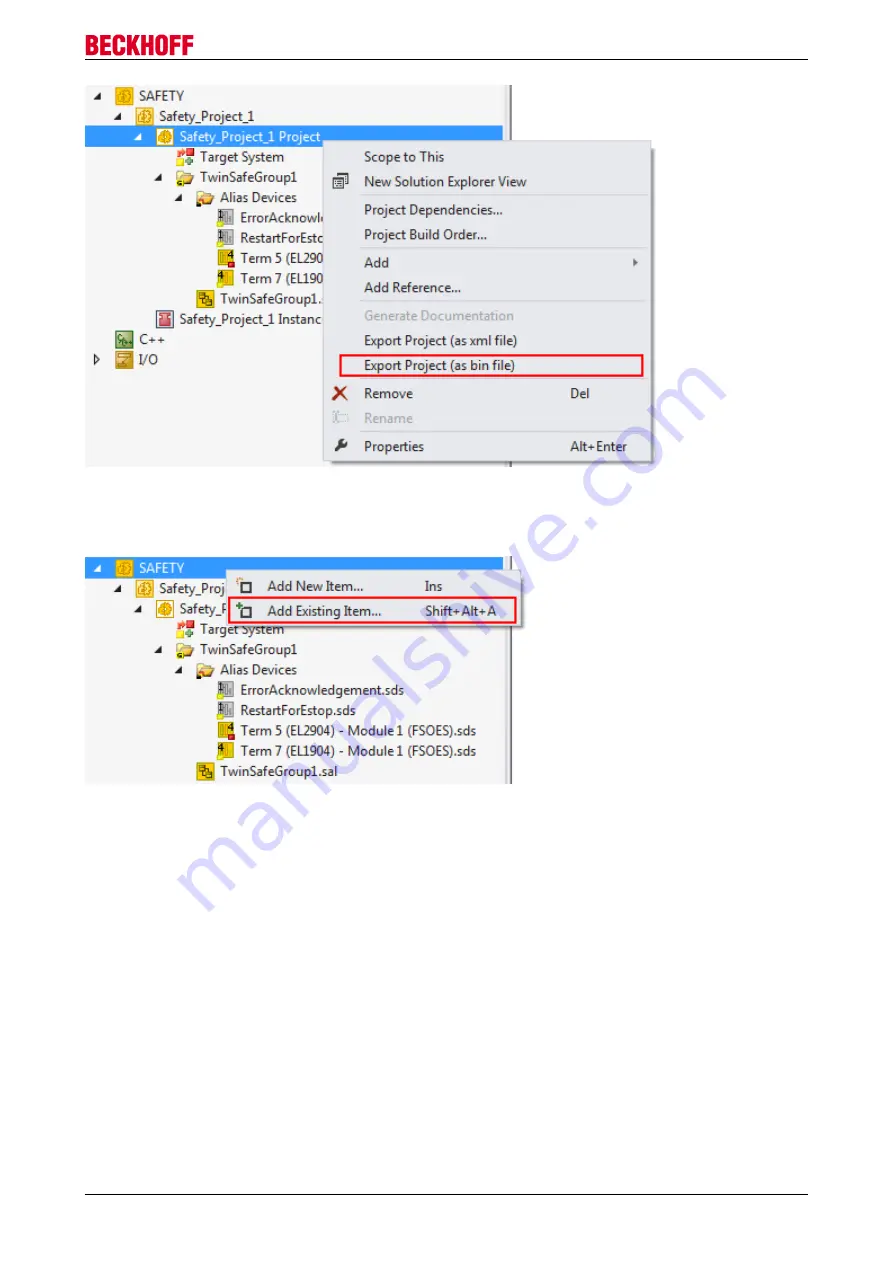
Operation
EL6910
101
Version: 1.8.0
Fig. 135: Saving the safety project in a binary format (e.g. for the TwinSAFE loader)
A previously exported safety project can be imported via the context menu of the main Safety entry in the
TwinCAT project structure.
Add Existing Item…
can be used to select the file type for the import.
Fig. 136: Selecting the file type for importing a safety project
The following file types are supported:
• Safety project files *.splc,
• Safety project archives *.tfzip
• Safety projects in XML format
Summary of Contents for TwinSAFE EL6910
Page 1: ...Operation Manual for EL6910 TwinSAFE Logic Terminal 1 8 0 2019 01 09 Version Date...
Page 2: ......
Page 69: ...Operation EL6910 69 Version 1 8 0 Fig 73 The Safety Project Online View tab...
Page 136: ...Appendix EL6910 136 Version 1 8 0 5 2 Certificates...
Page 137: ...Appendix EL6910 137 Version 1 8 0...