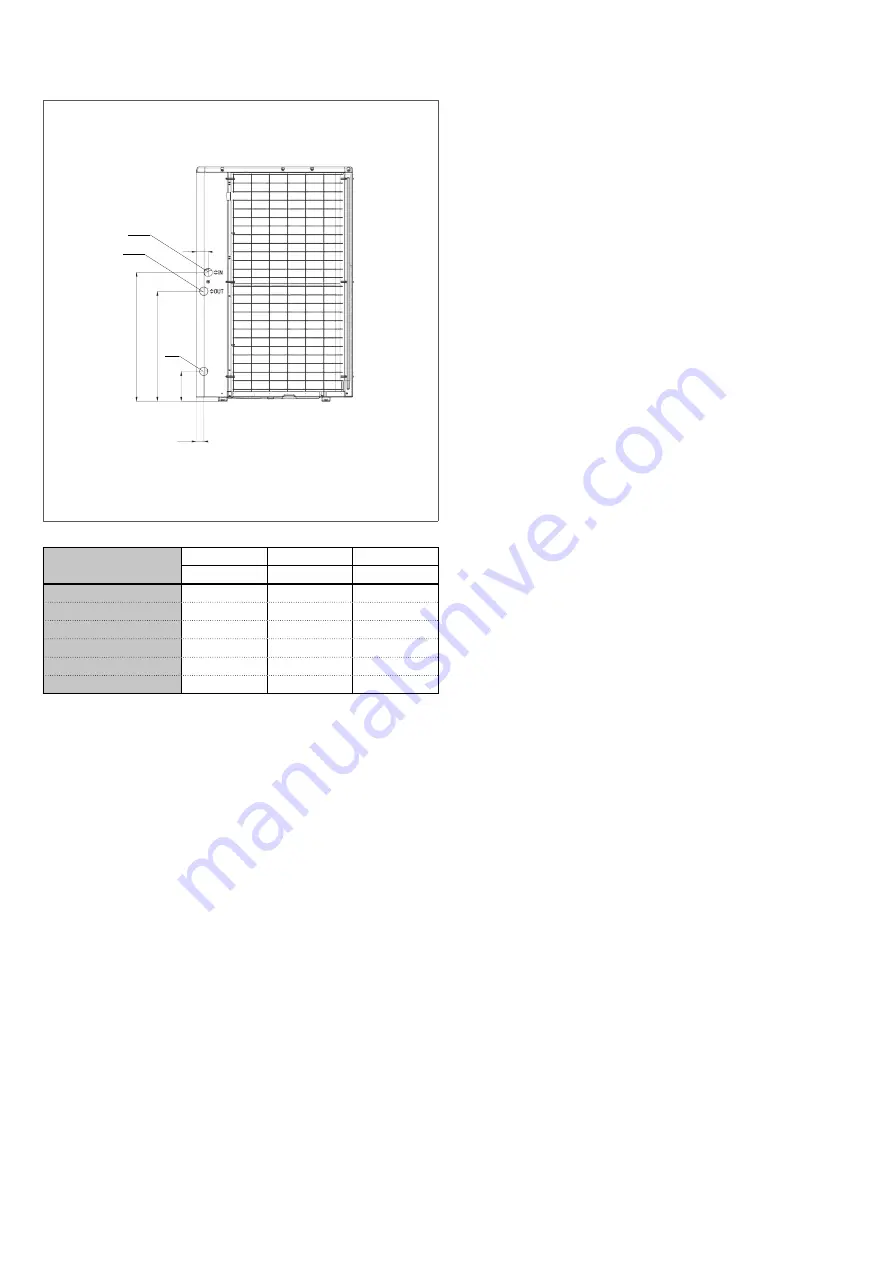
INSTALLATION
19
MODEL 11 - 15
A
System return
B
System delivery
C
Discharging
73
43
645
744
169
A
B
C
Model
System return
System delivery
Discharging
Inches
Inches
Inches
5
1
1
3/4
7
1
1
3/4
11
1
1
3/4
15
1
1
3/4
11T
1
1
3/4
15T
1
1
3/4
9
The choice and installation of the system components is dele-
gated to the installer, who will have to operate according to the
rules of good technique and current legislation.
9
The discharge of the installed safety valves must be connected
to an adequate collection and evacuation system. The man-
ufacturer of the appliance is not responsible for any flooding
caused by the intervention of the safety valves.
9
Is suggested to put a by-pass connection for the heat pump in
order to allows the cleaning of the system pipes without dis-
connecting the unit.
9
The connection tubes must have the appropriate diameter and
must be supported, so as not to rest their weight on the unit.
9
The systems with anti freeze additives or specific local laws,
require the installation of hydraulic backflow preventers.
9
Check the pressure drops of the appliance, the system, and
any other accessories mounted in line.
9
Do not use the heat pump for treating industrial water, swim-
ming pool water or domestic water. If water supplies of this
kind are used, an intermediate heat exchanger must be used.
Make sure to maintain the min. water content, possibly adding
a storage.
9
If the unit works in a system with a boiler >(parallel installation)
when the boiler is working, make sure that the water tempera-
ture inside the heat pump does not exceed 60 °C.
Mandatory items:
—
install a removable mesh water filter at the inlet to the appli
-
ance in an area accessible to maintenance, with character-
istics of at least 10 meshes / inch², to protect the appliance
from impurities in the water
— after the installation of the system and after each repair, it is
essential to clean the entire system thoroughly, paying par-
ticular attention to the condition of the filter
— install a suitably sized expansion vessel
— install air vent valves in the highest points of the pipes
—
install flexible elastic joints for connecting the pipes
— ensure that the quantity of water in the primary circuit is
greater than the minimum volume indicated in the chapter
"Plant water content"
p. 17, ensure that the quantity of wa-
ter in the primary circuit is greater than the minimum volume
indicated in the chapter
—
Foresee the pipes insulation, after the leackage verification,
in order to minimize the heat loss and the condensate effect.
— Use anti freeze additives in order to prevent the wter freezing
if the water circuit and pipes are exposed to ambient temper-
ature below 0°C.
0
It is forbidden to run the unit without a clean water filter in
-
stalled.