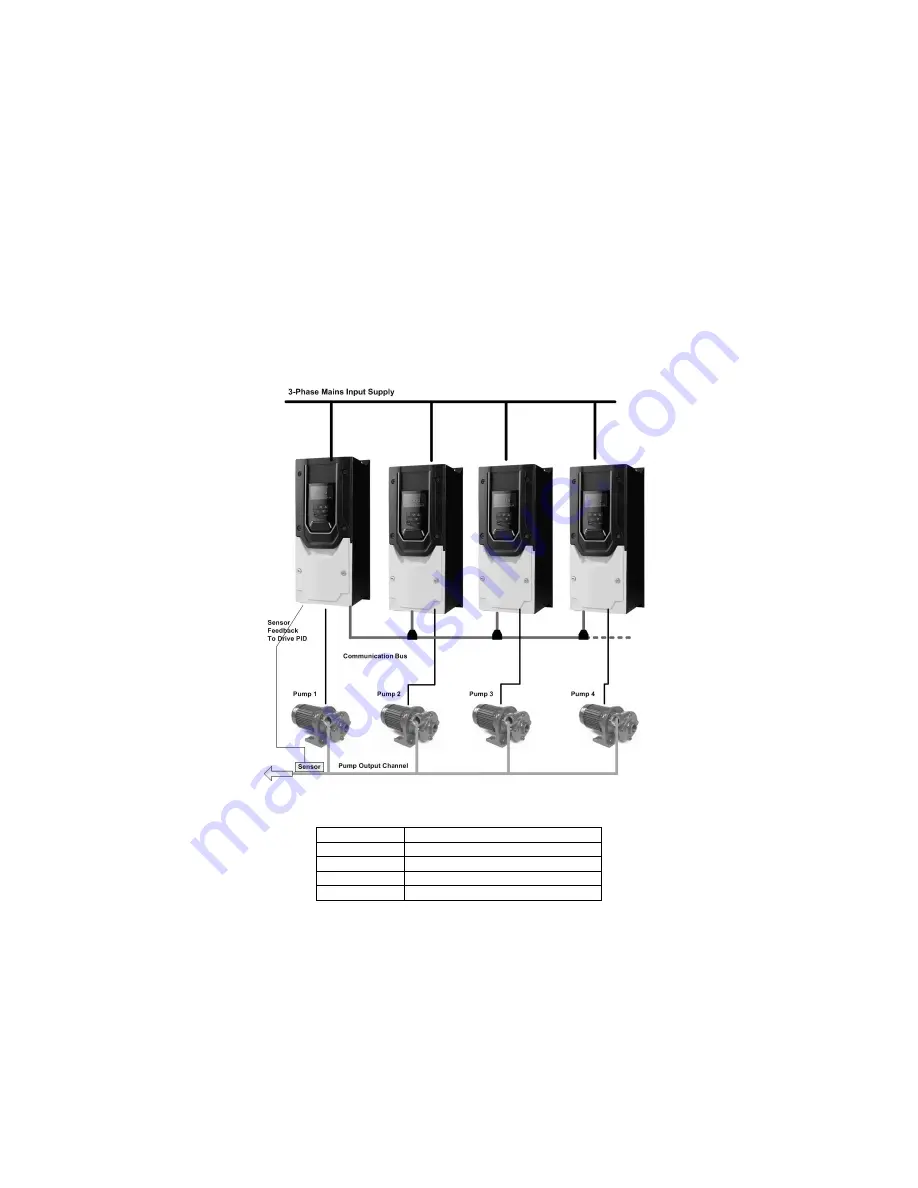
User Guide Revision 1.12
31
Set Basic parameters P1-01 to P1-10. Energy Optimiser P1-06 must remain disabled.
Set Parameter P1-14= 101 to allow access to extended parameters
In Menu 3, Configure parameters for the PID Control
If drive relay 2 is used as part of the slave DOL cascade then set P2-18 = 8
Set parameter P8-14=1 to enable the Pump staging – DOL cascade function
Set the number of DOL slave pumps available in the system (not including Master VFD pump) in P8-15
Set the drive operating speed limits used to activate / deactivate DOL slave pumps as follows:
o
P8-17: Pump Staging DOL Switch In Speed – Threshold to bring in DOL Slave pump
o
P8-18: Pump Staging DOL Switch Out Speed – Threshold to switch out DOL Slave pump
Set a pump staging settle time (minimum 10 seconds) in P8-19. The time entered in P8-19 must be sufficient for the PID feedback
signal from the system output sensor to settle to a steady level.
If the duty run times between DOL slave pumps are to be balanced then the maximum permissible difference in hours should be
entered in P8-16.
7.2.
Pump Staging – Multiple Drive Cascade
Summary:
The below illustration shows the use of several drive units as controllers in a variable speed pump staging system. All pumps in this
configuration are controlled by the drive units in variable speed mode with co-ordination and communication carried out over the built in
RS485 communications link as shown below.
Drives can be connected using the RJ45 data cables and the RS485 Data Cable Splitter as shown above up to a maximum of 5 drives. Part
numbers are as follows:
Product Code
Description
OPT-J45SP-BFI
RJ45 Splitter Box 1 – 2 Way
OPT-J4505-BFI
RJ45 to RJ45 RS485 Data Cable, 0.5m
OPT-J4510-BFI
RJ45 to RJ45 RS485 Data Cable, 1m
OPT-J4530-BFI
RJ45 to RJ45 RS485 Data Cable, 3m
Each motor / pump in this configuration is controlled by a dedicated HVAC drive (one drive per pump). All drives run in variable speed mode
with the speed reference passed across the communications network.
One drive in the system is denoted the ‘Network Master’. The Network Master has the Feedback sensor input connected to it along with the
input set-point control, and uses its PID function to generate the operating speed for the system. The ‘Network Master’ provides an enable
status and speed reference to the other drives on the network.
Operational Overview:
The pump staging with multiple drive cascade function is enabled by setting parameter P8-14=2 (Pump staging function select)
on the network
master drive only
. All drives other than the network master drive must be set to communications slaves by setting parameter P1-12= 5 ‘slave
mode).
In addition, the value of P8-15 on the network master, ‘Pump staging DOL pump availability’ must be set with the number of additional drives
available in the system (slave drives), excluding the master (set to a value other than 0). The master drive must be set to drive address 1
(default), with the addresses of the slave drives set in sequence to subsequent addresses (2. 3. 4. 5...). Addresses are set within P5-01.
Summary of Contents for HVAC H2
Page 1: ......
Page 72: ...User Guide Revision 1 12 72 82 H2MAN BE_V1 11...