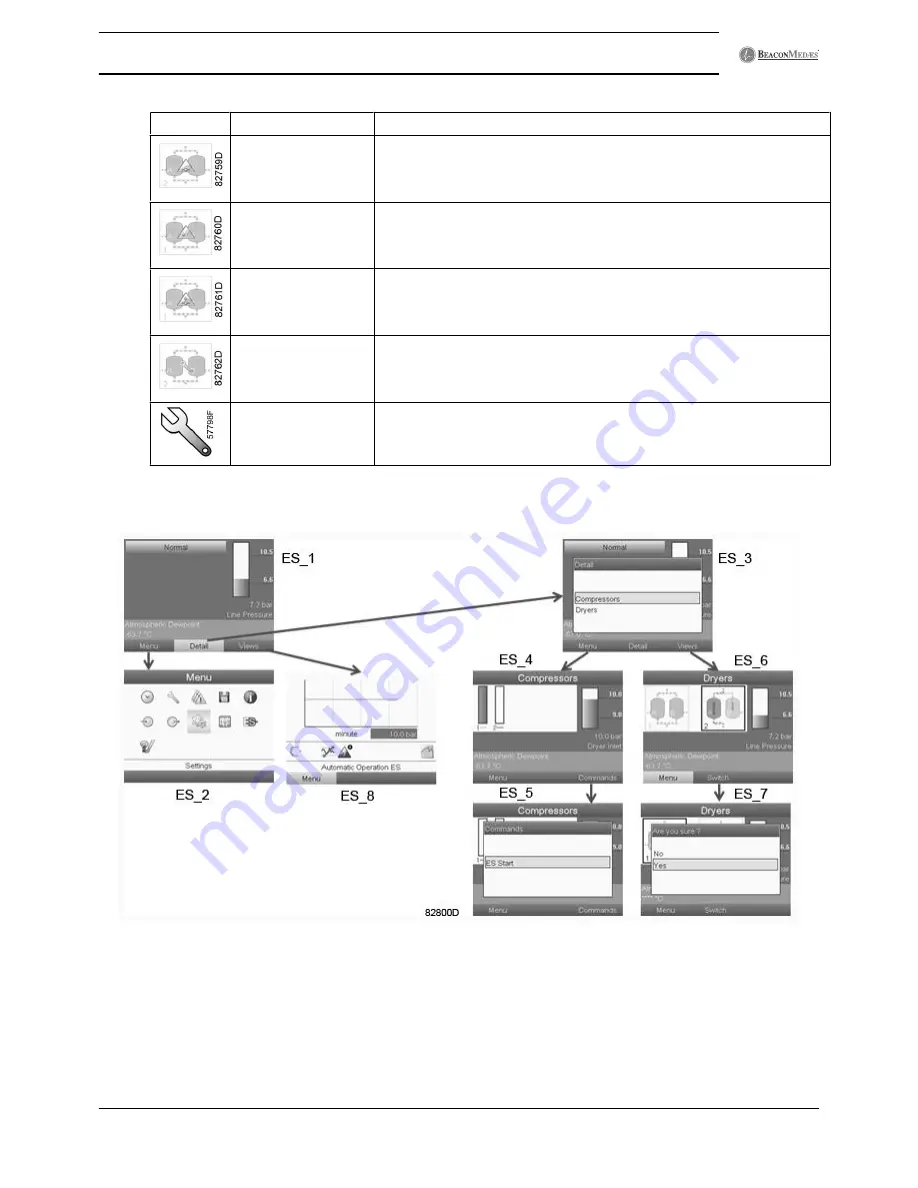
Icon
Status
Description
Pressure fault
Dryer outlet pressure too low. Manual reset required.
Dew point fault
Dew point too high. Manual reset required.
Pressure and dew
point fault
Dryer outlet pressure too low and dew point too high. Manual reset
required.
Service enabled
A service function has been activated.
Service required
The programmed service interval is reached and maintenance is
required.
Menu structure
Main menu flowchart (full access mode)
Downward navigation through the menus is done by pressing the Enter button. Upward navigation through
the menu is done by pressing the Escape button on the controller. Specific submenus and commands will be
explained in the following chapters. The main screens are referred to as follows:
• Starting screen (ES_1): shows the inlet net pressure and the status of the plant.
• Main menu (ES_2): gives access to the different submenus (see section
Central controller operation
).
Instruction book
2920 7099 70
23
Summary of Contents for dMED 100
Page 2: ......
Page 40: ...Inputs Instruction book 38 2920 7099 70...
Page 45: ...Instruction book 2920 7099 70 43...
Page 54: ...4 Installation 4 1 Dimension drawings Instruction book 52 2920 7099 70...
Page 55: ...Instruction book 2920 7099 70 53...
Page 56: ...Instruction book 54 2920 7099 70...
Page 57: ...Instruction book 2920 7099 70 55...
Page 58: ...Instruction book 56 2920 7099 70...
Page 59: ...Instruction book 2920 7099 70 57...
Page 60: ...Instruction book 58 2920 7099 70...
Page 61: ...Instruction book 2920 7099 70 59...
Page 62: ...References on drawings Instruction book 60 2920 7099 70...
Page 93: ......
Page 94: ...No 2920 7099 70 2012 01 Printed in Belgium www beaconmedaes com...