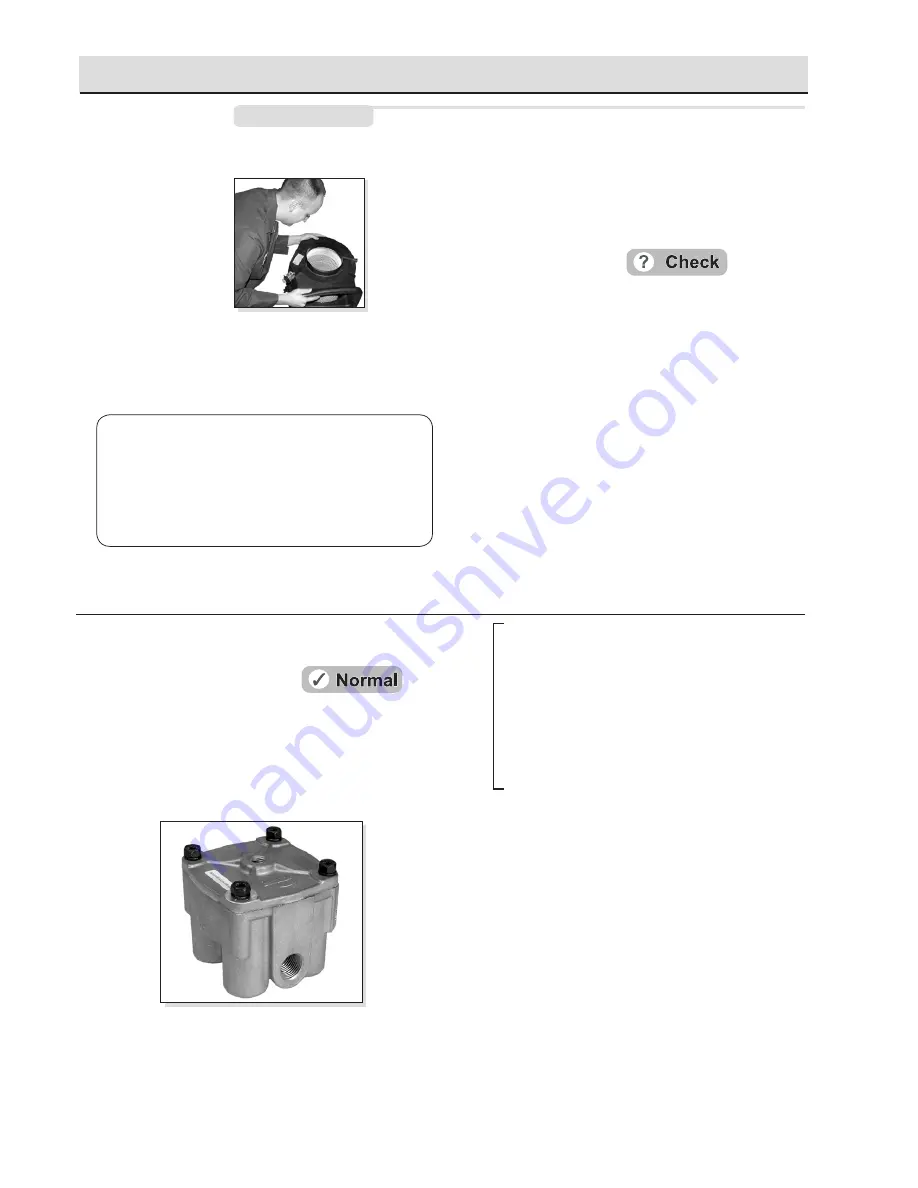
18
Symptom:
What it may indicate:
What you should do:
(i) Poorly filtered inlet air (poor air
quality to compressor).
(j) Governor malfunction or setting.
(k) Compressor malfunction.
4.0 Oil in Supply
or Service
Reservoir*
(air dryer installed)
(continued)
Check for leaking, damaged or defective
compressor air inlet components (e.g.
induction line, fittings, gaskets, filter bodies,
etc.). Repair inlet components as needed.
Note: Dirt ingestion will damage compressor
and is not covered under warranty.
Go to Test 4 on page 25.
If you found excessive oil present in the
service reservoir in step 4.0 (b) above and
you did not find any issues in steps 4.0 (c)
through 4.0 (j) above, the compressor may
be passing oil.
Replace compressor. If still under warranty,
follow normal warranty process. Note: After
replacing a compressor, residual oil may
take a considerable period of time to be
flushed from the air brake system.
Other (cont.)
Inspect the
engine air
cleaner.
** SAE J2024 outlines tests all air brake system pneumatic
components need to be able to pass, including minimum
levels of tolerance to contamination.
5.0 Oil present
at valves (e.g. at
exhaust, or seen
during servicing).
Air brake system valves are required
to tolerate a light coating of oil.
A small amount of oil does not affect SAE
J2024** compliant valves.
Check that regular maintenance is being
performed and that the amount of oil in the
air tanks (reservoirs) is within the accept-
able range shown on the Bendix
®
BASIC
test cup (see also column 5 of Table A on
page 13). Return the vehicle to service.
For oil-sensitive systems, see page 12.
Genuine
Bendix
valves are
all SAE
J2024
compliant.
*If a maintained Bendix
®
PuraGuard
®
system filter or Bendix
®
PuraGuard QC
™
oil coalescing
filter is installed, call 1-800-AIR-BRAKE (1-800-247-2725) and speak to a Tech Team member.
Crankcase Flooding
Consider installing a compressor bottom drain kit
(where available) in cases of chronic oil passing where
all other operating conditions have been investigated.
Bendix compressors are designed to have a 'dry'
sump and the presence of excess oil in the crankcase
can lead to oil carryover.