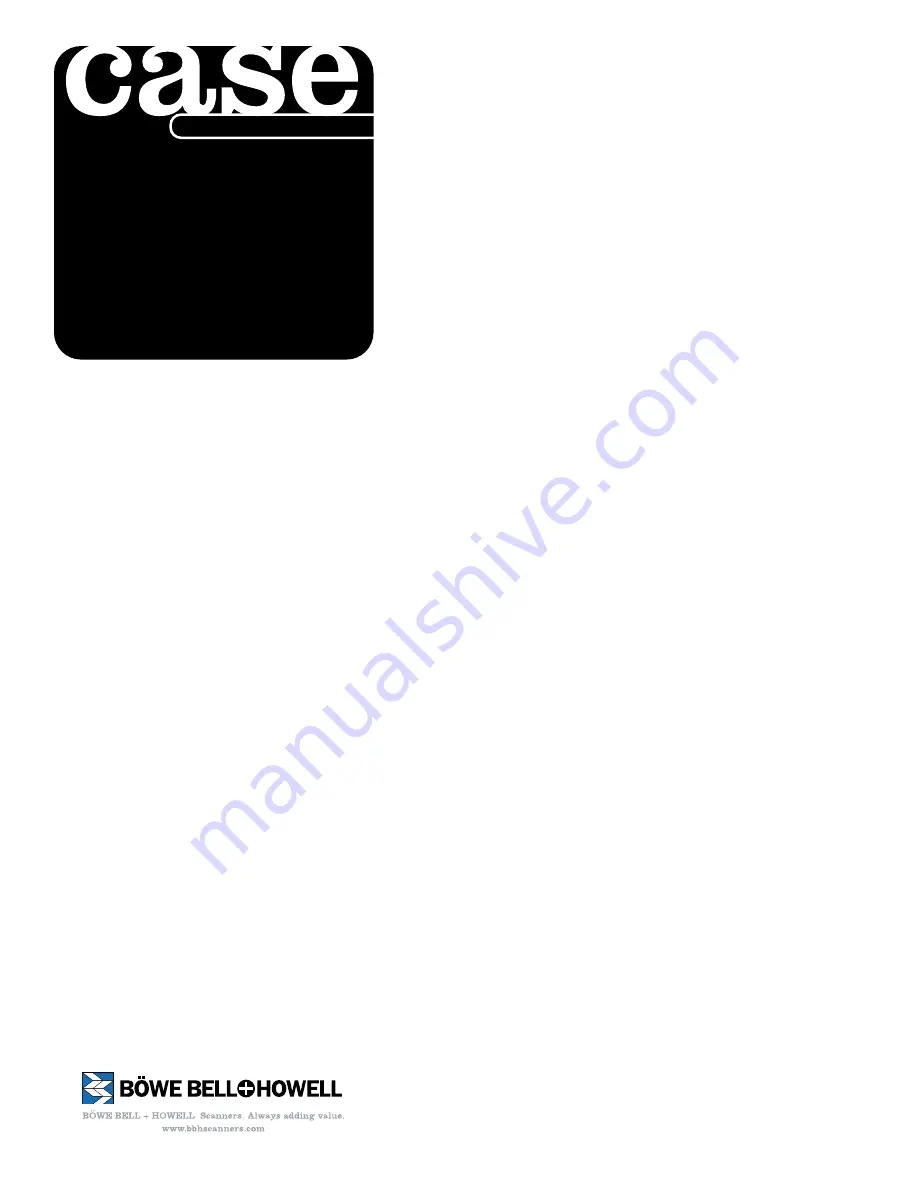
Essentially, Spectrum XF helped Papello ensure that any Maryhaven employees
with visual, auditory or physical impairments could fully operate and maintain the
scanners.
Work Processes Help Ensure Compliance, Security
Maryhaven’s lineup of BÖWE BELL + HOWELL production scanners today
includes eight Spectrum XF 8140 scanners, two Spectrum 8125 scanners and one
Trū¯ per 3200 scanner. The center operates an eight-hour shift, and uses DocuWare
and Kofax’s Ascent software for image capture and quality checks. It also ensures
compliance with regulations surrounding the management, creation and transfer
of digitized records. For example, because the bulk of Maryhaven’s work consists
of medical records and court documents, the center complies strictly with HIPAA
requirements.
Maryhaven employs adults with all types of disabilities, but it tests prospective
hires for two attributes: aptitude and patience. “As a professional agency, we ensure
that our employees are given the right kind of work to help us meet and exceed the
promise we make to our customers,” said Mahoney. Selected employees undergo
a two-week training regimen covering basic scanner operation, error resolution
and maintenance. They also receive instruction on HIPAA procedures and sign
confidentiality agreements before they work with any customer documents.
The scanning process at Maryhaven follows a series of carefully orchestrated
events. Customer documents arrive at the facility in banker boxes. About a dozen
workers prep the documents by removing them from envelopes, unfolding folded
material and removing staples. Scanner operators then feed the document batches
based on preprogrammed settings.
Equipped with the industry’s most advanced camera technology, Spectrum XF
scanners allow workers to capture up to 140 pages per minute. Image enhancement
technology built into the scanner hardware — VirtualReScan® (VRS) Professional
from Kofax — provides reliable capture and forms processing without sacrificing
scanning speed. VRS hardware in the scanner also adds several automated features,
such as blank-page deletion and auto-orientation.
“Automated features and user profiles with predetermined settings make it easy
for operators to make one selection and scan,” said Papello. Consistently sharp image
quality also improves the center’s optical character and barcode recognition rates.
One of the most valuable features that Spectrum XF brings to Maryhaven’s
imaging operation is ultrasonic multifeed detection, which helps ensure that every
document fed gets scanned. Sticky notes, taped photographs and labels often
appear on court and medical documents; fortunately, operators can preset the scanner
to ignore these items with the scanners’ exclusive Ignore-by-Size functionality. This
prevents the scanner from incorrectly identifying such documents as double-feeds and
allows operators to scan mixed batches of documents with remarkable accuracy.
Routine maintenance and cleaning the scanner is easy and does not require the
services of a specialized technician. Automatic indicators alert Maryhaven operators
when it’s time to clean the scanner or change the lamps.
Client Work Held to High Standard
All scanned images undergo a strict quality control process. Workers check
each paper file against a document log to verify high image quality. For clients who
need it, Maryhaven also follows a process for indexing the scanned documents.
Once the images pass quality control, an imaging specialist burns the files to CDs
or DVDs and mails them to the client. Some customers choose to receive their images
via a T1 line, which allows the secure transfer of scanned data from Maryhaven’s work
facility to a server or networked system on the client’s end. Employees then destroy the
paper records based on a schedule authorized by the client.
Maryhaven has come a long way from its microfilming days. While a few
microfilming cameras still chug along in one room, the work center today scans an
average of about 20 million documents annually.
“Scanning has provided our center with a sustainable means of revenue, and
given our staff valuable skills they can employ elsewhere,” said Mahoney. “We
expect to add more scanners next year to keep up with the growing demand for our
scanning services.”
Providing adults with disabilities hope and the ability to be productive members
of society was the founding principle of the Maryhaven Center of Hope — and
production scanning will help the center carry out that mission for years to come.
© 2008 Bowe Bell + Howell Scanners, LLC. All rights reserved. BÖWE BELL + HOWELL and the Böwe Bell
+ Howell logo are trademarks or registered trademarks of BBH, Inc. All other trademarks and service marks
are the property of their respective owners. Specifications are subject to change without notice.
S
T
U
D
Y
SD-222