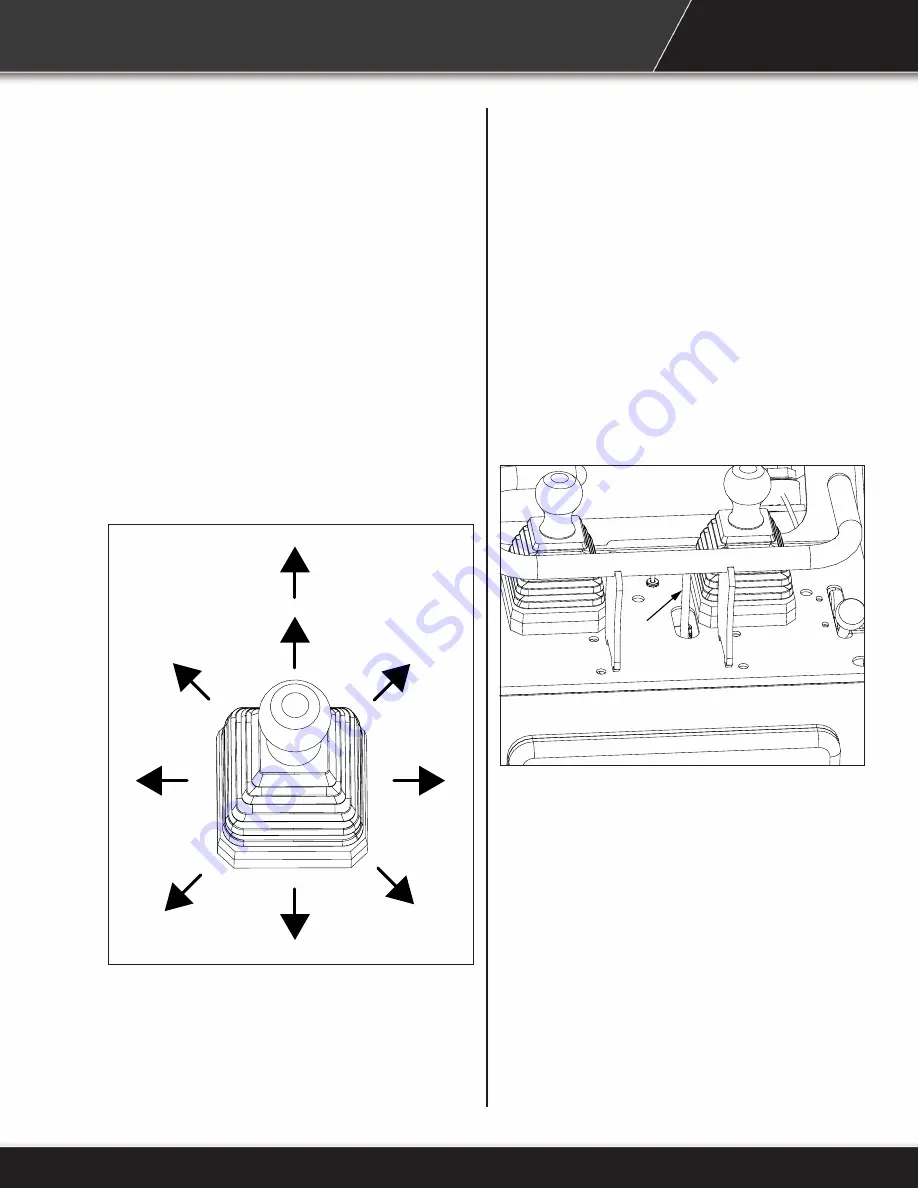
Boom Joystick
Move joystick forward (A) to lower lift arms.
Move joystick to the right (B) to tilt attachment
forward.
Move joystick rearward (C) to raise lift arms.
Move joystick to the left (D) to tilt attachment back.
Push joystick fully forward into detent position (E)
to allow a bucket or blade to follow the contour of
the ground.
A
B
C
D
E
Key Switch
Key switch has three positions: off, run, and start.
Rotate the key to the start position to start engine.
Release key when engine starts and it will move
automatically to the run position.
Rotate key to off position to stop engine.
Auxiliary Hydraulic Control
Auxiliary hydraulic control (I) provides a continuous
hydraulic flow to attachment. Center position is
off/locked. Move control forward for flow in one
direction or rearward for flow in the other direction.
I
Engine Preheat
Engine preheat is automatically controlled by the
Lofa control panel.
17