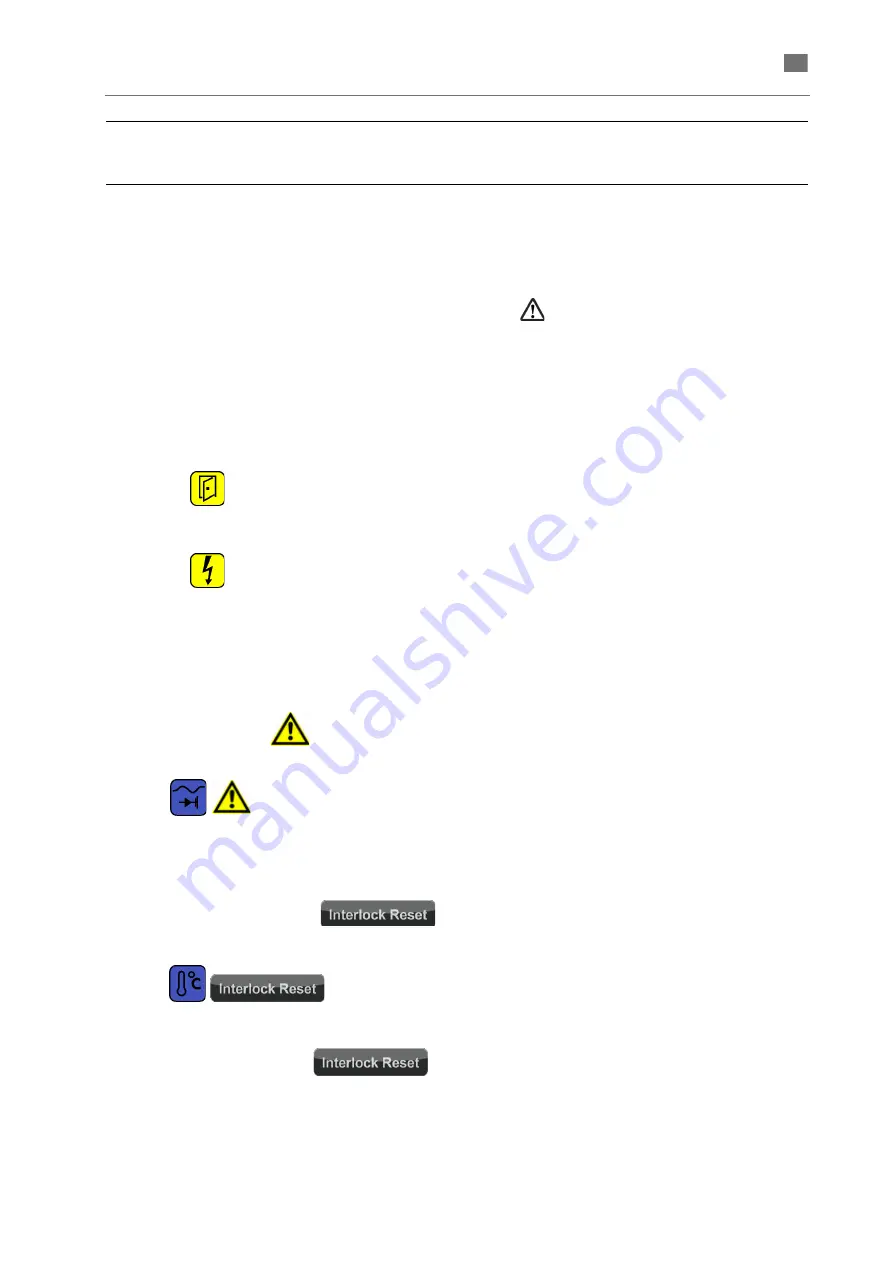
53
860
76
D
B
-en/
03
35
5.0
00
32
English
⋅
en
Status and error messages/
Fault clearance
General information
Status and error messages are displayed as
symbols at the top edge of the touchscreen.
The different types of status and error messages are
characterized by the following colors and displays.
Status messages
Messages that display normal operating states are
show as individual symbols without additional infor-
mation.
Error notes
This type of messages indicates states that may
cause subsequent malfunctions. The laser,
however, temporarily remains operable.
In this cases the symbol
is displayed in
addition to the specific error symbol.
Example:
= water flow too low.
Interlock error messages
In the case of malfunctions that cause the device to
turn off for security reasons, the
button is displayed in addition to the specific error
symbol.
Example:
= permissible
cooling water temperature exceeded.
The device will only work after eliminating the fault
and subsequently pressing the
button.
In the table in the following section, this error classi-
fication is referred to in the column Type by the
symbol
or the abbreviation IL.
The arising error measures are saved and can be
viewed in the History window of the --> SERVICE
MENU USER.
Examples:
= Safety circuit interrupted (such
as working chamber door not
closed)
lamp not yet ignited.