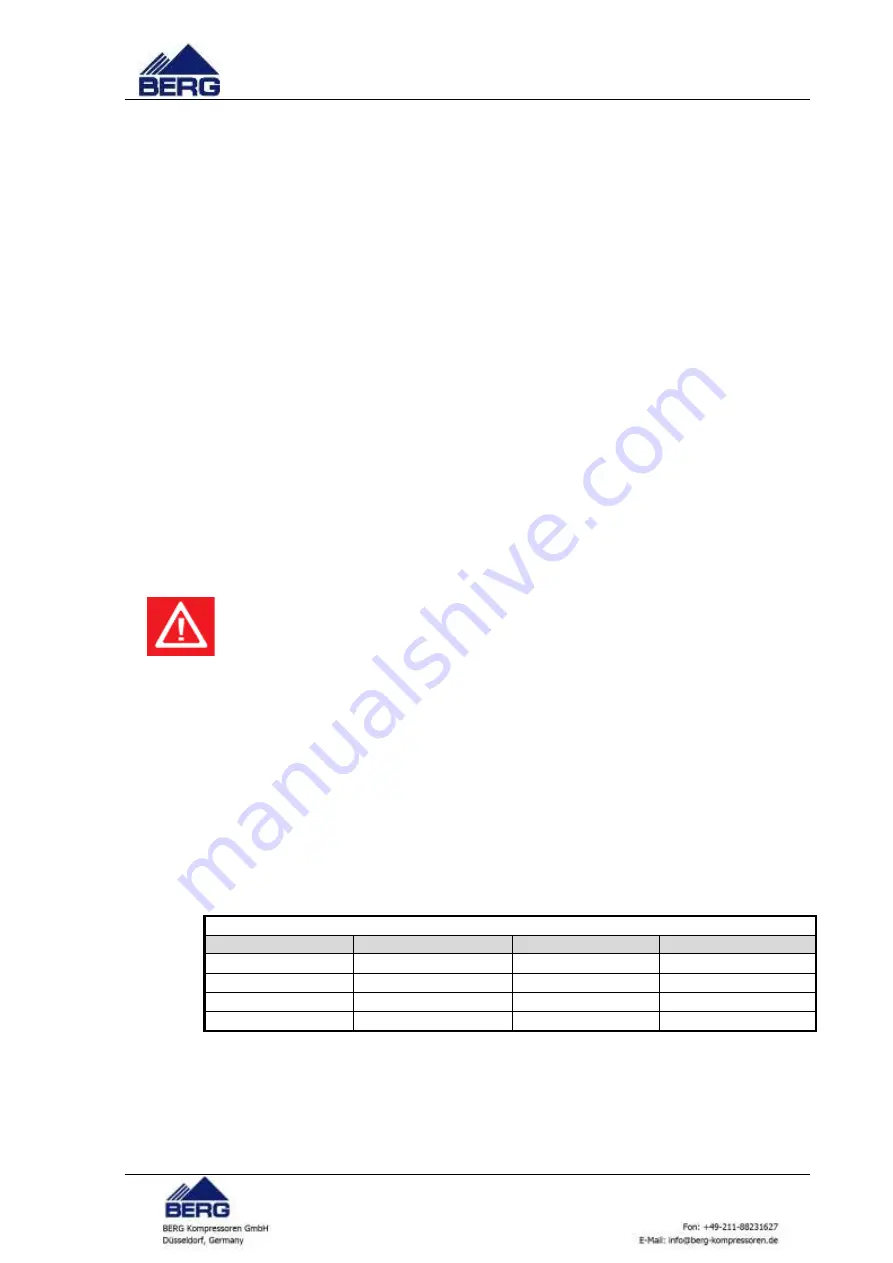
Maintenance procedure:
-
Stop the compressor, close the pressure conduit valve.
-
Lower the overpressure in the screw assembly body till reaches the atmospheric pressure (to
lower the overpressure inside the screw assembly body wait about 5 minutes after switching off
the compressor,
-
Safeguard the compressor from restarting by an unauthorized person, e.g. by cutting power
supply off.
-
Dismantle the radiator.
-
Clean and remove impurities.
-
Reassemble all disassembled components.
-
Fill (top up) the compressor with oil.
-
Carry out a operating test for approx. 3 to 5 minutes.
-
Stop the compressor, check the oil level and top up if necessary.
7.3.8.
. Electric motor
When the compressor is running, check the motor operation by paying attention to the following:
-
Operating noise,
-
Excessive vibration,
-
Excessive current consumption
–
protection activation in the electrical cabinet,
-
The condition of the fixing screws,
-
A degree of fouling.
The motor (compressor) should be stopped immediately in case of:
-
Overheating,
-
Smoke or burningsmell,
-
Excessive vibration,
-
Bearing noise.
The machine can be restarted after removing the cause of any failures
.
Periodic motor inspections:
The motor inspection should be performed at least once per 2 years.
The inspection should be performed by the in-house personnel or properly qualified personnel
from specialized companies.
Any repairs or special inspections should be performed by the specialised workshop or the
manufacturer service.
Replacement or lubrication of the motor bearings must be performed in accordance with the
manufacturer’s recommendations. The permissible hours of the bearing operation to the
replacement or lubrication are presented in the table below. When any symptoms indicating the
bearing damage occur (unusual noise or increased temperatures), contact the service
immediately.
7.3.9
Safety valve
The safety valves fulfil an important function in pressure equipment and systems. They require
particularly careful and professional service. Any operational shortcomings may damage the
Hours of operation until the performance of service operations
Motor power
Bearing type
Hours of operation
Operations
3-22 kW Maintenance-free
40000 h Replacement
30-55 kW Maintenance-free
20000 h Replacement
75-90 kW Requiring maintenance
4000 h Lubrication
110-200 kW Requiring maintenance
3000 h Lubrication