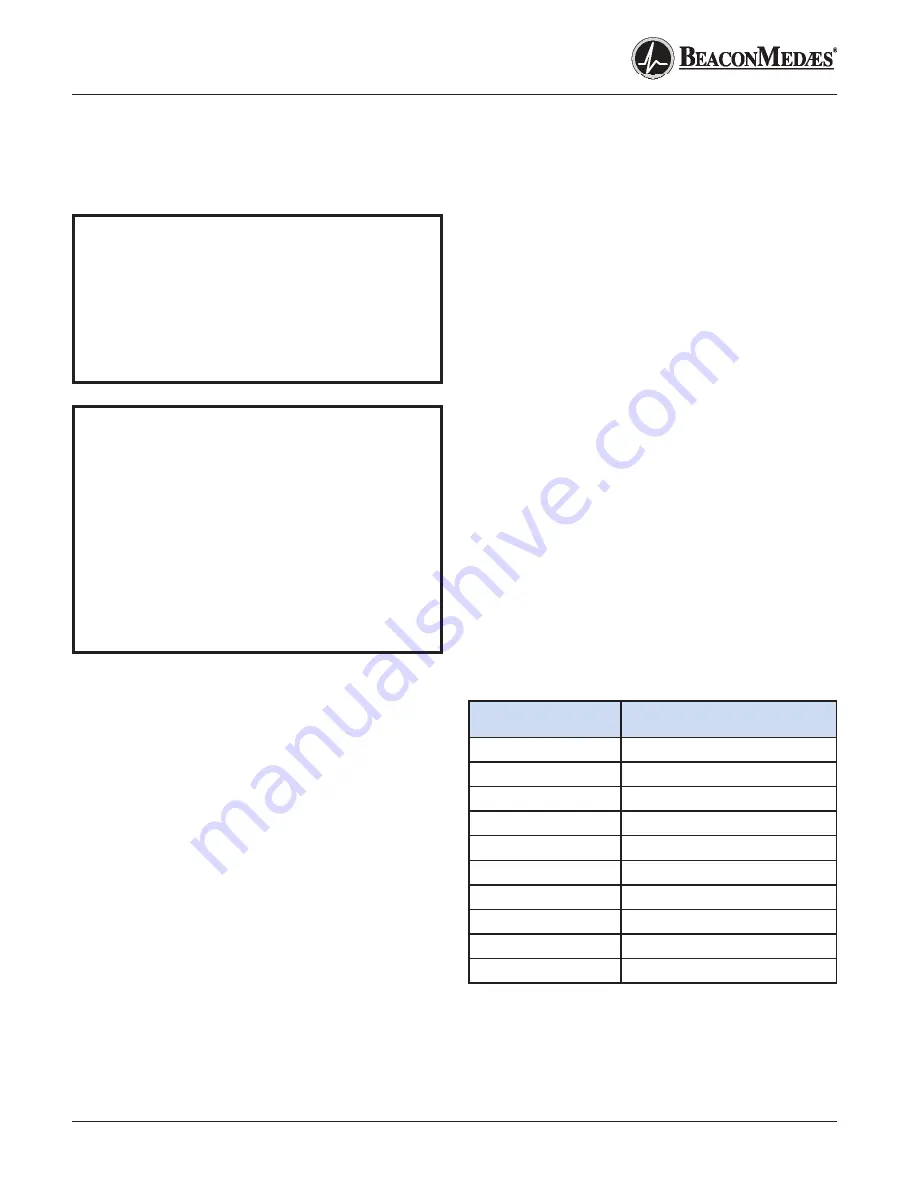
A-6
“Oil-Less” Scroll Laboratory Air
4107 9006 25.11
Appendix A: Desiccant Dryer
A compressed air dryer should give long and
trouble free operation if the recommended
preventative maintenance program is carried out.
The following is a recommended schedule:
1.
Quarterly procedure
- Clean the auto drain in
the coalescing fi lter. Monitor the backpressure
on the purging tower. If the gauge reads more
than 0 psig (when purging), check the purge
muffl
er for blockage and replace if necessary.
2.
Annual procedure
- Replace all fi lter
cartridges and purge muffl
er(s). Check the
automatic drain function in the coalescing
fi lter. Refer to chart located in Section A.4.1 for
correct system size and part numbers. Contact
BeaconMedæs Service
at 1-888-4MEDGAS for
parts.
3.
Three-year procedure
- Change all annual
parts. Change desiccant, check valves, and
purge valve(s). See chart in Section A.4.1 for
correct system size and part numbers.
A.4.1 Maintenance Interval
Service Interval
Description
Every year
Pre-fi lter
Every year
After-fi lter
Every year
Purge muffl
er
Every 3 years
Desiccant
Every 3 years
Check valve
Every 3 years
Tower o-ring
Every 3 years
Canister o-ring
As needed
Switching valve
As needed
Tower pressure gauge
As needed
Purge Poppit Valve
Note: All service components are listed as parts
within the service repair kits in Section 5.2
A.4 Maintenance
WARNING:
Always notify the appropriate facility
staff before performing any maintenance
or service procedures on the air system.
Compressed air levels may be aff ected
during maintenance or service procedures.
WARNING:
Compressed air can be dangerous unless
safety precautions are observed in the
use of compressed air and compressed
air equipment. Completely vent the
internal air pressure to the atmosphere
before disassembling any subassemblies
or components and before doing any
work on compressed air equipment. To
vent internal air pressure, follow the
maintenance shutdown instructions.