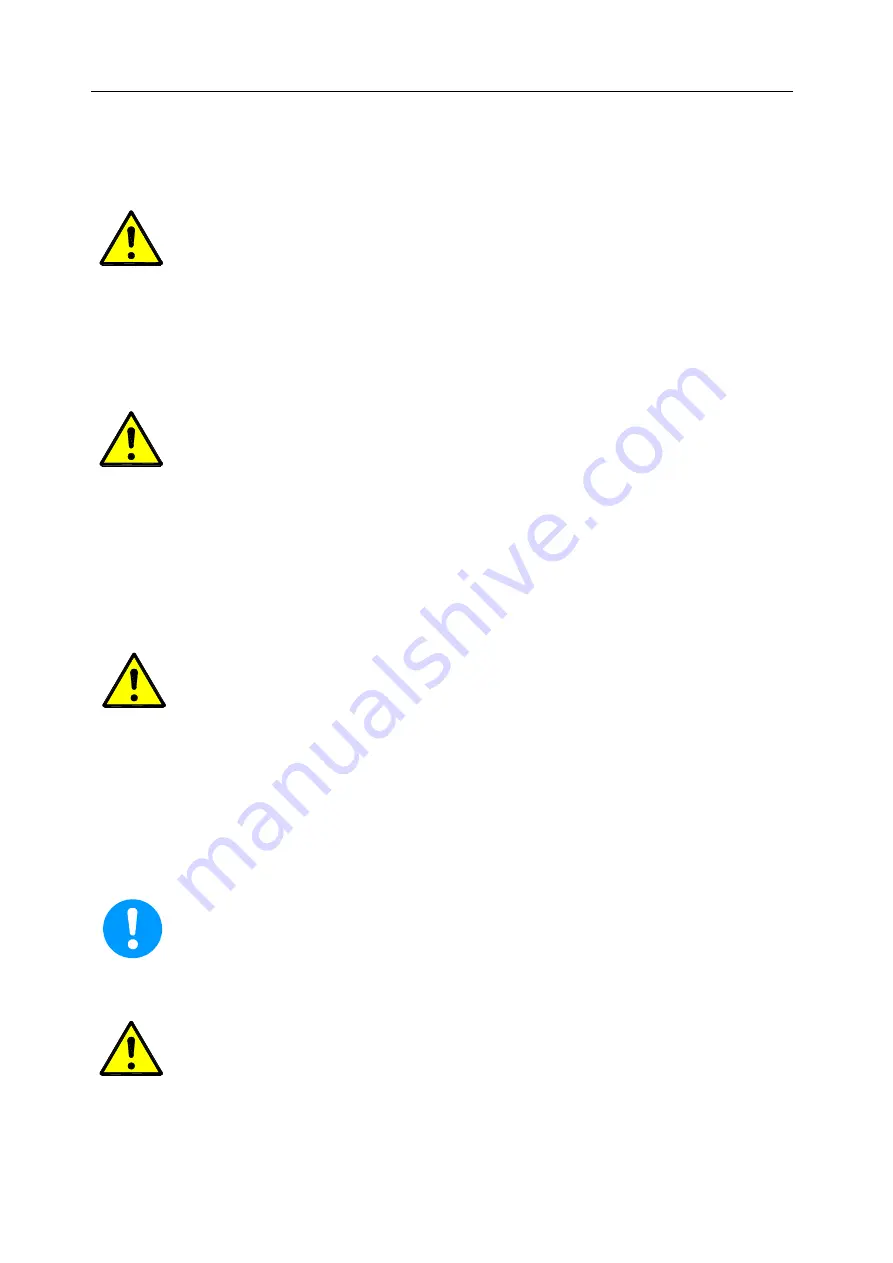
Safety instructions
10
CLEARPOINT® L 205 – L295 V
Unauthorised interventions, modification and abuse of the pressure device are prohibited.
Operators of the devices must observe the local and national pressure equipment
regulations in the country of installation.
Danger!
High pressure!
Subsequent to the start-up, components of the plant are under pressure.
Risk of serious injury or death through contact with quickly or suddenly escaping
compressed air or through bursting and/or unsecured plant components.
Any installation, repair and maintenance works must only be carried out when the plant is
disconnected, pressureless and de-energised.
Warning!
Improper use and application!
Improper use and application can lead to injury and damage to plants.
The following use is considered improper and is therefore prohibited:
Exceeding the max. permissible operating pressure
Exceeding the max. permissible operating temperature
Exceeding the max. permissible volume flow
All individual cases of application which are described as improper
Caution!
Improper transport!
Improper transport can lead to injury and damage to plants.
The CLEARPOINT
®
V must only be transported and installed by qualified and authorised
skilled personnel.
Only use suitable and technically unobjectionable lifting tools!
Only use lifting tools with a sufficient carrying capacity!
The respective national regulations and directives in force must be adhered to. Otherwise,
personal injuries may occur.
NOTE!
Damage through defective components!
Under no circumstances should you start up a damaged CLEARPOINT
®
V. Defective
components can impair the operational reliability and cause further damage.
Caution!
Incorrect installation!
Incorrect installation of the CLEARPOINT V
®
may endanger persons.
Ensure that the personnel in charge of the installation of the CLEARPOINT
®
V are sufficiently
instructed and competent for this task.