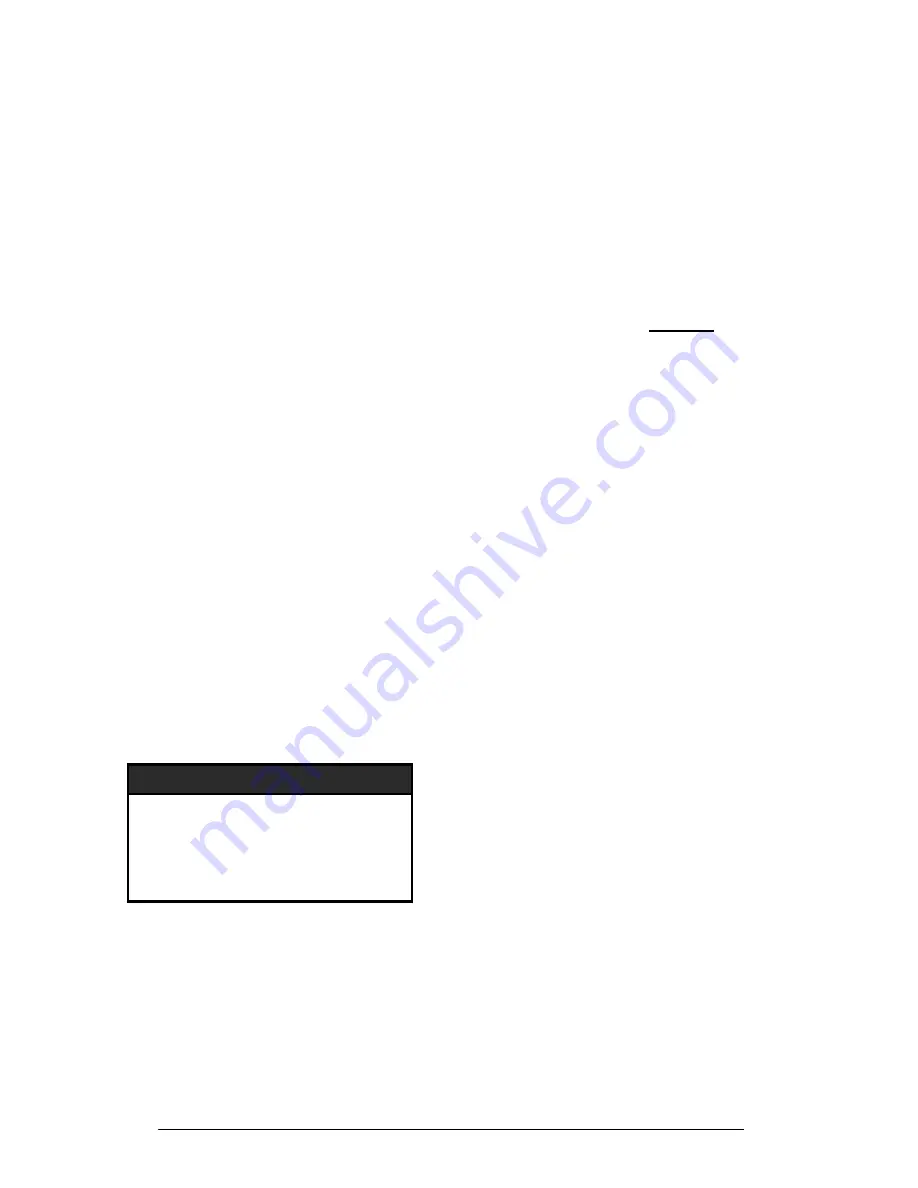
14
7. Check the torque on the tower mounting
bolts; the recommended value is 54 N.m (40
ft-lbs).
8. Check for cracks or loose hardware on the tail
boom and fin.
9. While descending the tower or before raising it,
inspect the following:
A. Check that the tower wiring is properly
secure.
B. Check all tower fasteners.
C. Look for any cracks in the tower structure.
D. Check the condition of the guy wire at-
tachments.
10. Check the connection on all ground rods and
hardware.
11. Inspect the surge arrestor(s). Replace if
there are signs of damage.
12. Remove the alternator shorting connection.
13. Listen to the sound of the machine as it
speeds up. No mechanical sounds, such as a
"clunking" or "banging," should be heard.
Also watch for any new or significant vibration.
Some “growling” from the alternator is normal.
The turbine operation should be very smooth.
14. Inspect the wire run, particularly all electrical
connections.
15. Check condition of all wiring connections into
and out of the PowerCenter.
Warning
Only qualified personnel with proper
safety equipment should climb the
tower. Never climb the tower when
the rotor is turning.
Preventive Maintenance
We recommend that the bearings be re-packed
(re-greased) every 8-12 years. There are four
tapered roller bearings, two for the alternator and
two for the tower adapter. They are all the same
size (Timken L44643/L44610). There are two
bearing seals and we recommend that these be
replaced when the bearings are re-packed.
The strength of the blades, particularly at the root
(inner) end, may degrade over time due to flexure
and UV degradation of the fiberglass material.
The symptom of degradation is a reduction in
blade stiffness fore-and-aft. The blades have to
become very flexible in the fore-aft direction be-
fore there is any risk of tower strikes during se-
vere weather. We recommend that you check
blade stiffness about every 10 years and replace
the blades if they become extremely flexible.
Summary of Contents for 24 VDC B
Page 19: ...18 Appendices ...