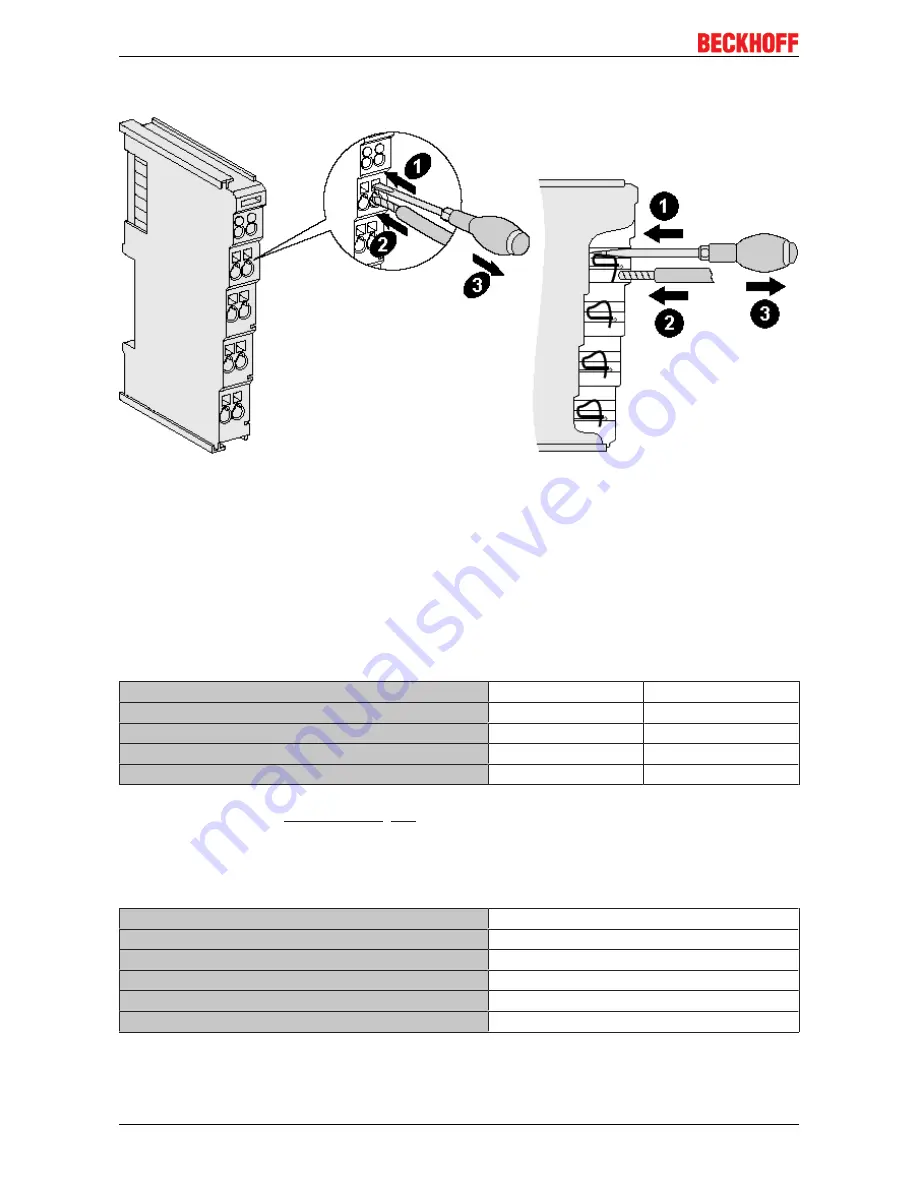
Mounting and wiring
KL2542
16
Version: 2.0.0
Terminals for standard wiring ELxxxx/KLxxxx and for pluggable wiring ESxxxx/KSxxxx
Fig. 9: Connecting a cable on a terminal point
Up to eight terminal points enable the connection of solid or finely stranded cables to the Bus Terminal. The
terminal points are implemented in spring force technology. Connect the cables as follows:
1. Open a terminal point by pushing a screwdriver straight against the stop into the square opening
above the terminal point. Do not turn the screwdriver or move it alternately (don't toggle).
2. The wire can now be inserted into the round terminal opening without any force.
3. The terminal point closes automatically when the pressure is released, holding the wire securely and
permanently.
See the following table for the suitable wire size width.
Terminal housing
ELxxxx, KLxxxx
ESxxxx, KSxxxx
Wire size width (single core wires)
0.08 ... 2.5 mm
2
0.08 ... 2.5 mm
2
Wire size width (fine-wire conductors)
0.08 ... 2.5 mm
2
0,08 ... 2.5 mm
2
Wire size width (conductors with a wire end sleeve)
0.14 ... 1.5 mm
2
0.14 ... 1.5 mm
2
Wire stripping length
8 ... 9 mm
9 ... 10 mm
High Density Terminals (
HD Terminals [
}
15]
) with 16 terminal points
The conductors of the HD Terminals are connected without tools for single-wire conductors using the direct
plug-in technique, i.e. after stripping the wire is simply plugged into the terminal point. The cables are
released, as usual, using the contact release with the aid of a screwdriver. See the following table for the
suitable wire size width.
Terminal housing
High Density Housing
Wire size width (single core wires)
0.08 ... 1.5 mm
2
Wire size width (fine-wire conductors)
0.25 ... 1.5 mm
2
Wire size width (conductors with a wire end sleeve)
0.14 ... 0.75 mm
2
Wire size width (ultrasonically “bonded" conductors)
only 1.5 mm
2
Wire stripping length
8 ... 9 mm
Summary of Contents for KL2542
Page 2: ......