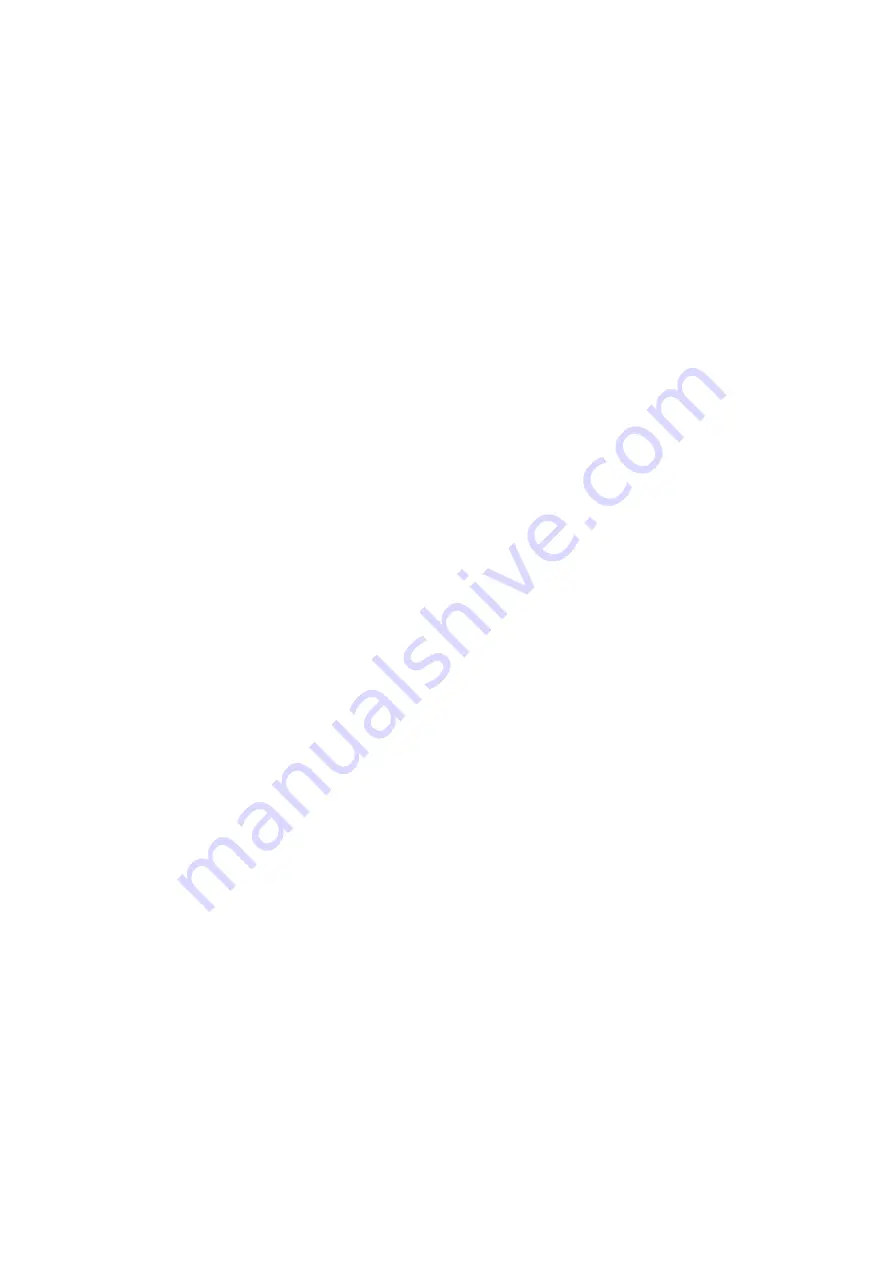
51
APPENDIX 1
ATEX Dust Certification
A1.0 ATEX dust certification
In addition to ATEX Ex nA certification permitting
installation in Zone 2 explosive gas atmospheres,
which is described in the main section of this
instruction manual, the BA384NG Rate Totaliser has
ATEX Ex tc dust ignition protection by enclosure
certification permitting installation in Zone 22
combustible dust atmospheres. The front panel
push button switches are non incendive and have
been certified intrinsically safe Ex ic without the
need for Zener barriers or galvanic isolators.
This appendix describes ATEX installations in
explosive dust atmospheres conforming with
EN 60079-14
Electrical installations design,
selection and erection
. When designing systems for
installation outside the UK the local Code of Practice
should be consulted.
The Rate |Totaliser’s Ex tc dust input and output
safety parameters are identical to the Ex nA gas
parameters, therefore all the electrical circuits shown
in the main section of this manual may also be used
for Ex tc dust applications.
A1.1
Zones, and Maximum Surface
Temperature
The BA384NG has been ATEX dust certified
Group II, Category 3D
Ex ic tc IIIC T80ºC Dc -40
≤
Ta
≤
60°C
When connected to a suitable system the Rate
Totaliser may be installed in:
Zone 22
explosive atmosphere in the form of a
cloud of combustible dust in air is not
likely to occur in normal operation, but
if it does occur, will only persist for a
short period.
Be used with dust in subdivisions:
IIIA
combustible flyings
IIIB
non-conductive dust
IIIC
conductive dust
Having a Minimum Ignition Temperature of:
Dust cloud
120°C
Dust layer on indicator
155
°
C
up to 5mm thick
Dust layer on indicator
Refer to
over 5mm thick.
EN 60079-14
At an ambient temperature between -40 and +60°C
A1.2 Special conditions for safe use in dust
atmospheres.
Special conditions for safe use are specified by the
Ex ic tc certificate indicated by the certificate
number's 'X' suffix. These state that the BA384NG
Rate |Totaliser should be:
a. Supplied from a
limited energy
circuit with
output parameters in normal operation equal to,
or less than the instrument’s input parameters.
The certificate states that It is
not
necessary to
power the instrument from an intrinsically safe
interface, such as a certified shunt diode safety
barrier or a galvanic isolator to comply with this
requirement.
b. Fitted with cable entry glands or conduit fittings
which maintain the impact and ingress
protection of the enclosure. Certified Ex e or
Ex n components satisfy these requirements.
The BA384NG is supplied fitted with one
certified M20 stopping plug and one temporary
hole plug which should be replaced with the
required gland or conduit fitting.
A1.3 Maintenance
The IEC guidance on maintenance procedures
EN 60079-17 permits live maintenance in Zone 22 if
a risk analysis demonstrates that this does not
introduce an unacceptable risk. The removal of
covers [opening of Ex tc enclosure] is permitted if
this can be done without contaminating the interior
of the enclosure and instrument with dust or
moisture. Some end-users may prefer not to permit
live maintenance to minimise risk.
ENSURE PLANT SAFETY BEFORE
STARTING MAINTENANCE
Live maintenance within the hazardous
area should only be performed when it is
permitted by risk analysis or when there is
no risk of a flammable atmosphere being
present.
The instrument assembly should only be removed
from the enclosure back-box when dust can not
enter the instrument enclosure. Before replacing the
instrument assembly the sealing gasket should be
inspected to ensure that it is undamaged and free
from foreign bodies.
Inspection of the Rate |Totalisers mechanical
condition and removal of accumulated dust from the
front of the instrument and the outside of the
enclosure should be regularly performed. The
interval between inspections depends upon
environmental conditions. Removal of flammable
dust should be performed with care to avoid creating
a dust cloud.