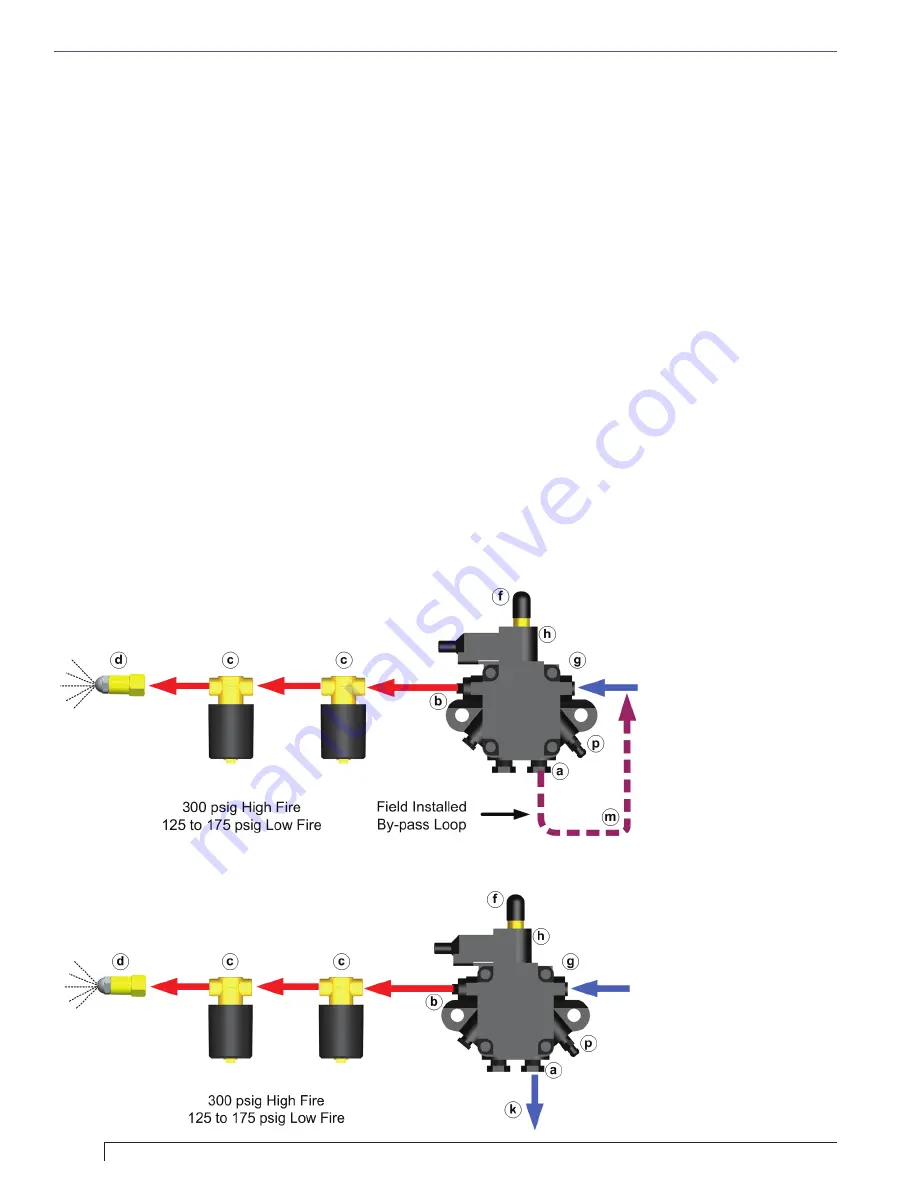
10
Special Note: The burner is shipped with a by-
pass plug installed in the fuel unit. For low/high
operation, the by-pass plug must be left in the fuel
unit, regardless of the fuel system used (one-pipe
with by-pass loop or two-pipe). Do not remove the
by-pass plug.
One-pipe Oil System By-pass Loop
Refer to
Figure 9
(item
m
). Note the addition of a
fi
eld-
installed by-pass loop (use 3/8” copper tubing) from the
fuel unit Return port to the Inlet port. This line is required
for low/high operation. It simulates the
fl
ow of a two-pipe
system at the fuel unit.
Oil Supply/Return Lines
Install the oil tank and oil lines in accordance with all
applicable codes.
Size the oil supply and return lines using the
guidelines given in the fuel unit literature included in
the literature envelope. Oil line
fl
ow rate will equal
the burner rate for one-pipe systems. For two-pipe
systems, refer to
Table 3
for the fuel unit gearset
capacity - the rate at which fuel is recirculated when
connected to a two-pipe system. Size two-pipe oil
lines based on this
fl
ow rate.
○
○
Legend (
Figure 9 & 10
)
a Return port
b Nozzle port
c Oil valves
d Nozzle & adapter
f
By-pass/Low
fi
re pressure
regulator
g Inlet port
h By-pass valve (“B” pump)
k Return line to oil tank
m One-pipe by-pass loop, 3/8”
p Air bleed valve
Figure 9 – One-pipe Oil Flow with “B” Pump
SK9940
Figure 10 – Two-pipe Oil Flow with “B” Pump
SK9939
Use continuous lengths of heavy-wall copper tubing,
routed under the
fl
oor where possible. Do not attach
fuel lines to the appliance or to
fl
oor joists if possible.
This reduces vibration and noise transmission
problems.
Install an oil
fi
lter sized to handle the fuel unit
gearset
fl
ow capacity (
Table 3
) for two-pipe systems.
However, size the
fi
lter for the
fi
ring rate for one-pipe
systems. Locate the
fi
lter immediately adjacent to
the burner fuel unit.
Install two high-quality shutoff valves in accessible
locations on the oil supply line. Locate one valve
close to the tank. Locate the other valve close to the
burner, upstream of the fuel
fi
lter.
Burner Fuel Flow
One-pipe systems
– See
Figure 9
for the fuel
fl
ow
paths for high-
fi
re and low-
fi
re operation. The low-
fi
re
by-pass regulation is done internally for type
B
fuel units.
Oil supply connects to one of the fuel unit Inlet ports.
Two-pipe systems
– See
Figure 10
for the fuel
fl
ow
paths for high-
fi
re and low-
fi
re operation. The low-
fi
re
by-pass regulation is done internally for type B fuel units.
Oil supply connects to one of the fuel unit Inlet ports.
Oil return connects to the fuel unit Return port. Do NOT
install valves in the return line.
○
○
○
Section: Mount the Burner