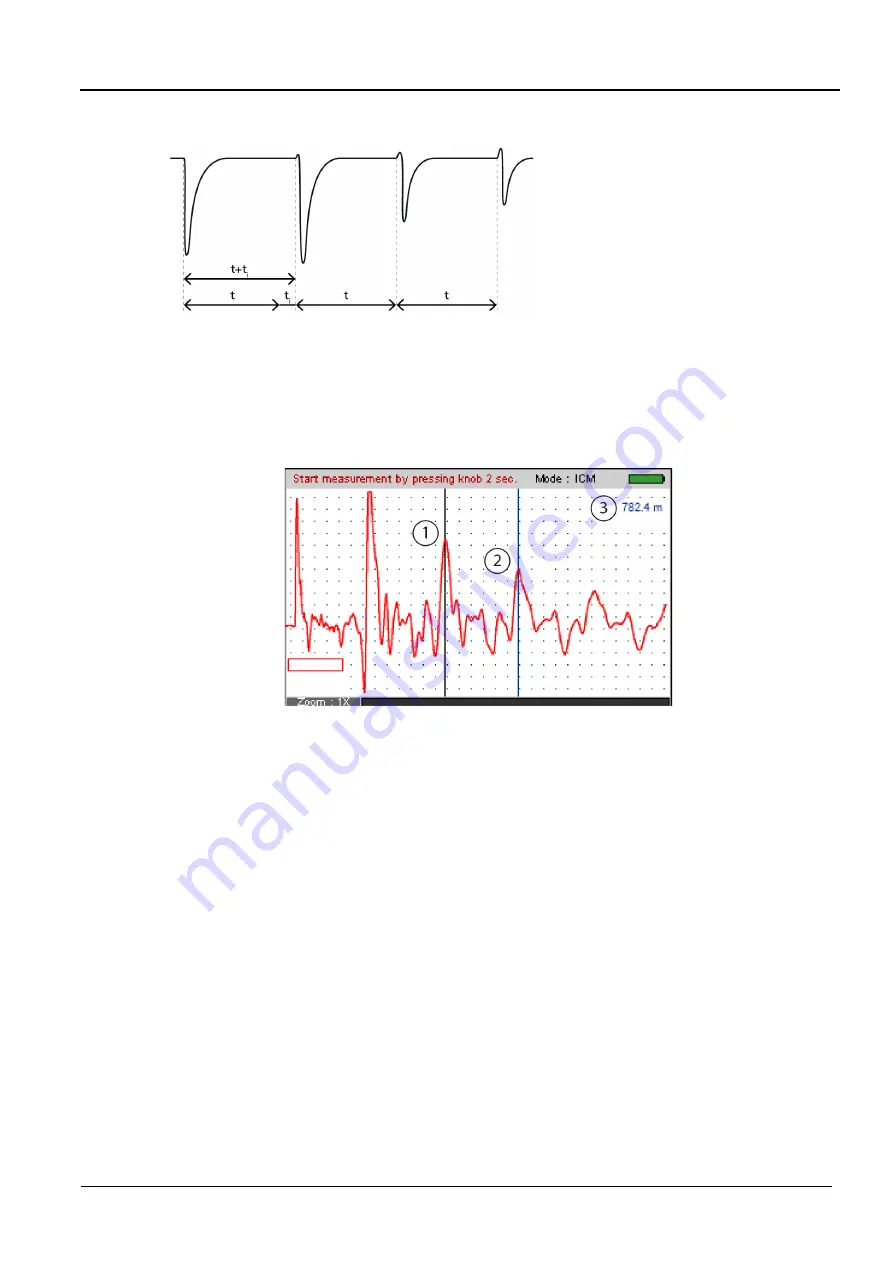
Cable fault pre-location
Syscompact 2000 M pro
70 / 98
822-175-2
t
Pulse duration
t
i
Ignition lag time in the first reflection period (ionization time)
v/2 Velocity of propagation
Procedure
1. Press the
CURSOR
key.
2. Place the zero cursor on a peak of the trace (1).
3. Place another cursor on the next peak of the trace (2).
The fault distance including the length of the test lead is displayed (3).
4. Subtract the length of the test lead (10 m) from the displayed fault distance.
Recommendation:
With long cables, place the each of the cursors on the rising flank.
Recommendation if the fault position is not easily visible
If no breakdown was achieved or if the fault position is not visible properly in the reflection
image, increase the voltage (if permitted) and repeat the measurement.
Summary of Contents for Sys compact 2000 M pro
Page 97: ......