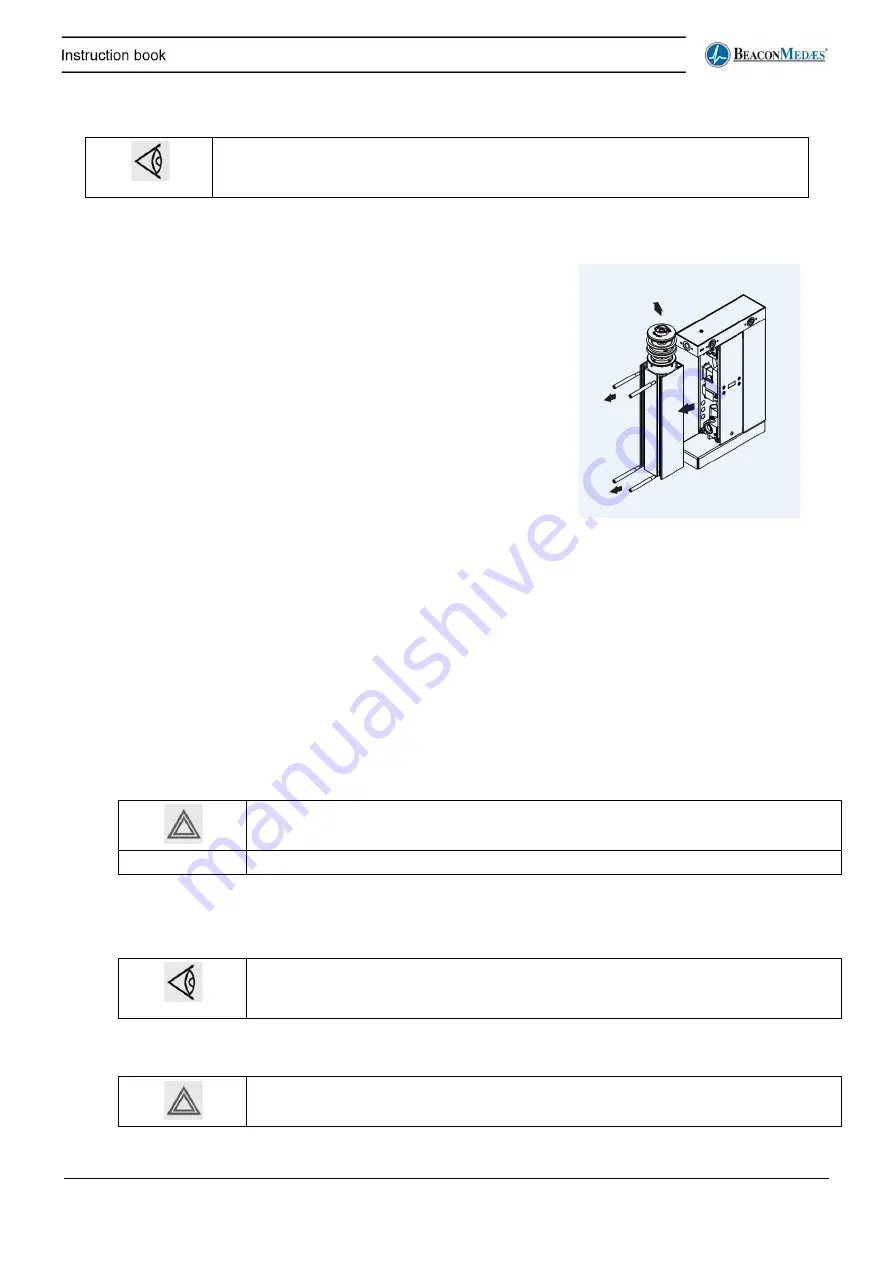
4233 5000 13
71
8.3 Dryer unit desiccant cartridge change
Desiccant cartridge for dMED 25 & dMED 35 dryer
1. Remove prefiltration and hoses.
2. Unscrew four bolts ¾ turn on the opposite tower to aid
desiccant changeout process.
3. Unscrew the four pressure housing retaining bolts and
slide out the pressure housing.
4. Remove banjo fixing bolt using hex key.
5. Extract end cap and banjo assembly from pressure housing.
6. Using banjo fixing bolt, retract the cartridge from pressure
housing.
7. Replace with new cartridge supplied as part of the cartridge
service kit.
8. Ensure O-ring seals are in place when installing cartridge and
assembly in pressure housing.
9. Follow above steps in reverse to finish installing new
cartridge into the dryer.
10. Repeat steps 1 – 10 for the second pressure housing.
11. Ensure the dryer is leak-free before operating pressure is applied to the dryer.
12. Follow start up procedure as stated in the operations section of this manual.
Desiccant cartridge for dMED 45 - dMED 300 dryer
Maintenance information leaflet is provided with each desiccant cartridge replacement kit
showing how to carry out the change out.
Warning
To ensure that the unit always produces pharmacopoeia compliant air, only dedicated and
genuine spare parts must be used.
The installation and maintenance must be done by trained and certified personnel.
Pharmacopoeia compliance
When replacing desiccant, make sure that the desiccant is disposed of according to the
local regulations.
Consult the parts list for part numbers.
After carrying out any maintenance or repair work, Pharmacopoeia testing must be done
by a local testing company to assure reliable and correct operation of the unit.
Ensure shutdown and start up procedures are followed prior to carrying out any
maintenance work on the dryer
Summary of Contents for dMED 025
Page 2: ......