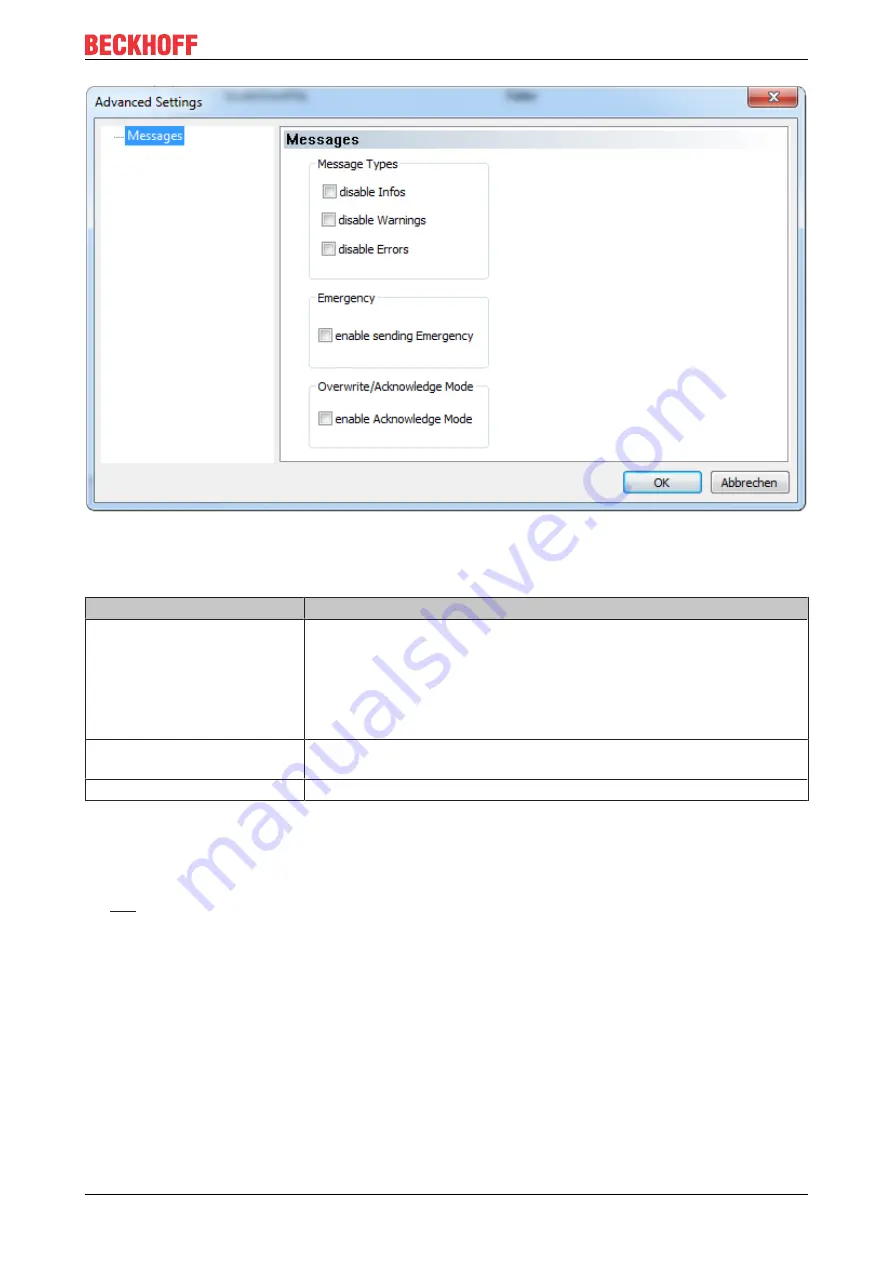
Operation
EP1918
43
Version: 1.1.0
Fig. 31: Diag history – advanced settings
Advanced Settings
Setting
Description
Message Types
• disable Info
Messages with the
Info
status are not saved in the diag history
• disable Warnings
Messages with the
Warning
status are not saved in the diag history
• disable Errors
Messages with the
Error
status are not saved in the diag history
Emergency
In addition to saving the message in the diag history, an emergency object
is also sent and displayed in the TwinCAT logger window.
Overwrite / Acknowledge Mode This setting is currently not supported.
4.5.8
Diagnosis History
The diagnostic history of the TwinSAFE devices that support this function is implemented in accordance with
the
guideline ETG.1020 Chapter 13 "Diagnosis Handling". The diagnostic messages are saved by the
TwinSAFE device in a dedicated CoE object under 0x10F3 and can be read out by the application or by
TwinCAT.
Both the control entries and the history itself can be found in the CoE object 0x10F3. The entry Newest
Message (0x10F3:02) contains the subindex of 0x10F3, which contains the latest diagnostic message, e.g.
0x06 for diagnostic message 1.
Summary of Contents for EP1918
Page 2: ......
Page 30: ...Operation EP1918 30 Version 1 1 0 Fig 19 Creating alias devices by the user ...
Page 53: ...Appendix EP1918 53 Version 1 1 0 5 3 Certificates ...
Page 55: ......