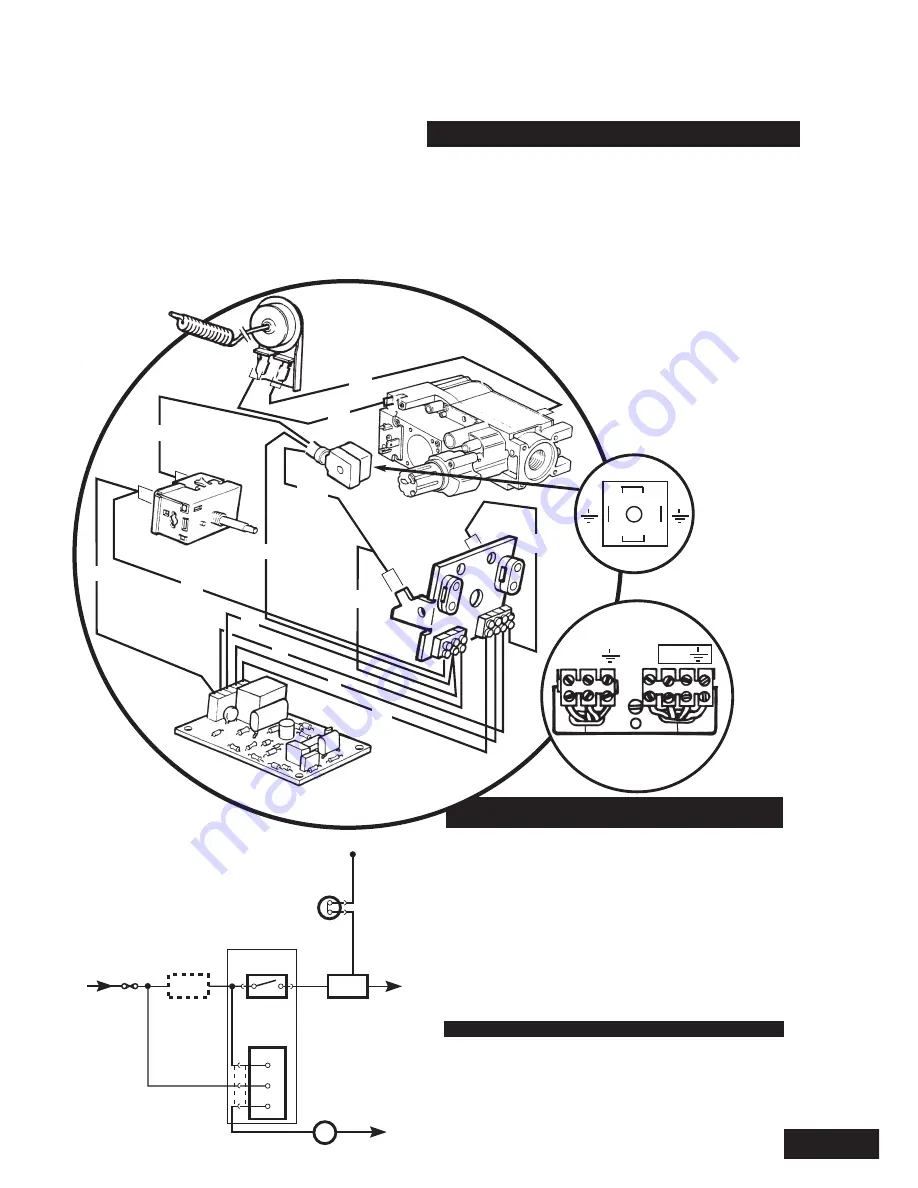
23
Electrical Supply
The electrical supply for this Solo 2 RS depends on
the design of the central heating system i.e.
Gravity DHW and Pumped Central Heating - 3 core
cable.
Fully Pumped, Open Vented with rising primaries - 4
core cable. However, 3 core cable can be used if the
timed pump overrun and overheat thermostat are
disconnected.
Sealed Systems and Fully Pumped
Systems with dropping pipework - 4
core cable must be used.
Detail of the electrical supply
for the various system
designs can be found below.
FOR FULLY PUMPED AND SEALED
SYSTEMS
The recommended cable for connection to the
appliance terminal strip is 4-core 0.75mm
2
(24 x 0.2mm dia) P.V.C. IEC 53 code 227 (heat
resistant).
External wiring must be correctly earthed and
polarised and in accordance with current I.E.E. wiring
regulations.
The mains supply required is 230V ~ 50Hz fused at
3A.
WARNING
THIS APPLIANCE MUST BE EARTHED.
NOTE: The method of connection to the electricity
supply must facilitate complete electrical isolation of
the appliance.
Thermocouple
Overheat
Thermostat
Fuse
3A
L
N
N
External
Programmer
or
br
w
w
2
3
Pump
Gas
Valve
Pump-Overrun
Timer
r
br
Boiler
Thermostat
220/240V
KEY
br -
brown
b -
blue
g/y - green/yellow
or -
orange
r
-
red
w -
white
g/y
w
w
br
g/y
g/y
b
or
or
b
b
br
r
Overheat
thermostat
Gas valve
Boiler
thermostat
Pump Overrun
Circuit
S/L N
P/L
Pump
L N
2
1
view in arrow
direction