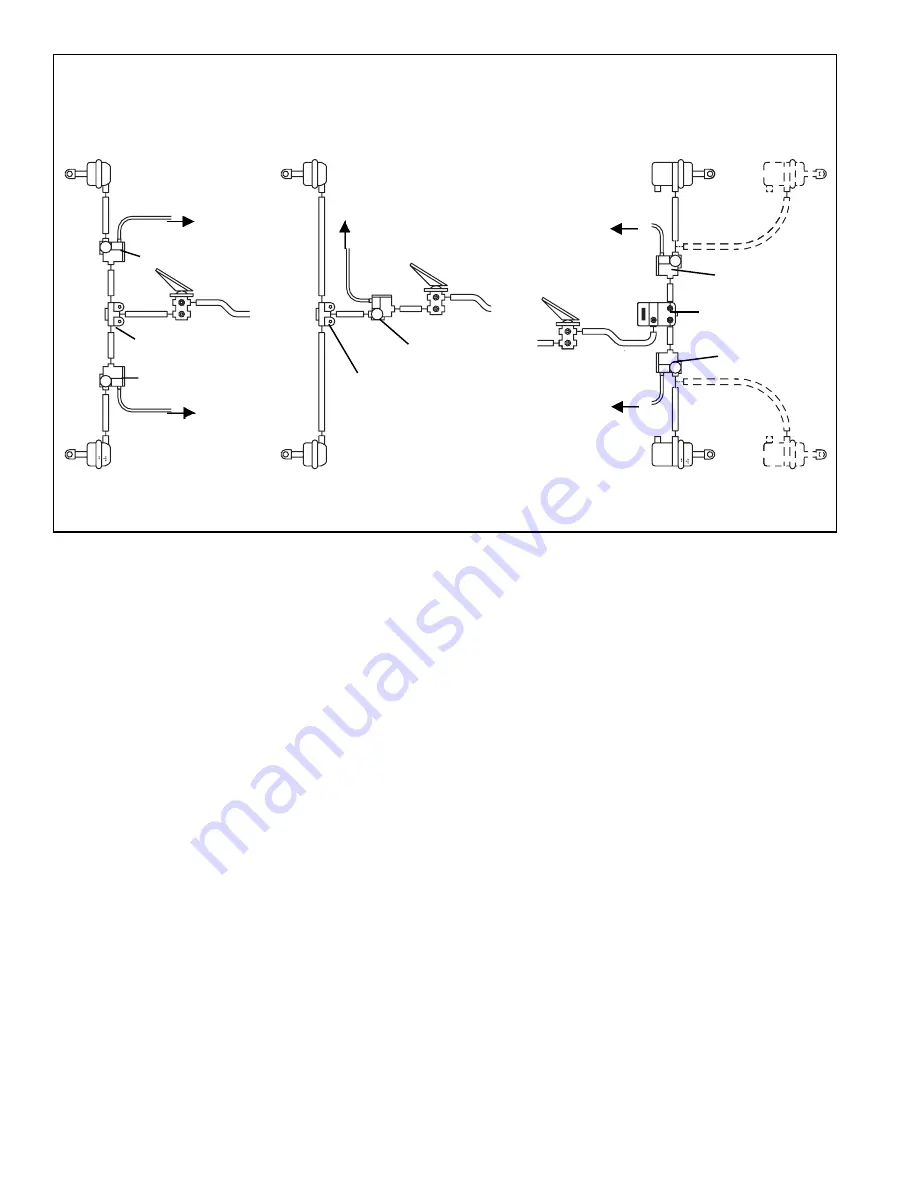
2
FIGURE 2 -
WHEEL AND AXLE CONTROL SYSTEMS
bw
NON-ANTILOCK HOLD (FIGURE 4)
When the desired air pressure is attained in the service
brake chambers, the brake system is in the holding position.
In the holding position both solenoids in the modulator remain
de-energized and the balance of the internal components
remain in the same position as they assumed during
application.
REAR AXLE SYSTEM
FRONT AXLE SYSTEMS
AXLE CONTROL
WHEEL CONTROL
WHEEL CONTROL
SERVICE BRAKE
CHAMBER
M-21
™
OR M-22
™
MODULATOR
M-21
™
OR M-22
™
MODULATOR
QUICK RELEASE VALVE
M-21
™
OR M-22
™
MODULATOR
SERVICE BRAKE
CHAMBER
SERVICE &
SPRING BRAKE
CHAMBER
QUICK RELEASE VALVE
TO
ANTILOCK
CONTROLLER
CONTROLLER/
RELAY ASSEMBLY
M-21
™
OR M-22
™
MODULATOR
M-21
™
OR M-22
™
MODULATOR
TO
ANTILOCK
CONTROLLER
TO
ANTILOCK
CONTROLLER
TO
ANTILOCK
CONTROLLER
TO ANTILOCK
CONTROLLER
They are as follows;
Identification
Air Line Connection
1
Supply
(incoming air from foot valve or relay)
2
Delivery
(air delivery to service actuators)
3
Exhaust
(air exhaust during antilock control)
OPERATION
NON-ANTILOCK APPLICATION (FIGURE 3)
During normal non-antilock braking, both solenoids are de-
energized (no electrical power). Brake application air enters
the supply port of the modulator and flows to, and through,
the open exhaust solenoid then to the exhaust diaphragm.
Air pressure, along with spring force, seats the exhaust
diaphragm on the exhaust passage thus preventing the
escape of service air. Simultaneously, application air flows
to the supply diaphragm and forces it away from its seat. Air
flows past the open supply and out the modulator delivery
port to the service brake chambers.