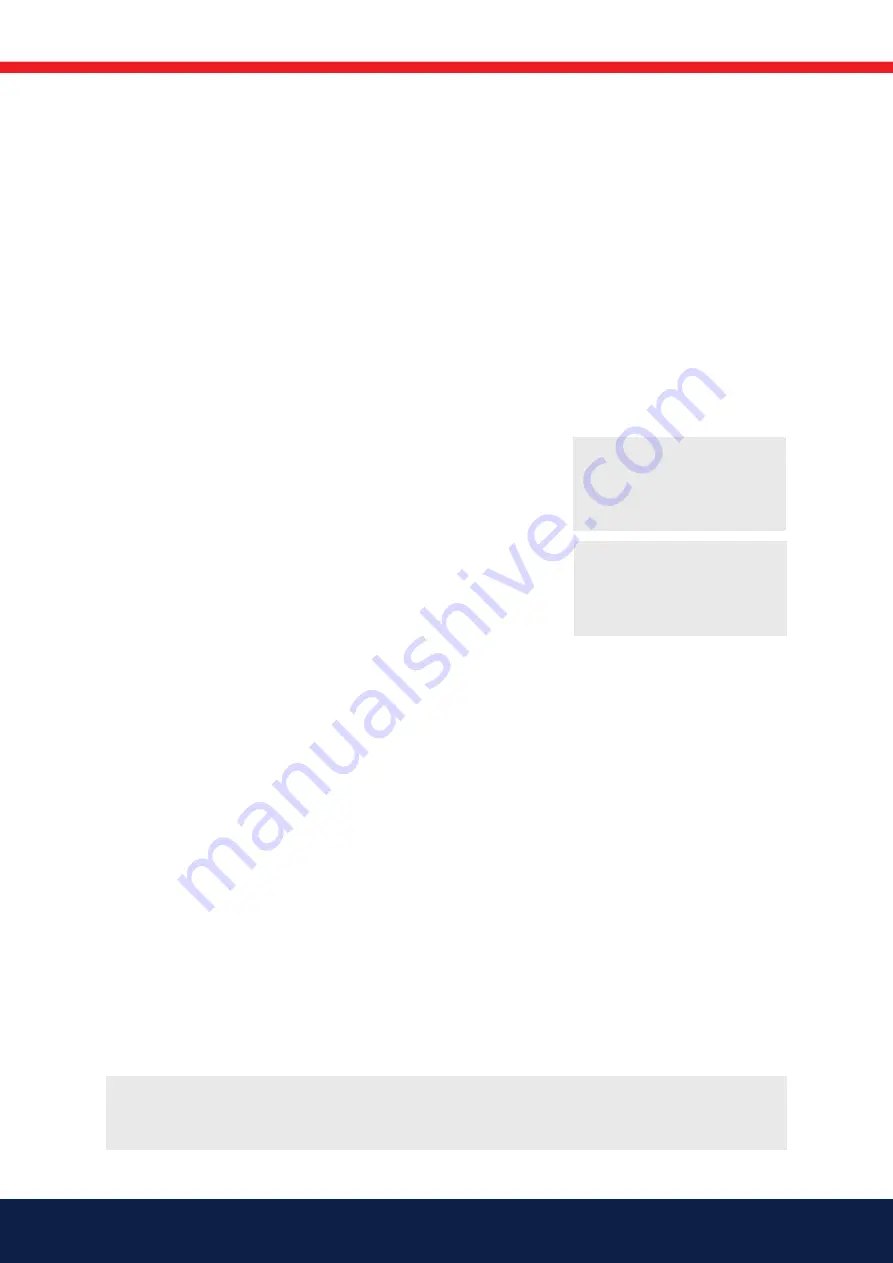
13
Bentone
!
If any electrical connection is used other than that recommended by Enertech, there may be a risk of
damage to property and personal injury.
3.2 Delivery inspection
Make sure everything is delivered and the goods have not been damaged
during transit. If something is wrong with a delivery, report it to the supplier.
Transport damage must be reported to the shipping company.
3.3 Preparing for installation
Check that the burner’s dimensions and capacity range are suitable for the
relevant boiler. The power data on the rating plate refers to the burner’s
minimum and maximum power.
3.4 Oil distribution
In order to achieve good reliability, it is important that the oil distribution
system is designed correctly.
Take the following into account:
-
Selection of pipe diameter, pipe length and height difference; see
Pump instruction.
-
Pipelines are to be laid with the fewest possible number of glands.
-
The pipes are to be laid so that the oil supply hoses are not subjected
to tensile stresses or become excessively bent when the burner is
swung out or removed for servicing.
-
The oil filter should be installed so that the filter cartridge can easily be
replaced or cleaned.
-
Parts in contact with oil must be selected in materials that are capable
of withstanding the medium’s physical properties.
-
When installing oil hoses, check that the inlet and return hoses are
fitted to the appropriate connection on the oil pump. The hoses must
be located so that they do not bend or become subject to tensile
load.
-
Bleed the oil system. The oil pump/oil preheater may be damaged if
run dry. The vacuum in the suction line should not fall below 0.3 bar
during start-up.
!
Be sure to fill the
burner oil system
before starting it for
the first time.
3.5 Electrical connection
• Before work on the electrical connection, the current must be
disconnected so that the installation is isolated.
• Electrical connection must be done in accordance with the applicable
regulations.
• Burners must be connected to an all-pole switch.
• Connection must conform to the wiring diagram.
• Use appropriately sized fuses.
!
The oil filter must
be installed before
the burner’s oil
pump
Summary of Contents for BENTOFLEX ST 146 B30A
Page 32: ...171 905 28...
Page 35: ......
Page 36: ...Enertech AB P O Box 309 SE 341 26 Ljungby www bentone se www bentone com...