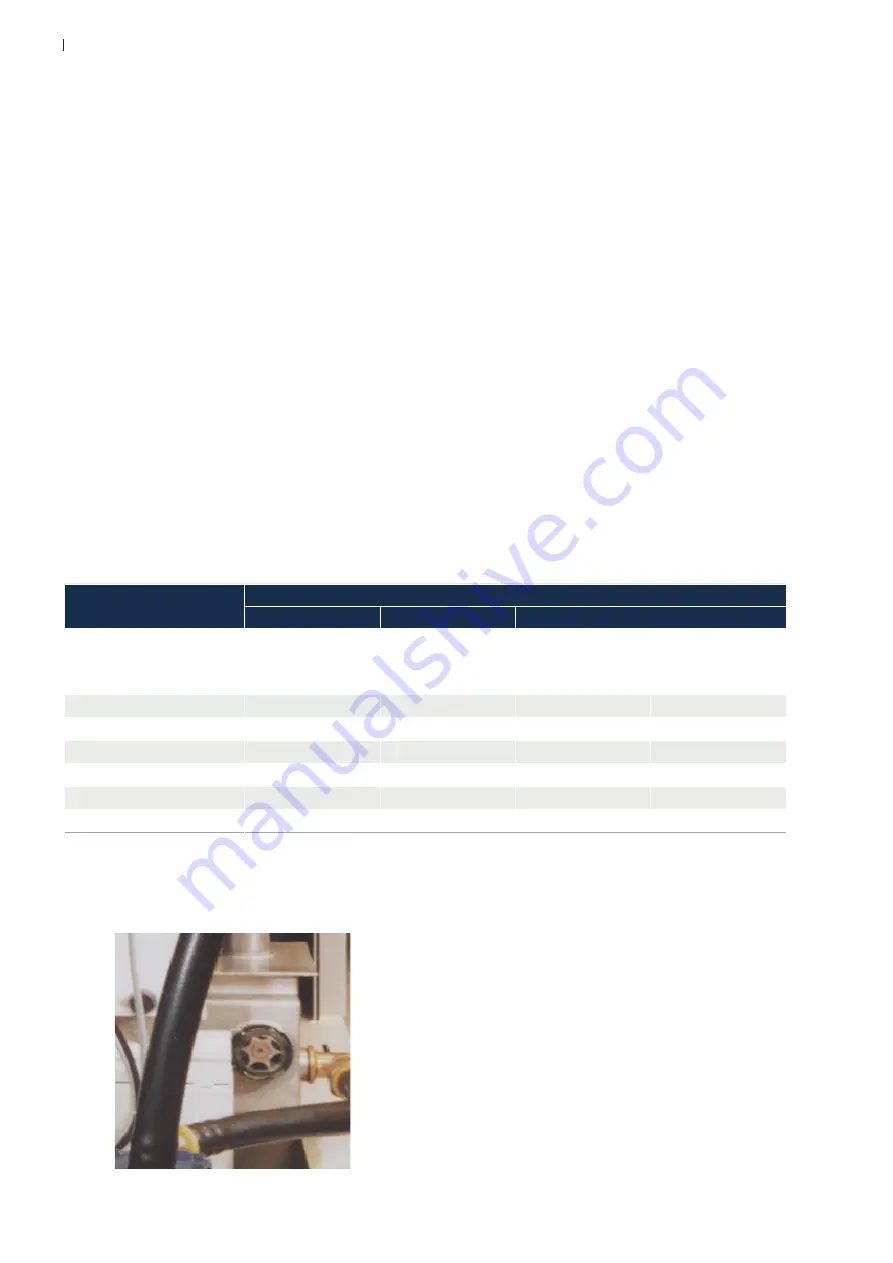
42
BECKER VADS 1500+
9
MAINTENANCE, SERVICING AND DISMANTLING
9.1 MAINTENANCE AND MAINTENANCE
The VADS 1500+ is built according to the state of the art and the recognised safety rules. As a prerequisite for safe and
proper operation, it is therefore essential that the machine is serviced and maintained at regular intervals by appropriately
qualified personnel. In addition, regular servicing and maintenance increases availability and extends the service life of
the VADS 1500+. The recommended service and maintenance intervals are listed in this chapter.
9.2 PREPARATIONS
The responsibilities of the personnel must be clearly defined at all times. The responsibilities for installation, operation,
maintenance and cleaning must be clearly regulated and defined and recorded in the table in chapter 2.4.
For maintenance and servicing measures, it must be ensured that sufficient space is available for all work. The space
for maintenance and servicing measures must be as free as possible from tripping and falling hazards. Possible tripping
and falling hazards must be pointed out. The maintenance area must be secured.
The following steps must be followed when preparing for maintenance and servicing activities:
1. All motors must be individually isolated. Maintenance during operation or when the machine is switched on is
strictly prohibited.
2. If safety devices have to be dismantled or modified for troubleshooting, they must be reattached, adjusted and
tested immediately after completion of the maintenance and servicing activities and before starting the VADS 1500+.
3. According to this, a verifiably qualified electrician may carry out activities on the VADS 1500+, taking into account
the 5 safety rules.
After completion of the activities, the VADS 1500+ may be put back into operation after a visual inspection.
9.3 MAINTENANCE INTERVALS
The following overview shows the maintenance intervals:
Component
Interval time
40h
40-200h
8000h (min. 1x/a)
Intake filter
check
clean
(change, min 2x/a)
Oil
Oil level check
change
Oil filter
change
Oil cooler
clean exterior
Oil cooler (filter mat)
change
Housing
clean
Electrocell (filter mat)
change
Table 9.1: Maintenance intervals
9.4 MAINTENANCE ACTIVITIES
The maintenance plan provides for the following activities:
Check oil level
The oil level must be checked through the oil sight glass (chapter
4.3.2 - item 8). The oil level can only be realistically represented
when the machine is at a standstill after an appropriate waiting
time and should not drop below 2/3 of the sight glass.
The oil is responsible for the lubrication of the bearings. Therefore,
the oil level must be checked and adjusted if necessary.
The following oil is recommended by Gebr:
Becker Lube G 70
Alternative oils according to ISO VG 68 can also be used in con-
sultation with the manufacturer.