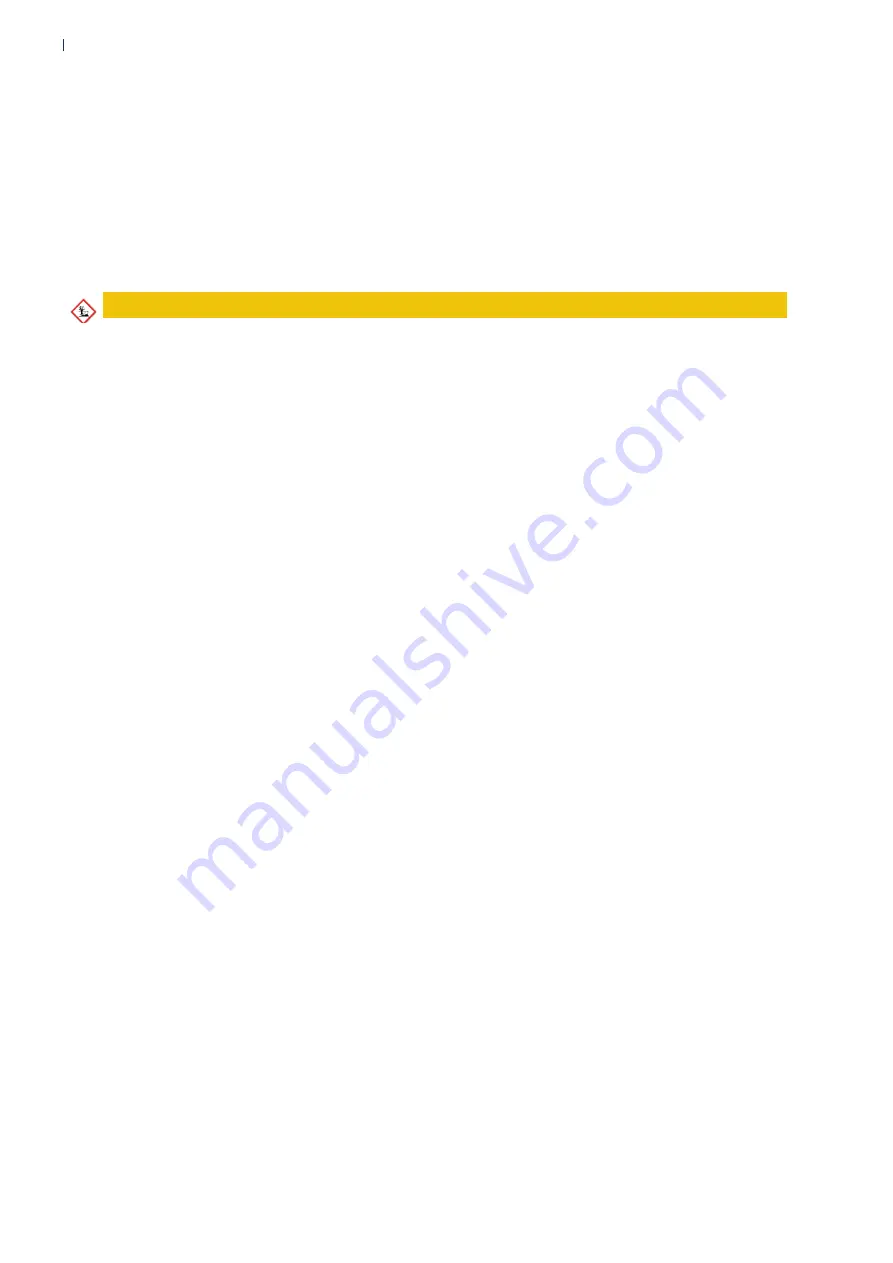
48
BECKER VADS 1500+
9.11 DISPOSAL
When disposing of the machine, pay attention to environmental protection and the relevant local statutory environ-
mental regulations.
Operating materials and chemicals must be taken to a designated collection point. Water contaminated with operating
materials must not enter the groundwater and must be disposed of in accordance with the operating materials.
All water-polluting substances must be stored and disposed of in watertight containers. The safety data sheets for ope-
rating materials and chemicals must be observed.
Components and assemblies must be separated and disposed of according to the type of waste. The local legal regu-
lations must be observed.
CAUTION
Contamination and damage to the environment by operating materials
The operating materials used for the proper functioning of the VADS 1500+ and water contaminated with these
operating materials can pose a danger to the environment.
Suitable absorbents must always be kept on hand to ensure rapid absorption of spills and contaminated water.
Used absorbents must always be disposed of according to the prescribed procedures.
All environmental protection regulations must always be observed when handling and disposing of operating
materials.
Operating materials and contaminated water must be disposed of in accordance with the environmental pro-
tection conditions applicable on site.