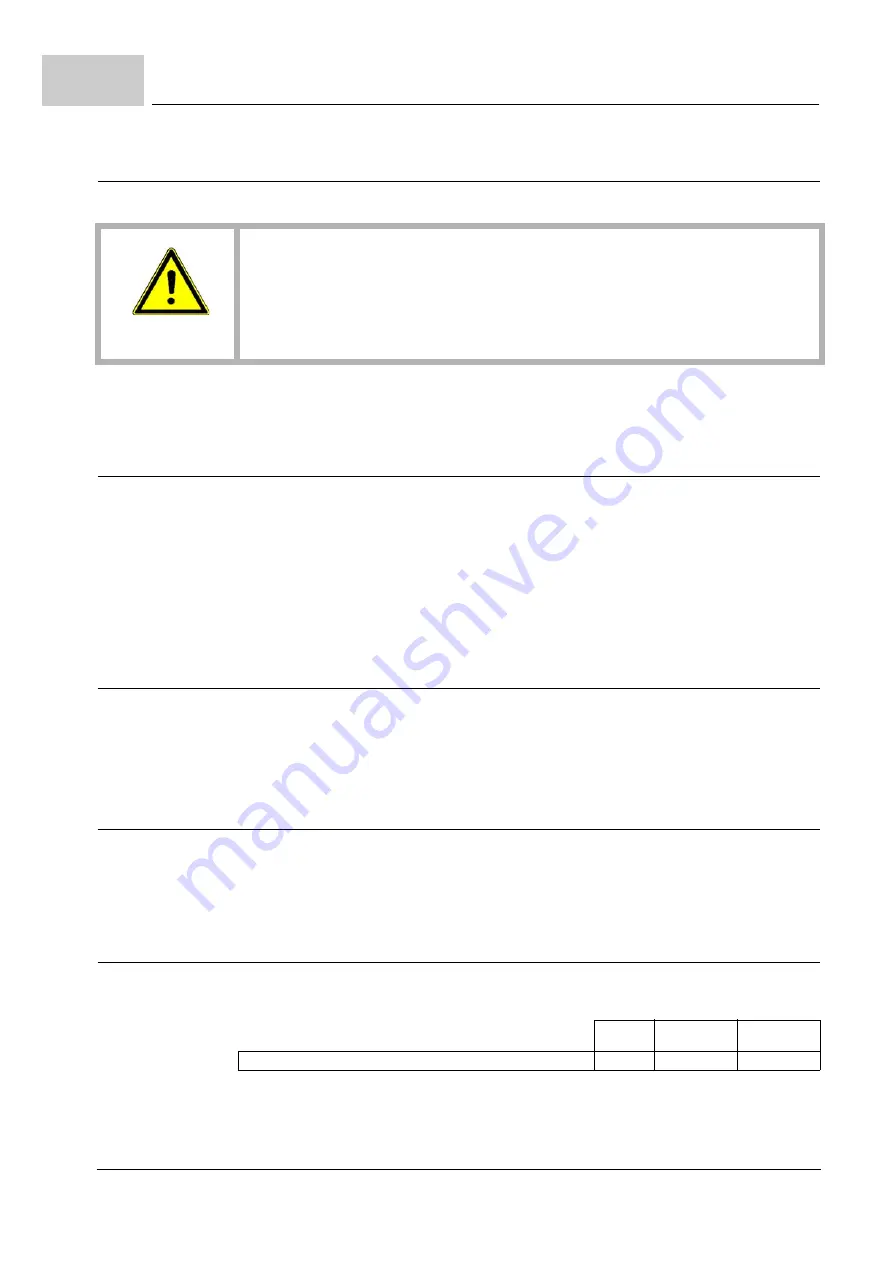
Spare parts
Operation manual
b maXX
BM4100 (NWR)
Document no.: 5.04052.09
Baumüller Nürnberg GmbH
10
1.7
1.7
Spare parts
Procure spare parts through an authorized dealer or directly from the manufacturer.
See also
1.8
Guarantee provisions
The guarantee provisions are stated in a separate document of the sales documents.
The devices described herein may only be operated in accordance with the stipulated
methods, procedures and conditions. Anything else not presented here, including the op-
eration of devices in mounted positions, is not permitted and must be cleared with the
plant on a case-by-case basis. If the devices are operated in any other manner than as
described within these instruction handbook, then all guarantee and warranty rights are
rendered null and void.
1.9
Customer service
Our customer service is available to provide you with technical information.
Info on the responsible contact persons is available at all times via telephone, fax, mail or
the Internet.
1.10 Terms used
The term „device“ or the item designation BM4XXX are also used in this documentation
for this Baumüller product. A list of the abbreviations used can be found in
1.11 List of other applicable documents
Parameter hand-
book
WARNING!
False or flawed spare parts can lead to damage, malfunction or complete fail-
ure, thus endangering safety.
Therefore:
m
Only use original spare parts of the manufacturer.
Doc No.
Part No.
German
Part No.
English
Parameter manual basic unit b maXX b maXX 4100 mains inverter
5.04054
392423
392424
Summary of Contents for b maXX 4100 Series
Page 143: ......