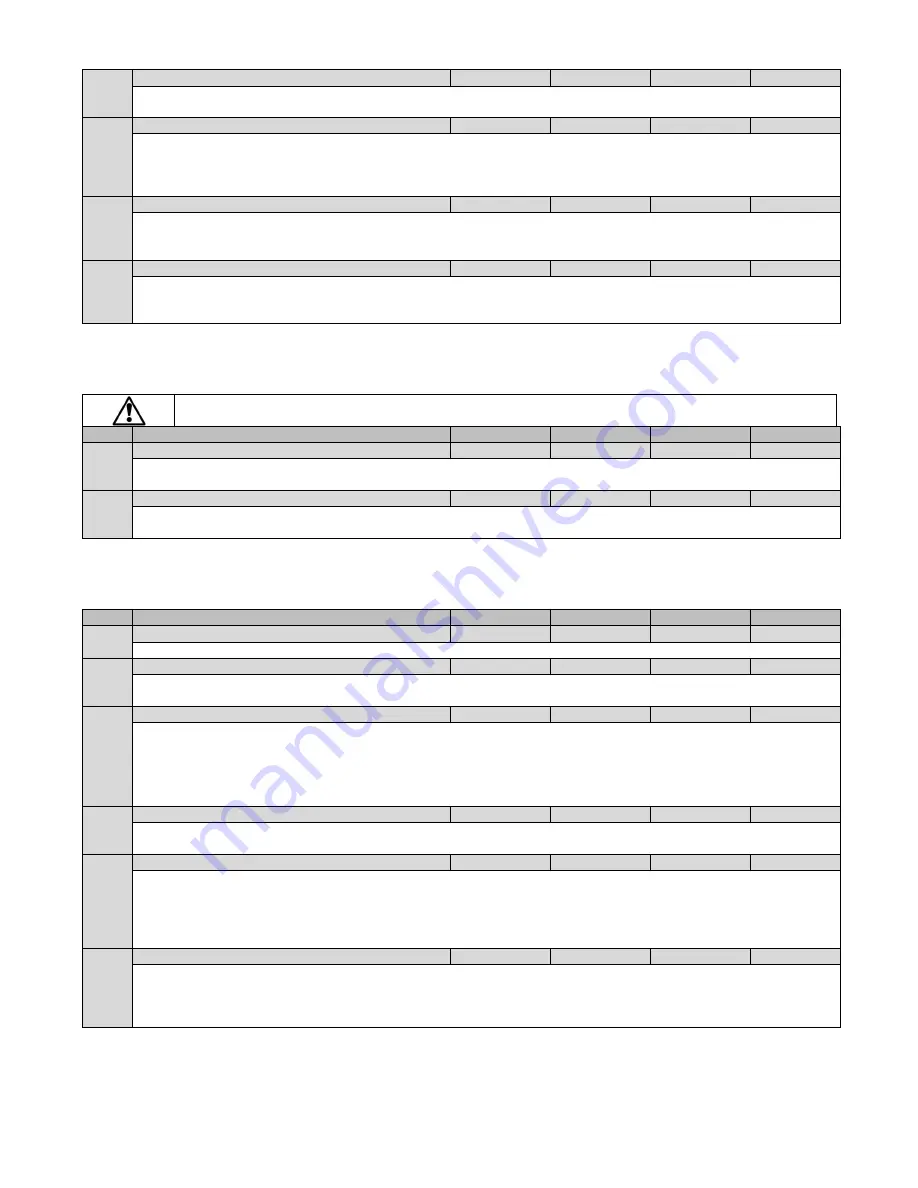
User Guide Revision 1.12
55
P3-15
2
nd
PID Digital Reference Value
0.0
100.0
0.0
%
When P3-05 = 0, and the 2
nd
digital reference is selected (see Digital Input Functions – Section 10.1) this parameter sets the preset
digital reference (set-point) used for the PID Controller
P3-16
Pump Prime Time
0
600
0
Seconds
A value other than zero in this parameter will automatically enable burst pipe protection function. Each time the drive is enabled
whilst in PID control or is switched to PID control, the drive will monitor the PID feedback level for the time entered in P3-16. If the
PID feedback level does not exceed the threshold entered in P3-17 before the time in P3-16 expires then the drive will trip with "Pr-
Lo" (pressure low) trip.
P3-17
Burst Pipe Threshold
0.0
100.0
0.0%
%
PID feedback threshold for the burst pump control. In direct PID mode, PID feedback should be less than or equal to this threshold
before the pump prime time (P3-16) expires. In inverse PID mode, PID feedback should be larger than or equal to the threshold
before the pump prime time (P3-16) expires.
P3-18
PID Reset Control
0
1
0
-
This parameter is used to control the reset behaviour of the PID loop.
0: PID loop will continue running as long as P gain (P3-01) is not zero.
1: PID loop will only run when drive is enabled. If drive is not running, PID output will reset to 0 (Including integral result)
11.3.
Parameter Group 4 – High Performance Motor Control
Incorrect adjustment of parameters in menu group 4 can cause unexpected behaviour of the motor and any connected
machinery. It is recommended that these parameters are only adjusted by experienced users.
Par
Parameter Name
Minimum
Maximum
Default
Units
P4-02
Auto-tune Enable
0
1
0
-
When set to 1, the drive immediately carries out a non-rotating auto-tune to measure the motor parameters for optimum control and
efficiency. Following completion of the auto-tune, the parameter automatically returns to 0.
P4-07
Maximum Motoring Current Limit
20
150
150
%-
When set to 1, the drive immediately carries out a non-rotating auto-tune to measure the motor parameters for optimum control and
efficiency. Following completion of the auto-tune, the parameter automatically returns to 0.
11.4.
Parameter Group 5 – Communication Parameters
Par
Parameter Name
Minimum
Maximum
Default
Units
P5-01
Drive Fieldbus Address
0
63
-
1
Sets the Fieldbus address for the drive
P5-03
Modbus RTU / BACnet Baud rate
9.6
115.2
115.2
kbps
Sets the baud rate when Modbus/BACnet communications are used
9.6kbps, 19.2kpbs, 38.4kpbs, 57.6kpbs, 115 kbps
P5-04
Modbus RTU / BACnet Data Format
-
-
-
Sets the expected Modbus or BACnet telegram data format as follows
: No Parity, 1 stop bit
: No parity, 2 stop bits
: Odd parity, 1 stop bit
: Even parity, 1 stop bit
P5-05
Communications Loss Timeout
0.0
5.0
1.0
seconds
Sets the watchdog time period for the communications channel. If a valid telegram is not received by the drive within this time
period, the drive will assume a loss of communications has occurred and react as selected below (P5-07)
P5-06
Communications Loss Action
0
3
0
-
Controls the behaviour of the drive following a loss of communications as determined by the above parameter setting (P5-06).
0: Trip & Coast To Stop
1: Ramp to Stop Then Trip
2: Ramp to Stop Only (No Trip)
3: Run at Preset Speed 4
P5-07
Fieldbus Ramp Control
0
1
0
-
Selects whether the acceleration and deceleration ramps are control directly via the Fieldbus, or by internal drive parameters P1-03
and P1-04.
0 : Disabled
. Ramps are control from internal drive parameters
1 : Enabled
. Ramps are controlled directly by the Fieldbus
Summary of Contents for HVAC H2
Page 1: ......
Page 72: ...User Guide Revision 1 12 72 82 H2MAN BE_V1 11...