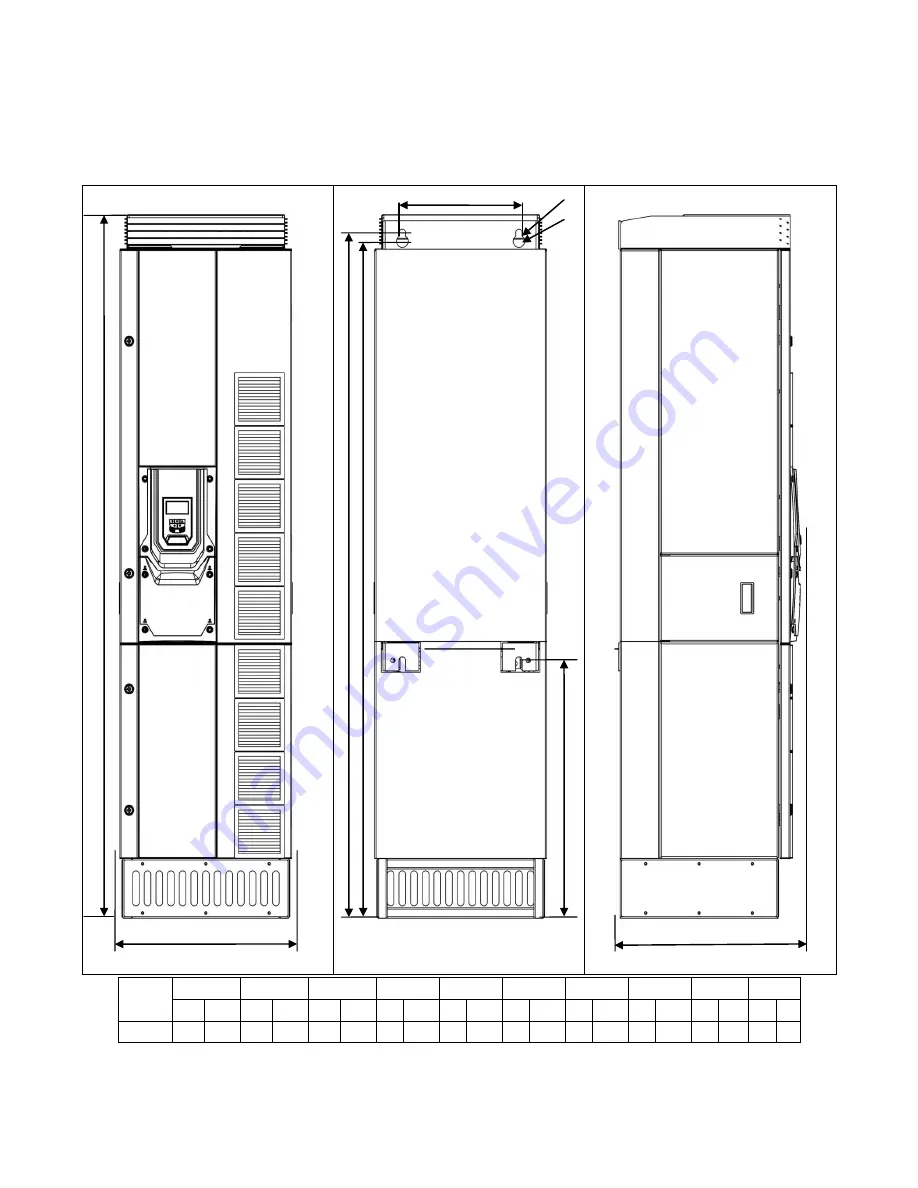
User Guide Revision 1.12
13
Control Terminal Torque Settings:
All Sizes:
0.8 Nm (7 lb-in)
Power Terminal Torque Settings:
Frame Size 4:
1.2 – 1.5 Nm
Frame Size 5:
2.5 – 4.5 Nm
Frame Size 6:
8 Nm
Frame Size 7:
8 Nm
3.7.
Mechanical dimensions and mounting – IP40 Units
Drive Size
A
B
C
D
E
F
G
H
I
J
mm
in
mm
in
mm
in
mm
in
mm
in
mm
in
mm
in
mm
in
mm
in
mm in
8
2000 78.74 1925 75.79 1950 76.77 733 28.86 516 20.31 500 19.69 350 13.78 406 15.98 35 1.38 19 0.75
Control Terminal Torque Settings:
All Sizes: 0.8Nm (7lb-in)
Power Terminal Torque Settings:
All Sizes: 50Nm (37 lb-ft)
E
ØI
ØH
G
F
A
C
D
B
Summary of Contents for HVAC H2
Page 1: ......
Page 72: ...User Guide Revision 1 12 72 82 H2MAN BE_V1 11...