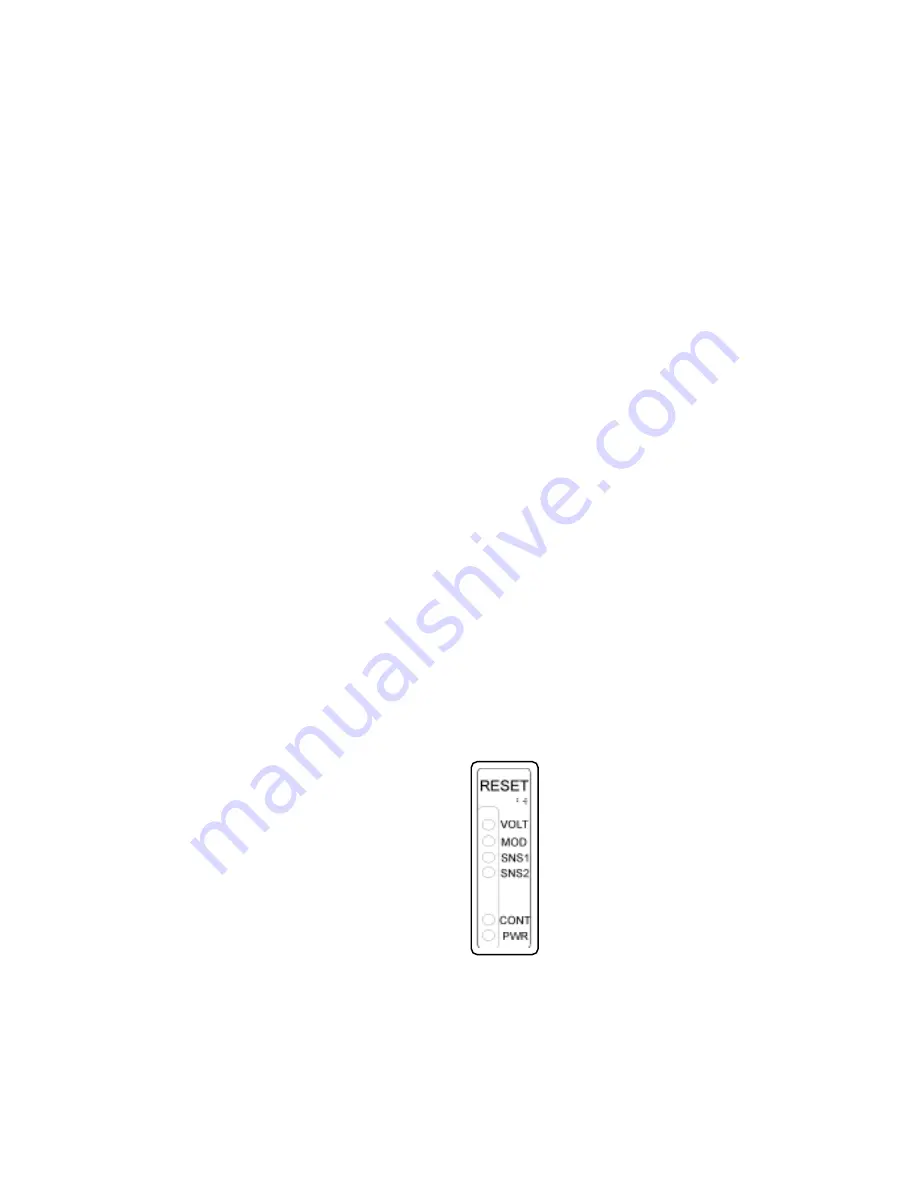
8
5. Inspect all air line fittings and plugs for corrosion. Clean
all old thread sealant from the pipe threads.
Any component exhibiting a condition described in inspection
steps 2 to 5 should be discarded and replaced before
proceeding.
ASSEMBLY—
REFER TO FIG. 9
1. Using a lubricant (Bendix Pc. No. 291126) lightly coat
all o-rings and the bores of the valve body.
2. Install spring seat (9) onto the inlet/exhaust valve (8) so
that it covers the rubber seat of the inlet/exhaust valve.
Place the inlet/exhaust valve, large diameter first, into
the M-12
™
modulator's bottom bore.
3. Install spring (10) over the barrel of the inlet/exhaust valve
(8) so that one end of the spring rests on the spring seat
(9).
4. Install the o-rings (11 8 12) into the respective grooves of
the O.D. and l.D. of the exhaust assembly (13). Place
the large diameter of the exhaust assembly against the
spring (10) and compress the spring until the exhaust
assembly enters the bore of the body and the o-ring (11)
seals against the wall of the bore.
5. Depress the exhaust assembly into the bore until it
exposes the groove for the snap ring (14). Install snap
ring (14) into its groove. Make sure it is fully seated.
6. Install o-ring (5) into its groove in the piston (6). Install
piston (6) into the M-12
™
modulator body. The piston
stem fits into the small hole in the center of the body.
7. Install o-ring (4) onto the protrusion on the bottom of the
M-12
™
modulator solenoid assembly. Install the solenoid
assembly (2) onto the valve body. The solenoid assembly
will fit on the M-12
™
modulator body in any of four
orientations, 90 degrees apart. However, if clearance is
a problem, make sure the control port is not directly
above the valve's supply port, which will be nipple
mounted to a reservoir. Secure the solenoid assembly
to the valve body with the four 1/2" bolts. Torque the
bolts to 120 150 in. Ibs.
8. Install gasket (7) onto the EC-12
™
controller. Install the
EC-12
™
controller (1) as shown in Figure 9 by plugging
the electrical connector from the solenoid assembly into
the socket in the bottom of the controller. Press in until
lock tab engages. Ensure engagement by pulling the
connector lightly. Place the controller onto the solenoid
assembly and secure with the four 1/2" bolts and lock
washers. Torque to 30 60 in. Ibs.
OPERATIONAL AND LEAKAGE TEST
1. Chock wheels. Fully charge air brake system and adjust
brakes.
2. Make several trailer brake applications and check for
prompt application and release at each wheel.
3. Check for inlet valve o-ring leakage. With the trailer
service brakes released, coat the exhaust port and the
area around the retaining ring with a soap solution. A 1"
bubble in 3 seconds is permitted.
4. Check for exhaust valve leakage. With the trailer service
brakes fully applied, coat the exhaust port with a soap
solution. A 1" bubble in 3 seconds is permitted. Coat
the outside of the modulator body to check for seal ring
leakage. No leakage is permitted.
5. If leakage is excessive around the supply and exhaust
solenoids, replace the M-12
™
modulator. If excessive
leakage is detected where the solenoid assembly and
M-12
™
modulator body meet, replace the M-12
™
modulator. If excessive leakage is detected at the exhaust
port, before replacing the M-12
™
modulator perform the
following test:
Place the vehicle in park by exhausting the air pressure
from the emergency side of the spring brake. Perform the
leakage check around the exhaust. If the air continues to
leak out the exhaust replace the M-12
™
modulator. If a leak
exists between the emergency and service sides of the spring
brake, the leakage at the exhaust will cease when air pressure
is exhausted from the emergency side of the spring brake.
The air pressure will pass from the emergency side to the
service side of the chamber, out the service inlet and out the
M-12
™
modulator exhaust.
ELECTRICAL TEST
If the status light remains on after the trailer brakes have
been actuated, inspect the EC-12
™
controller for illuminated
LEDs. Each LED represents a specific area.
VOLT LED (red)
High/Low Voltage
MOD LED
(red)
M-12
™
Modulator Failure
SNS1 LED (red)
Wheel Sensor Failure
SNS2 LED (red)
Wheel Sensor Failure
CONT LED (red)
EC-12
™
Controller Failure
PWR LED (green) EC-12
™
Controller Power
RED LEDs INDICATE FAILURE
When the EC-12
™
controller senses a failure, the red LED
corresponding to the failure mode will illuminate. A failure is
stored in memory until the problem is repaired and the
EC-12
™
controller is reset. NOTE: Only the voltage LED
resets itself after the condition no longer exists.