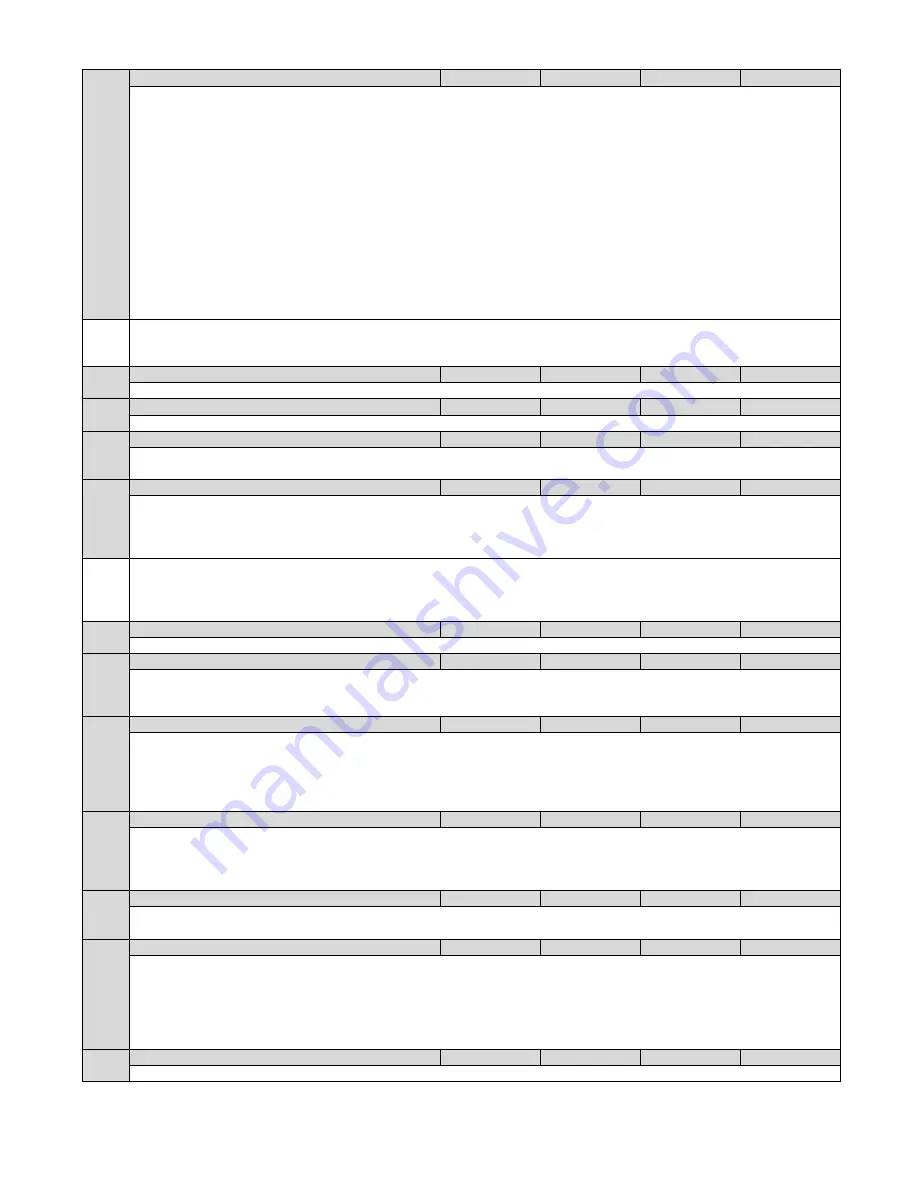
User Guide Revision 1.12
52
P2-18
Relay Output 2 Function (Terminals 17 & 18)
0
8
0
-
Selects the function assigned to Relay Output 2. The relay has two output terminals, Logic 1 indicates the relay is active, and therefore
terminals 17 and 18 will be linked together.
0
: Drive Enabled (Running)
. Logic 1 when the motor is enabled
1 : Drive Healthy
. Logic 1 when power is applied to the drive and no fault exists
2
: At Target Frequency (Speed)
. Logic 1 when the output frequency matches the set-point frequency
3: Output Frequency > 0.0 Hz
. Logic 1 when the drive output frequency to the motor is exceeds 0.0Hz
4
: Output Frequency >= Limit
. Logic 1 when the motor speed exceeds the adjustable limit
5
: Output Current >= Limit
. Logic 1 when the motor current exceeds the adjustable limit
6
: Reserved
. No Function
7
: Analog Input 2 Signal Level >= Limit
. Logic 1 when the signal applied to the Analog Input 2 exceeds the adjustable limit
8 : Assist Pump 1 Control (DOL1)
.
See section 7.1, Pump staging –DOL Cascade.
9 : Fire Mode Active.
Logic 1 when the drive in running in Fire Mode (Fire Mode input is active).
10 :
Maintenance Due.
Logic 1 when Maintenance Timer expires indicating that Maintenance is now due.
11 : Drive Available.
Logic 1 when drive is in Auto-mode, no trips are present, and the safety circuit is enabled indicating that drive is
ready for automatic control.
Note:
When using settings 4 – 7, parameters P2-19 and P2-20 are used to control the output behaviour. The output will switch to Logic 1
when the selected signal exceeds the value programmed in P2-19, and return to Logic 0 when the signal falls below the value
programmed in P2-20.
P2-19
Adjustable Threshold 2 Upper Limit (AO2 / RO2)
P2-20
200
100.0
%
Setting the upper limited value for P2-13 and P2-18, please refer to P2-13 or P2-18.
P2-20
Adjustable Threshold 2 Lower Limit (AO2 / RO2)
0
P2-19
0.0
%
Setting the lower limited value for P2-13 and P2-18, please refer to P2-13 or P2-18.
P2-21
Display Scaling Factor
-30.000
30.000
0.000
-
Determines the factor for scaling display.
The variable selected in P2-22 is scaled by the factor set in P2-21.
P2-22
Display Scaling Source
0
2
0
-
Source value used when custom units are to be shown on the drive display.
0: Motor Speed
1: Motor Current
2: Analog Input 2
Note:
P2-21 & P2-22 allow the user to program the drive display to show an alternative output unit scaled from an existing parameter (for
example, to display conveyer speed in metres per second based on the output frequency).
This function is disabled if P2-21 is set to 0. If P2-21 is set >0, the variable selected in P2-22 is multiplied by the factor entered in P2-21,
and is shown on the drive display whilst the drive is running.
P2-23
Zero Speed Holding Time
0.0
60.0
0.2
Seconds
Determines the time for which the drive output frequency is held at zero when stopping, before the drive output is disabled
P2-24
Switching Frequency
4kHz
[Drive Dependent]
[Drive Dependent]
Default
Effective power stage switching frequency. Higher frequencies reduce audible noise from the motor, and improve the output current
waveform, at the expense of increased drive losses.
Note: De-rating of the drive output current may be required when increasing P2-24 beyond the minimum setting.
P2-25
Fast Decel Ramp Time
0.0
30.0
0.0
Seconds
This parameter allows an alternative deceleration ramp down time to be programmed into the drive.
Fast Deceleration ramp is selected Automatically in the case of a mains power loss if P2-38 = 2.
When ramp rate in P2-25 is set to 0.0, the drive will coast to stop.
Fast deceleration ramp can also be selected using the user defined logic configuration parameters in menu 9 (P9-02), or selection
configured through the drive PLC function using the OptiTools Studio Suite PC software.
P2-26
Spin Start Enable
0
1
1
-
0 : Disabled
1 : Enabled
. The drive will attempt to determine if the motor is already rotating on start up and to detect rotational speed and
direction. The drive will begin control of the motor from its current (detected) speed. A short delay may be observed when starting the
drive whilst the spin start function is completed.
P2-27
Standby Mode Enable
0.0
250.0
0.0
Seconds
This parameter defines the time period, whereby if the drive operates at minimum speed for greater than the set time period, the
Drive output will be disabled, and the display will show
.
The function is disabled if P2-27 = 0.0.
P2-28
Slave Speed Scaling
0
3
0
-
Active in Keypad mode (P1-12 = 1 or 2) and Slave mode (P1-12=4) only. The keypad reference can be multiplied by a preset scaling
factor or adjusted using an analog trim or offset.
0 : Disabled
. No scaling or offset is applied.
1 : Actual Speed = Digital Speed x P2-29
2 : Actual Speed = (Digital Speed x P2-29) + Analog Input 1 Reference
3 : Actual Speed = (Digital Speed x P2-29) x Analog Input 1 Reference
P2-29
Slave Speed Scaling Factor
-500.0
500.0
%
100.0
Slave speed scaling factor used in conjunction with P2-28.
Summary of Contents for HVAC H2
Page 1: ......
Page 72: ...User Guide Revision 1 12 72 82 H2MAN BE_V1 11...