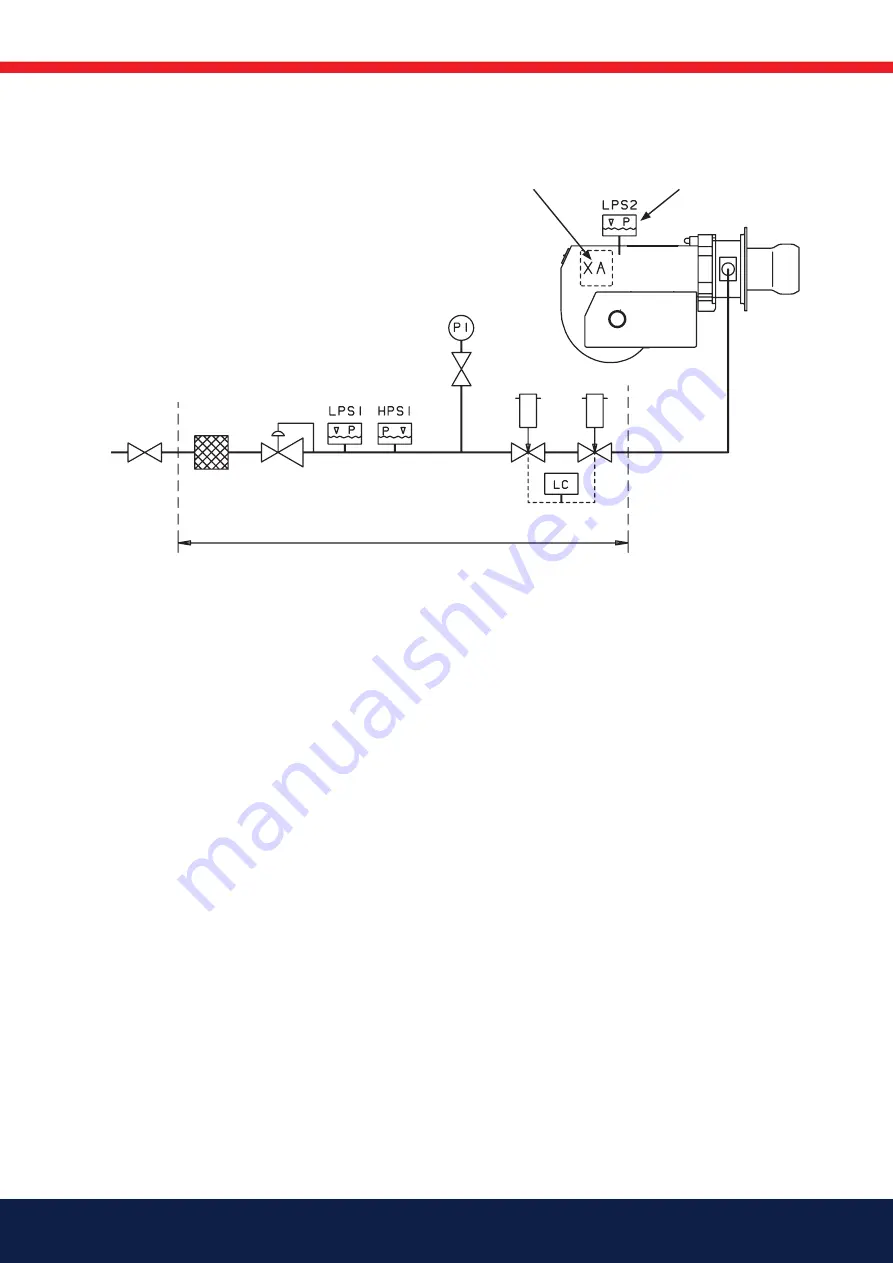
25
Bentone
172 515 04 2018-01-02
4.10
Skeleton diagrams
,
1-stage burner
1 Ball valve
2 Filter
3 Governor
4 Pressure gauge with shut-off cock
5a Gas pressure switch, mini
5b Gas pressure switch, maxi
6a Main valve
6b Safety valve
7
1)
Valve proving system
9 Air pressure switch
10 Gas burner control
Pos. 5b, 7: Components not required according to EN 676.
1)
Required over 1200 kW according to EN 676.
3
6b
5b
10
6a
9
7
1
2
5a
4
Summary of Contents for STG 146i/2
Page 34: ...34 Bentone 6 2 Wiring diagram...
Page 123: ......
Page 124: ...Enertech AB P O Box 309 SE 341 26 Ljungby www bentone com...