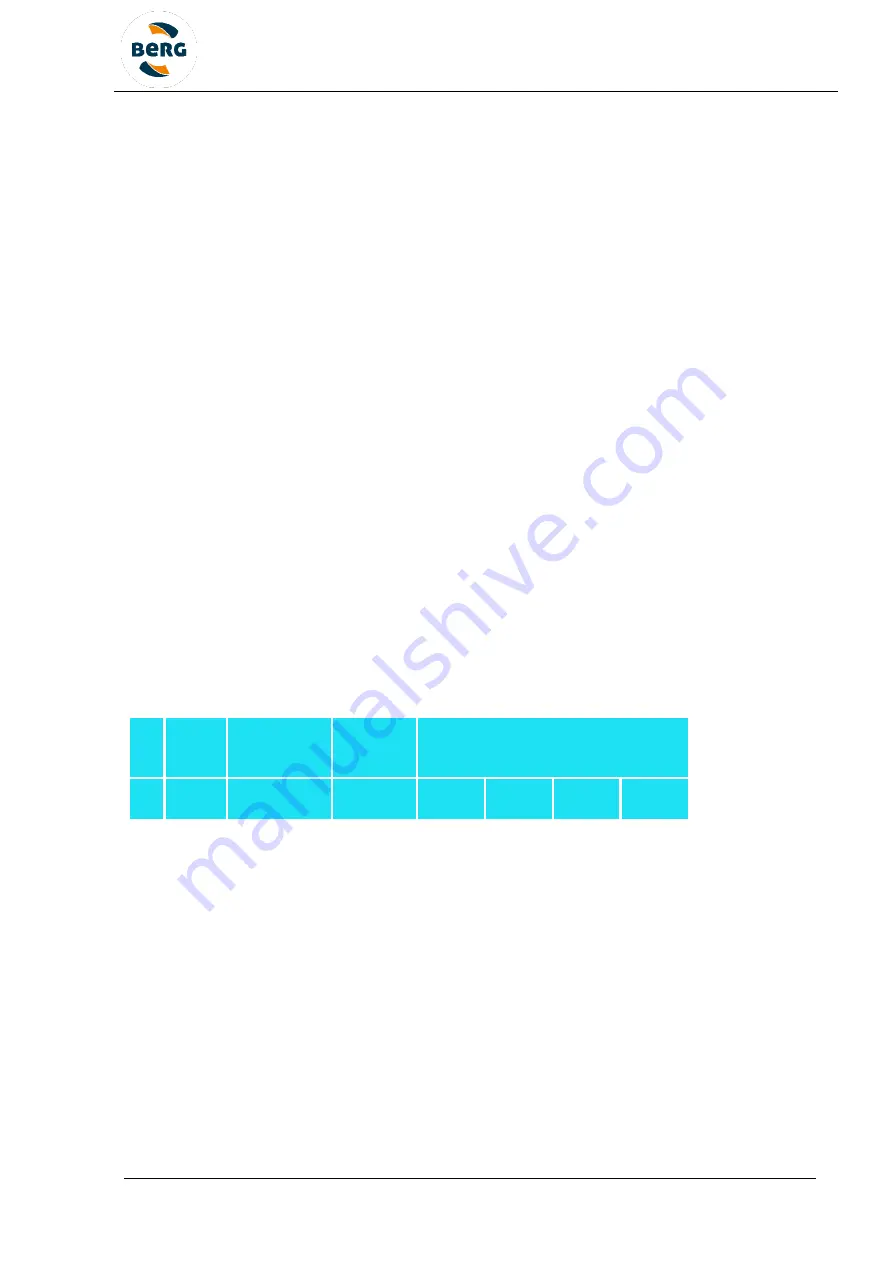
Translated user manual V3_EN
METO-SWT
7030.XX.XXXX
17 / 52
7.3
Minimum requirements for the pipe rail system
The rails (normally heating pipes) must have an external diameter of either 51 mm or 45
mm and a wall thickness of at least 2 mm. The minimum material specifications for the
pipes is as follows: Steel 37 (S235JR). The distance between the pipe rail system
supports may not exceed 1.25 metres. When combining pipes with a diameter of 45 mm
to a track width of 42cm, the distance between the rail supports should not exceed 1
metre. The pipe rail supports used should be in accordance with, or equivalent to the
following specifications: 1.5 mm thick steel base plate with reinforcing profile - base plate
width of at least 115 mm - the length should be such that the base plate protrudes at least
70 mm from the two vertical supports which carry the load of the pipes. The centre-to-
centre distance between the pipes should be at least 42 cm. The pipes must be properly
secured, precisely installed and with a maximum tilt of no more than 2
in both length or in
width. The pipes must also be properly attached to the supports and the concrete track .
Loose fitting pipes must not be used! At the pipe ends (in front of the wall) there should be
an end-stop welded on that is at least 5 cm high - at the end of each season check
whether the stops are not flat, folded, crooked or broken. A soil test bore should be carried
out using probing equipment (see the Health & Safety catalogue applicable in the
Netherlands). It should have a so-called cone value on the top layer of more than 0.4 Mpa
(62 psi).
The use of rail systems not covered by the H&S catalogue applicable in the Netherlands is
permitted on the condition that a stabilisation test is carried out in accordance with the
said H&S catalogue from which it appears that the pipe rail trolley / pipe rail system
combination would be stable. Furthermore, the supports for these other pipe rail systems
must be installed no more that 1 metre apart, and the tilt must not exceed 2 degrees in
both length and width.
The tubes are similar or at least equal to the specifications given in the table below.
The conditions for the axle load stand in the table below.
Cat.
Track-
width
Tube-
diameter /
thickness
Support-
distance
Permissible axle load at
center to center size
Cat.
[mm]
[mm]
[mm]
420mm
[kg]
500mm
[kg]
550mm
[kg]
600mm
[kg]
1
420 t/m
600
51 / 2,25
max. 1000 507
548
573
593
2
420 t/m
600
51 / 2,25
max. 1250 406
438
458
475
3
420 t/m
600
45 / 2
max. 1000 345
372
372
403
4
420 t/m
600
45 / 2
max. 1250 276
298
276
323
Quality steel 37 (St37)
Wheelbase between 62.5% and 125% of the support distance.
All values for other pipe and tube rail supports should be calculated separately.
Source: The Dutch health and safety catalog in force in the Netherlands
https://agroarbo.nl/catalogus/buisrailsysteem/