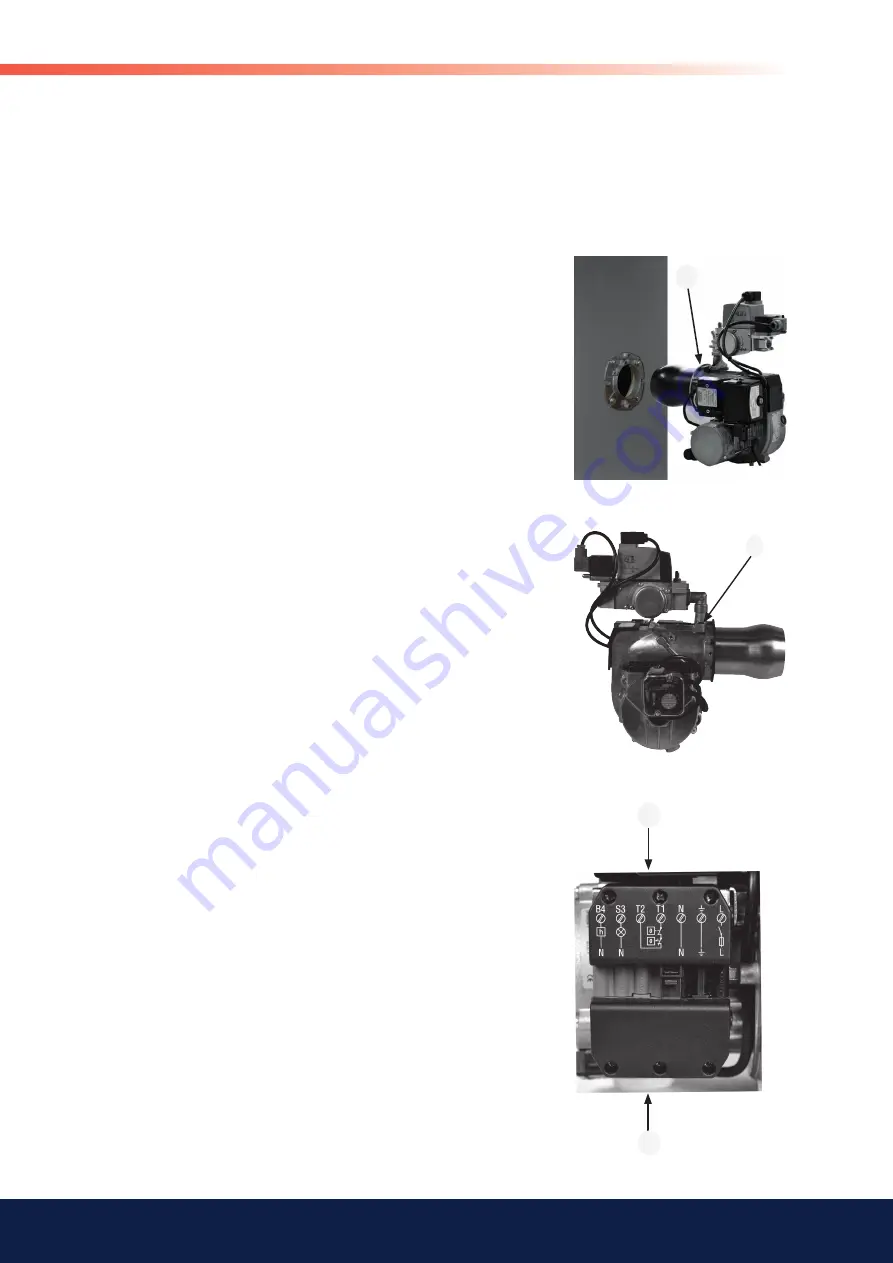
17
Bentone BFG1
E
F
X1
X2
3.7 Burner installation
3.7.1 Hole pattern
Check that the hole pattern on the boiler matches that of the flange, (see
Technical data).
3.7.2 Burner installation
1.
Install the flange with gasket on the boiler.
2.
Insulate between the blast tube and the boiler door to minimize heat
radiation.
3.
Check the ignition electrode and ionisation electrode.
(Refer to Technical data).
4.
Install the burner on the boiler and lock into the flange (E).
5.
Install the gas line on the burner. Check that the O-ring has not been
damaged during installation, fasten with the screws (F).
6.
Where support for the multiblock is included, this should be installed.
3.7.3 Gas connections
1.
Check the gas pipe dimensions. (According to local regulations).
2.
Connect the gas pipe to the gas flange of the multiblock.
3.
A manual gas valve should be installed in the vicinity of the burner.
4.
No mechanical stresses/forces should exist in the gas connection.
5.
Check the sealing of the gas connections, including the multiblock and
flanges.
NOTE!
If the gas connection is via a hose, the support for the multiblock that is
supplied with the burner should be mounted (F). Install the support so that
the underneath of the multiblock rests on it.
3.7.4 Electric connection
If the boiler does not have a pre-wired connector, connect in the included
connector, X2 according to the wiring diagram.
1.
Turn off the main switch.
2.
Connect the Eurostecker X2 acc. to Alt. 1 - 3, (see Electric equipment).
3.
Install the Eurostecker X2 on the burner.
4.
Turn on the main switch.
Summary of Contents for BFG 1 H1
Page 13: ...13 Bentone BFG1 4 3 5 1 6 2 10 16 9 15 14 13 7 8 22 11 12 2 7 Description ...
Page 47: ...47 Bentone BFG1 Alt 1 Acc to DIN 4791 Alt 2 Alt 3 8 2 Wiring diagram ...
Page 54: ......
Page 57: ......
Page 58: ......
Page 59: ......
Page 60: ...Enertech AB P O Box 309 SE 341 26 Ljungby www bentone se www bentone com ...