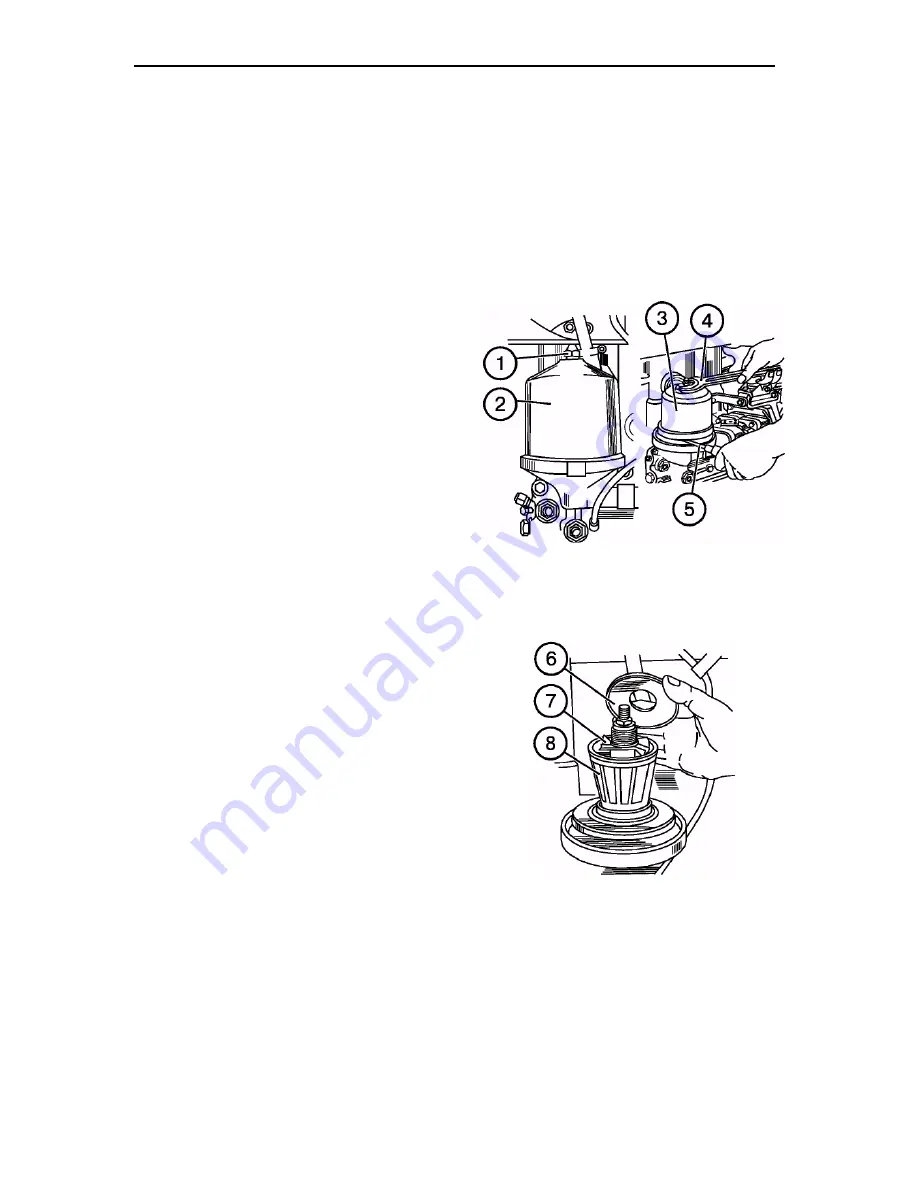
Section G. Maintenance Belarus– 510/512 Operating manual
88
Maintenance No. 2 (MS-2) after
each 500 service hours
Perform the previous MS actions plus as
follows:
Operation 15. Centrifugal oil filter of
engine
• Unscrew the nut (1) and remove the
cap (2).
• Insert the screwdriver (5) or a rod be-
tween the filter body and the rotor bot-
tom to lock the rotor (3) against rota-
tion and remove the rotor barrel (3) by
turning the rotor nut with spanner (4).
• Remove the cover (6), impeller (7)
and filtering grid (8) of the rotor. If
necessary, clean and flush the grid.
• Remove deposits from the inner walls
of the rotor barrel using a non-
metallic scraper.
• Clean all the parts in a detergent solu-
tion and blow with compressed air.
• Reassemble the filter by performing
the same operations in the reverse or-
der. Prior to assembling the barrel with
the rotor casing, lubricate the seal ring
with motor oil.
• Align the balancing marks of the bar-
rel with those on the rotor casing.
Tighten the barrel-fastening nut with
a slight force until the barrel is fully
set on the rotor.
• The rotor must rotate freely, without
jamming.
• Install the cap (2) to place and
tighten nut (1) to a 35 to 50 N•m
(3.5 to 5.0 kgf•m) torque.
NOTE:
After stopping the engine, the
noise of a turning rotor must be head
for 30-60 s. This indicates that the fil-
ter operates properly.