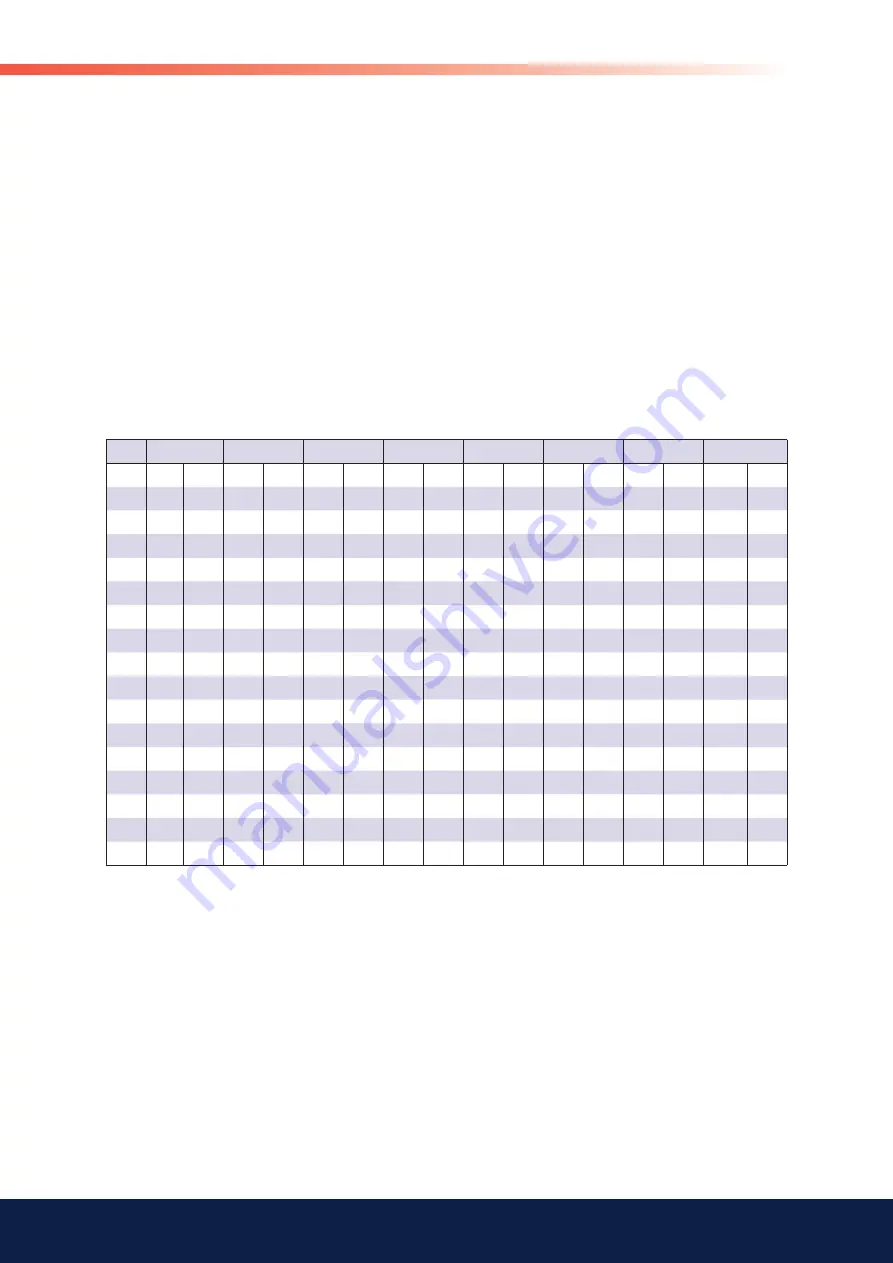
9
Bentone BF1
General
2.2 Recommended nozzles and pressures
Because of the different types of boiler in existence, with varying furnace
geometries and furnace loads, it is not possible to commit to any given spray
angle or spay pattern. Note that spray angles and spray patterns change
with pump pressures.
Nozzle
60° Solid/Hollow cone
80° Solid/Hollow conel
Pump pressure
10 bar (8–14 bar) Fuel oil 1, RME
Kerosene
2.3 Nozzle table, 8-15 bar
Pump pressure, bar
Gph
8
9
10
11
12
13
14
15
kg/h
kW
kg/h
kW
kg/h
kW
kg/h
kW
kg/h
kW
kg/h
kW
kg/h
kW
kg/h
kW
0,40 1,33
16
1,41
17
1,49
18
1,56
18
1,63
19
1,70
20
1,76
21
1,82
21
0,50 1,66
20
1,76
21
1,86
22
1,95
23
2,04
24
2,12
25
2,20
26
2,28
27
0,60 2,00
24
2,12
25
2,23
26
2,34
28
2,45
29
2,55
30
2,64
31
2,73
32
0,65 2,16
26
2,29
27
2,42
29
2,54
30
2,65
31
2,75
33
2,86
34
2,96
35
0,75 2,49
29
2,65
31
2,79
33
2,93
35
3,08
36
3,18
38
3,30
39
3,42
40
0,85 2,83
33
3,00
36
3,16
37
3,32
39
3,47
41
3,61
43
3,74
44
3,87
46
1,00 3,33
39
3,53
42
3,72
44
3,90
46
4,08
48
4,24
50
4,40
52
4,56
54
1,10 3,66
43
3,88
46
4,09
48
4,29
51
4,48
53
4,67
55
4,84
57
5,01
59
1,20 3,99
47
4,24
50
4,47
53
4,68
55
4,89
58
5,09
60
5,29
63
5,47
65
1,25 4,16
49
4,40
52
4,65
55
4,88
58
5,10
60
5,30
63
5,51
65
5,70
68
1,35 4,49
53
4,76
56
5,02
59
5,27
62
5,50
65
5,73
68
5,95
70
6,15
73
1,50 4,98
59
5,29
63
5,58
66
5,85
69
6,11
72
6,36
75
6,60
78
6,83
81
1,65 5,49
65
5,82
69
6,14
73
6,44
76
6,73
80
7,00
83
7,27
86
7,52
89
1,75 5,82
69
6,18
73
6,51
77
6,83
81
7,14
85
7,42
88
7,71
91
7,97
94
2,00 6,65
79
7,06
84
7,45
88
7,81
93
8,18
97
8,49
101
8,81
104
9,12
108
2,25 7,49
89
7,94
94
8,38
99
8,78
104
9,18
109
9,55
113
9,91
117
10,26
122
The table applies to oils with a viscosity of 4.4 mm
2
/s (cSt) at a density of 830 kg/m
3
.
2.3.1 Burner with preheater
Allow for a reduction in oil quantity of 5–20% with preheating owing to:
• Temperature increases at the nozzle.
• Nozzle design.
• Capacity (the higher the capacity the lower the difference).
Summary of Contents for BF1 RME
Page 2: ......
Page 11: ...11 Bentone BF1 General 2 11 12 1 10 5 15 24 22 21 23 13 3 17 14 19 20...
Page 36: ...10 DECLARATION OF CONFORMITY...
Page 38: ......
Page 39: ......
Page 40: ...Enertech AB P O Box 309 SE 341 26 Ljungby www bentone se www bentone com...