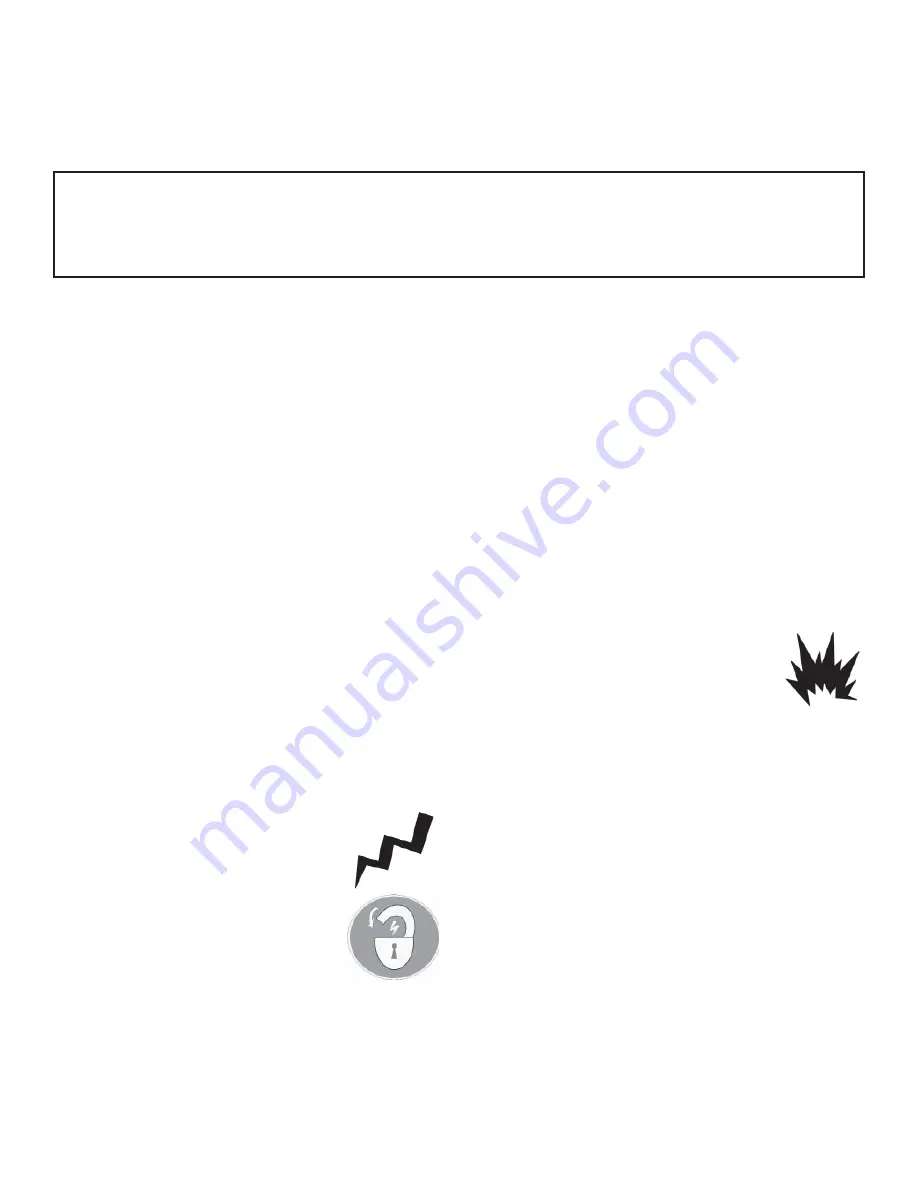
6
1. Carefully remove the crating and packing
materials. CAUTION! Be careful when cutting steel
banding material as items may become loose and fall
causing personal harm or injury.
2. Check the voltage, phase, and proper amperage
requirements for the motor shown on the motor plate.
Electrical work should be performed only by a certifi ed
electrician.
IMPORTANT SAFETY INSTRUCTIONS
Read these safety instructions entirely. Do not attempt to install this lift if you have never been trained
on basic automotive lift installation procedures. Never attempt to lift components without proper lifting tools such as
forklift or cranes. Stay clear of any moving parts that may fall and cause injury. When using your garage equipment,
basic safety precautions should always be followed, including the following:
INTRODUCTION
1. Read and understand all instructions and all safety warn-
ings before operating lift.
2. Care must be taken as burns can occur from touching
hot parts.
3. Do not operate equipment with a damaged cord or if the
equipment has been dropped or damaged until it has been
examined by a qualifi ed service person.
4. Do not let a cord hang over the edge of the table, bench,
or counter or come in contact with hot manifolds or moving
fan blades.
5. If an extension cord is necessary, a cord with a current
rating equal to or more than that of the equipment should be
used. Cords rated for less current than the equipment may
overheat. Care should be taken to arrange the cord so that it
will not be tripped over or pulled.
6. Always unplug equipment from electrical outlet when not
in use. Never use the cord to pull the plug from the outlet.
Grasp plug and pull to disconnect.
7. Let equipment cool completely before putting away. Loop
cord loosely around equipment when storing.
8. To reduce the risk of fi re, do not operate equipment in the
vicinity of open containers of fl ammable liquids (gasoline).
9. Adequate ventilation should be provided when working
on operating internal combustion engines.
10. Keep hair, loose clothing, fi ngers, and all parts of body
away from moving parts. Keep feet clear of lift when lowering.
Avoid pinch points.
11. DANGER! To reduce the risk of elec-
tric shock, do not use on wet surfaces or
expose to rain. The power unit used on
this lift contains high voltage. Disconnect
power at the receptacle or at the circuit
breaker switch before performing any elec-
trical repairs. Secure plug so that it cannot
be accidentally plugged in during service. or
mark circuit breaker switch so that it cannot
be accidentally switched on during service.
12. Use only as described in this manual.
Use only manufacturer’s recommended attachments.
13. ALWAYS WEAR SAFETY GLASSES. Everyday eye-
glasses only have impact resistant lenses, they are not safety
glasses.
14. Consider work environment. Keep work area clean.
Cluttered work areas invite injuries. Keep areas well lit.
15. Guard against electric shock. This lift must be grounded
while in use to protect operator from electric schock. Never
connect the green power cord wire to a live terminal. This is
for ground only.
16. Only trained operators should operate this lift. All non-
trained personnel should be kept away from the work area.
Never let non-trained personnel come in contact with, or
operate lift.
17. DO NOT override self-closing lift controls.
18. Clear area if vehicle is in danger of falling.
19. ALWAYS make sure the safeties are engaged before
attempting to work on or near a vehcile.
21. WARNING! RISK OF EXPLOSION. This
equipment has internal arcing or sparking
parts which should not be exposed to fl am-
mable vapors. This machine should not be
located in a recessed area or below fl oor
level.
22. MAINTAIN WITH CARE. Keep lift clean for better and
safer performance. Follow manual for proper lubrication and
maintenance instructions. Keep control handles and/or but-
tons dry, clean and free from grease and oil.
23. Check for damaged parts. Check for alignment of mov-
ing parts, breakage of parts or any condition that may affect
operation of lift. Do not use lift if any component is broken or
damaged.
24. NEVER remove safety related components from the lift.
Do not use lift if safety related components are missing or
damaged.
23. STAY ALERT. Use common sense and watch what you
are doing. Remember, SAFETY FIRST.
SAVE THESE INSTRUCTIONS