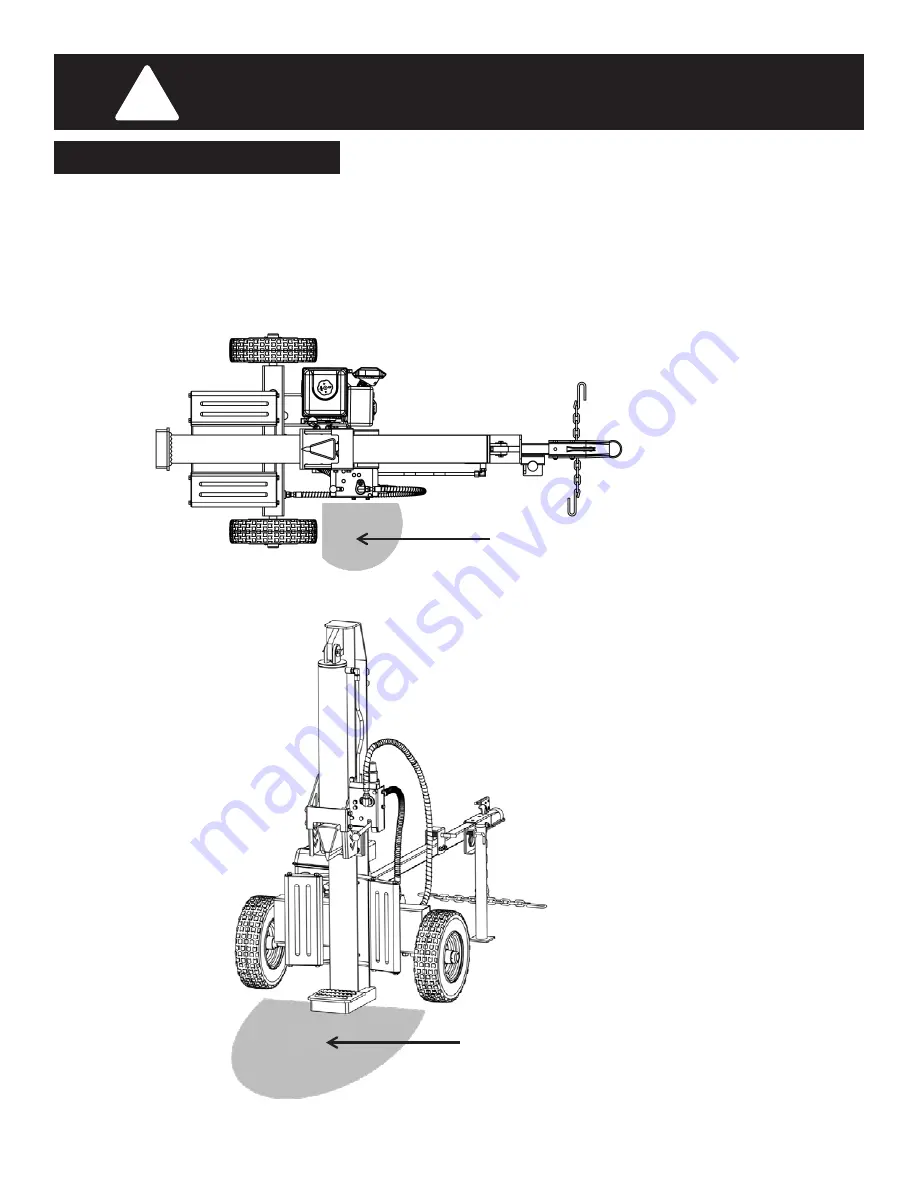
7
ONLY
operate the log splitter from the operator zone as shown in the diagrams below. The operator has the safest
and most efficient access to the control valve and the beam in this location. Operating the log splitter in another
location can result in serious injury or death.
OPERATOR ZONE
IMPORTANT SAFETY INFORMATION
!
ONLY
operate the log splitter from the operator zone as shown in the diagrams below. The operator has the safest and
most efficient access to the control valve and the beam in this location. Operating the log splitter in another location can
result in serious injury or death.
a. Horizontal Operating Position: Stand on the control lever side of the log splitter and stabilize log if needed. See
FIGURE 1.
b. Vertical Operating Position: Stand in front of the log splitter and stabilize log if needed. See FIGURE 2.
GENERAL REPAIR
OPERATOR ZONE
Operator Zone
(FIGURE 1).
Operator Zone
(FIGURE 2).
Page 7