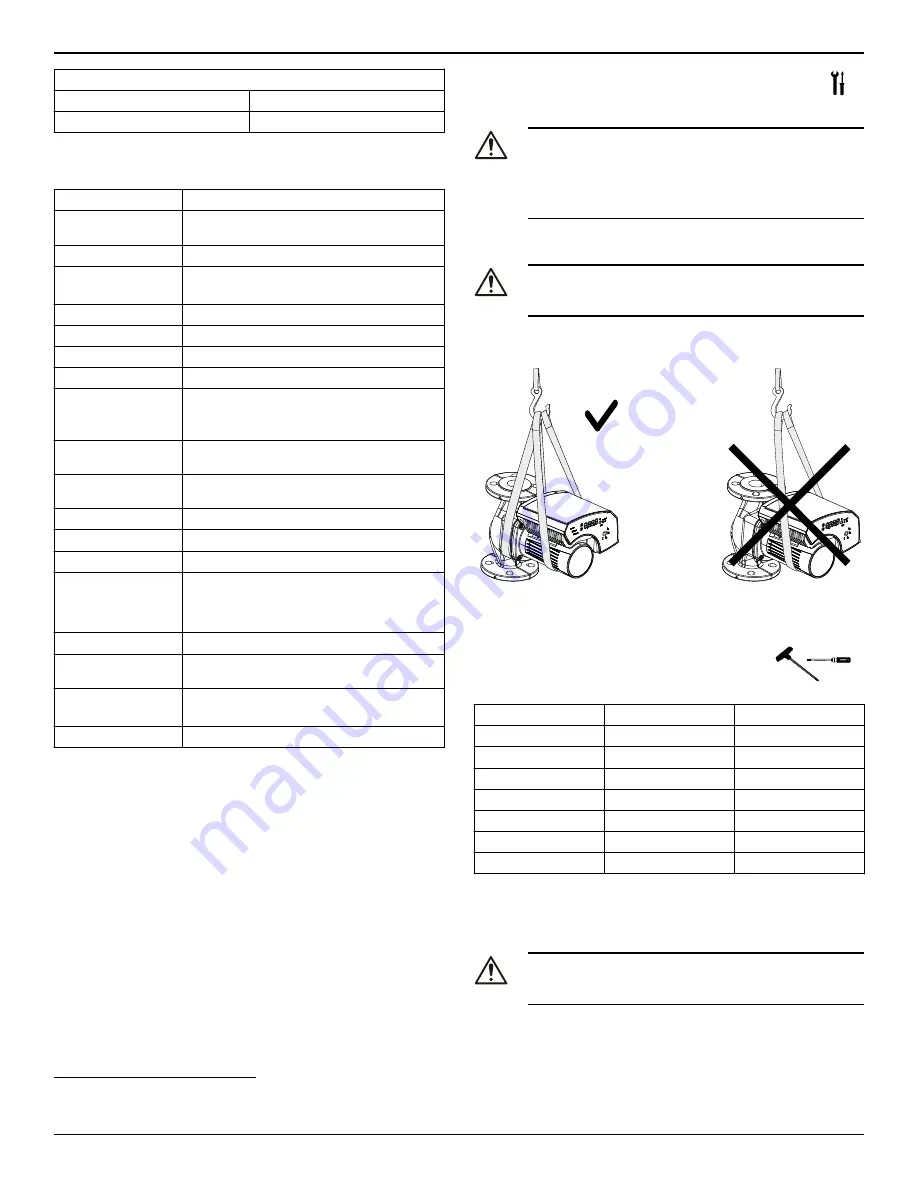
Example: ecocirc XL B 15–75
-15
Maximum pump head (FT)
-75
Maximum pump flow rate (GPM)
3.3 Technical data
Feature
Description
Motor model
Electronically commutated motor with perma-
nent magnet rotor
Series
ecocirc XL
Rated voltage
1 x 115 V ±10%
1 x 208–230 V ±10%
Frequency
50/60 Hz
Power consumption
100–1700 W
IP protection
IP 44
Insulation class
Class 155 (F)
Maximum working
pressure
The maximum pressure is indicated on pump
nameplate
175 PSI (12 bars)
Liquid temperature
range
14°F (-10°C) to 230°F (110°C)
Ambient temperature
range
32°F (0°C) to 104°F (40°C)
Ambient humidity
95% non-condensing
Pumping media
Water and water/glycol mixtures
1
up to 50%.
Sound pressure
≤ 43 dB (A)
EMC (electromagnetic
compatibility)
EN 55014-1:2006 + A1:2009 + A2:2011, EN
55014-2:1997 + A1:2001 + A2:2008, EN
61000-3-2:2006 + A1:2009 + A2:2009, EN
61000-3-3:2008, 61800-3:2004+A1:2012.
Leakage current
< 3.5 mA
I/O aux15 VDC
power supply
Imax < 40 mA
Fault signal relay
Vmax < 250 VAC
Imax < 2 A
CSA certification
NSF/ANSI-372 compliant (bronze body parts)
3.4 Scope of delivery
Inside the package you will find:
• Pump unit
• Insulating shells for pump body — for heating applications
• O-ring to be used as replacement between motor housing and
pump body
• Two (2) gaskets for flanged connection
• 20 mm x ½” NPT electrical fitting
• IOM and Quick Start guide
3.5 Accessories
• Companion flanges
• Fastener Packs consisting of 4 bolts and 4 nuts (for 2–bolt models)
• Fastener Packs consisting of 8 bolts and 8 nuts (for 4–bolt models)
• Pressure sensor (for details see section 5.2.10 of this manual)
• Temperature sensor (for details see section 5.2.10 of this manual)
• Wireless module
• RS–485 module
4 Installation
Precautions
WARNING:
• Observe accident prevention regulations in force.
• Use suitable equipment and protection.
• Always refer to the local and/or national regulations,
legislation, and codes in force regarding the selection of
the installation site, plumbing, and power connections.
4.1 Pump handling
WARNING:
Observe local codes and regulations setting the limits for
manual lifting or handling.
Always lift the pump by the motor housing or pump body. If the pump
weight exceeds the manual handling limits, use lifting equipment with
lifting straps.
4.2 Tools required for pump installation
• T-Handle with allen screw
• Control screw driver – with 2 mm blade size
Model number
Allen screw size (mm) T-handle length (in)
20–35
5
8
36–45
5
8
15–75
5
8
55–45
6
10
20–140
6
10
65–130
8
12
40–200
8
12
4.3 Facility requirements
4.3.1 Pump location
DANGER:
Do not use this unit in environments that may contain flam-
mable/explosive or chemically aggressive gases or powders.
Guidelines
Observe the following guidelines regarding the location of the prod-
uct:
1
The pump can be used with water/propylene glycol mixtures up to 50% with a maximum viscosity of 50cST at 14°F (-10°C). The pump has built-in overload and
thermal protection to protect the pump from overload due to increased fluid viscosity. Pump performance is based on 77°F (25°C). Therefore pumping of glycol
mixtures will affect max performance, depending on mixture concentration and temperature.
4 Installation
ecocirc XL Installation, Operation, and Maintenance manual
5