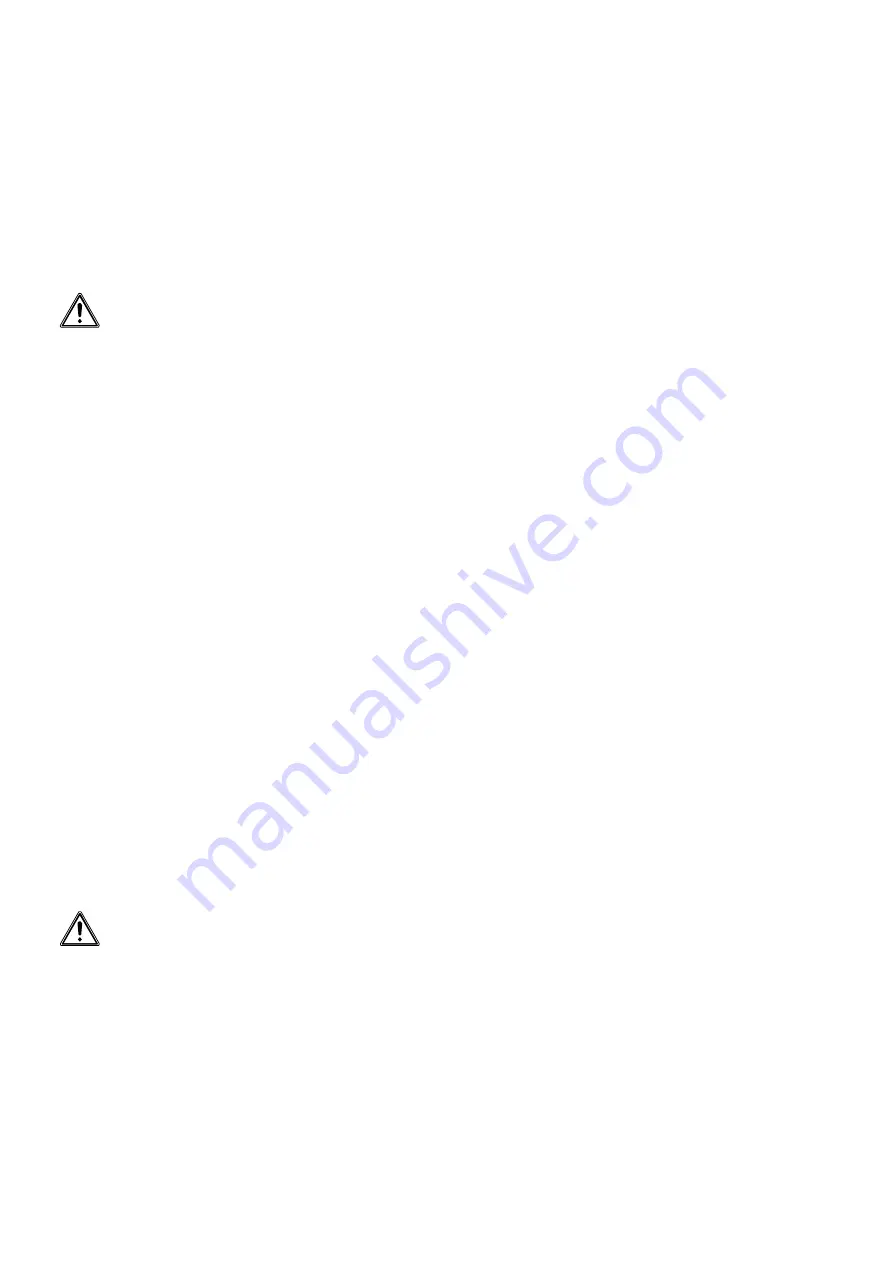
21
D22000431 v.0 - UPD 051213
5.2 - How to use log splitter
Position the log on the beam as shown in
fi
g.6, page 3. The supporting guides (2 in
fi
g.1, page 2) help to keep the log at the centre of the wedge.
If the log tends to wobble, it must be repositioned turning it so that is remains
fi
rmly on the beam.
From the permitted position only (10 in
fi
g.1, page 2), activate both the levers (4 in Abb.1) forwards: The log pusher will be activated and the log
will be split. Hold the levers of the two hands control in this position until the log is completely split.
Note: If you release one of the levers, the machine will stop in its current position.
If you release both the levers, the log pusher come back to the start position, fully open position.
Repeat the operation with the pieces obtained so as to split the log into several parts.
Never force the log splitter for more than a few seconds keeping the cylinder under pressure in the attempt to split ex-
cessively hard wood. The oil under pressure, in fact, is overheated and the machine could be damaged. It is thus better
to stop and rotate the log by 90° to see whether it can be split in a different position. In any case, if you are not able to
split the log, this means that its hardness exceeds the capacity of the machine and thus that log should be discarded
so as not to damage the log splitter.
WARNING
THE MANUFACTURER IS NOT LIABLE FOR INJURY TO PERSONS, ANIMALS OR OTHER THINGS CAUSED BY AN IMPROPER
USE OF THE MACHINE
5.3 - Manual handling of the log splitter
To move the machine for short distances use the appropriate lever (8 in
fi
g.1, pg.2) as shown in
fi
g.12, page 4.
When transporting (e.g. loaded on motor vehicles), ensure that all parts of the machine have cooled down completely, the bleeder screw is screwed
up, and the machine is positioned horizontally.
6 - ROUTINE MAINTENANCE
This chapter describes routine maintenance, i.e. operations carried out by the operator, on the TURBO 8 log splitter to keep this in perfect working
order and therefore reliable for continuous, long-term use.
All routine maintenance operations must be carried out with the machine off and in the case of log splitters with electric motor with the power cable
disconnected.
Any other maintenance operation not specifi cally envisaged in this manual must be carried out by authorised personnel only in that hazar-
dous situations may arise for which the operator is not prepared.
In the case in which extraordinary maintenance or part replacement operations are not carried out by authorised personnel, the guarantee
shall be immediately null and void and the manufacturer shall be relieved of any responsibility for injury to persons or animals or damage.
6.1 - How to change the hydraulic oil
The spent oil must be replaced with new oil of the type indicated on page 18 every 400 hours of operation. To change the oil, proceed as follows.
Make sure that the log pusher of the machine is fully retracted.
Unscrew the cap shown in Fig. 7/A on page 3 and remove it completely.
Position a container under the log splitter that can hold 8 litres of oil; then tilt the machine to empty the oil (Fig. 7/B).
Tilt the machine in the other direction (Fig. 7/C) and pour in 6 litres of oil of one of the types indicated on page 18.
Clean the dipstick and insert it (
fi
g.7/D) to check that the oil level is between the two notches on the stem.
Clean the cap and washer thoroughly and re-tighten completely but carefully so as not to break the threading of the cap.
WARNING:
NEVER MIX OIL WITH GENERAL WASTE! USED OIL MUST BE DISPOSED OF ACCORDING TO CURRENT REGULATIONS IN
THE COUNTRY WHERE THE MACHINE IS USED.
6.2 - Refi lling the hydraulic oil
Periodically check the oil level, which must be between the two notches on the oil cap dipstick (Fig. 7/D).
If the level is low, re
fi
ll using the recommended types of oil on page 18.
6.3 - Sharpening the wedge
After long periods of operation and when required, sharpen the wedge of the log splitter using a
fi
ne-toothed
fi
le and taking care to remove any burrs
or crushed parts of the metal.
ENGLISH
Summary of Contents for TURBO 8 B&S
Page 3: ...3 D22000431 v 0 UPD 051213 5 6 10 8 7 9...
Page 4: ...4 D22000431 v 0 UPD 051213 12 13 11a 11b...
Page 5: ...5 D22000431 v 0 UPD 051213 Assembling instructions...
Page 6: ...6 D22000431 v 0 UPD 051213 Assembling instructions KIT OPTION K91550100 K91550110...
Page 7: ...7 D22000431 v 0 UPD 051213 Assembling instructions KIT OPTION K91550100 K91550120...
Page 39: ...39 D22000431 v 0 UPD 051213...
Page 45: ...45 D22000431 v 0 UPD 051213 Tav 7 Key Code 161 B60380010 162 E25830185 163 E25354445...
Page 46: ...46 D22000431 v 0 UPD 051213...