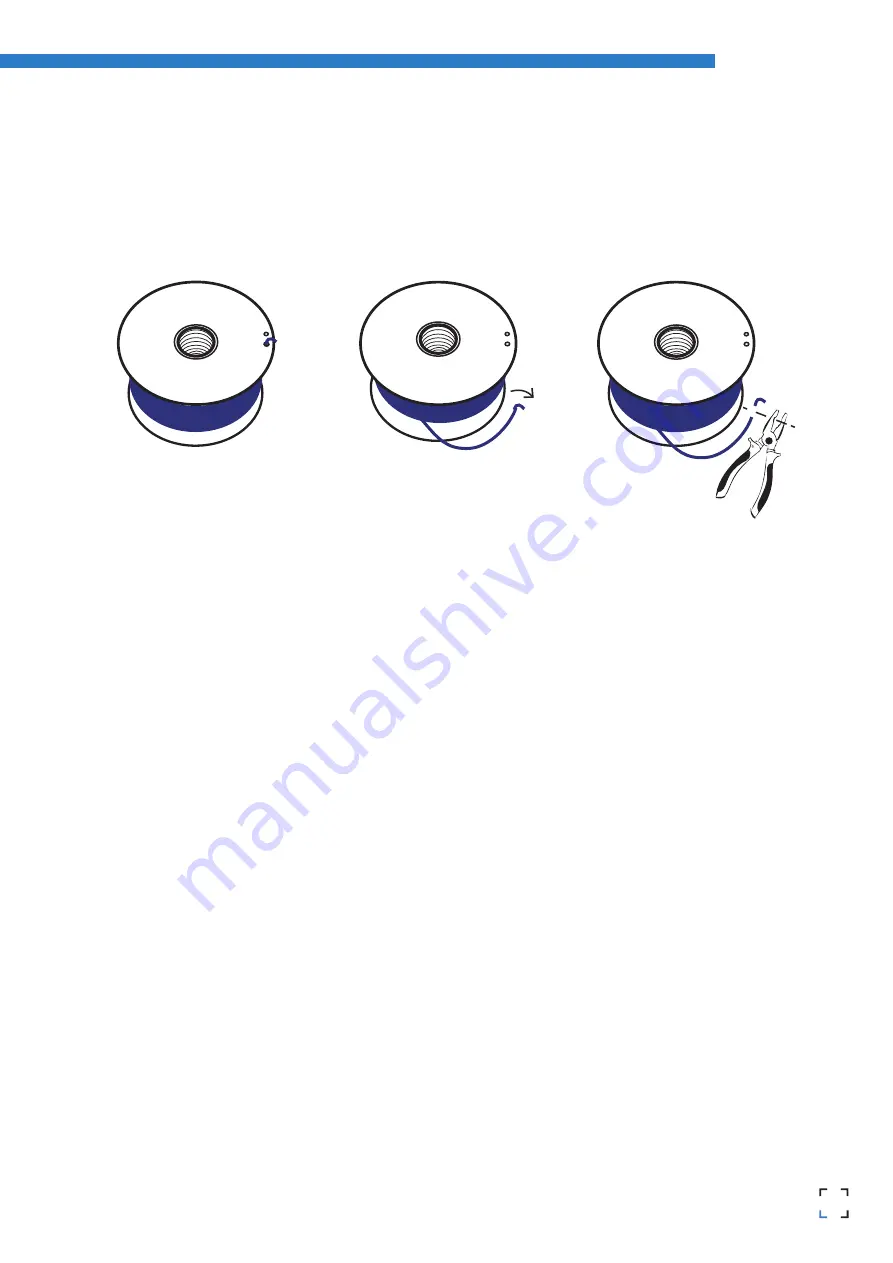
13
12
RepRapBCN
User Manual
Loading filament
One of the more common operations in our BCN3DR will be, for several reasons, loading and unloading filament: a
change of color, a change of material, using a fresh spool, cleaning, maintenance...
•
Unloading:
1. Heat the extruder selecting Preheat PLA in the menu.
2. Click on Prepare > Move Axis > 1 mm > Extruder and rotate the wheel slightly clockwise to extrude a few milli-
metres of material. This procedure will help prevent jams.
3. Click on Prepare > Move Axis > 1 mm > Extruder and rotate the wheel anticlockwise a 100mm moving the gear a
few steps back until the filament is free.
4. Untighten the two idler screws on the extruder.
5. Manually extract all the filament from the Bowden tube.
•
Loading:
Once the thread is out, disconnect the Bowden tube from the hotend connector. The easiest way to do that is by
following these steps:
1. Tighten the Bowden tube to the end from below.
2. Manually open the latch taking care not to crush the tube.
3. Pull the tube out of the connector
4. Untighten the two idler screws on the extruder.
5. Select Preheat PLA in the menu and insert the filament along the whole tube until 20mm stick out of it.
6. With the help of some pliers, insert the plastic thread into the hotend until filament is extruded through the
nozzle. If necessary, push the filament from the extruder deeper inside the tube.
7. Once the nozzle is full of filament, grab the end sticking out of the extruder and pull it out while, at the same
time, inserting the tube into the connector.
8. Once the Bowden tube is firmly held by the connector, slightly tighten the idler screws by hand.
9. Once this is done, the filament is loaded and the machine ready to print.
Summary of Contents for BCN3DR
Page 1: ...R...