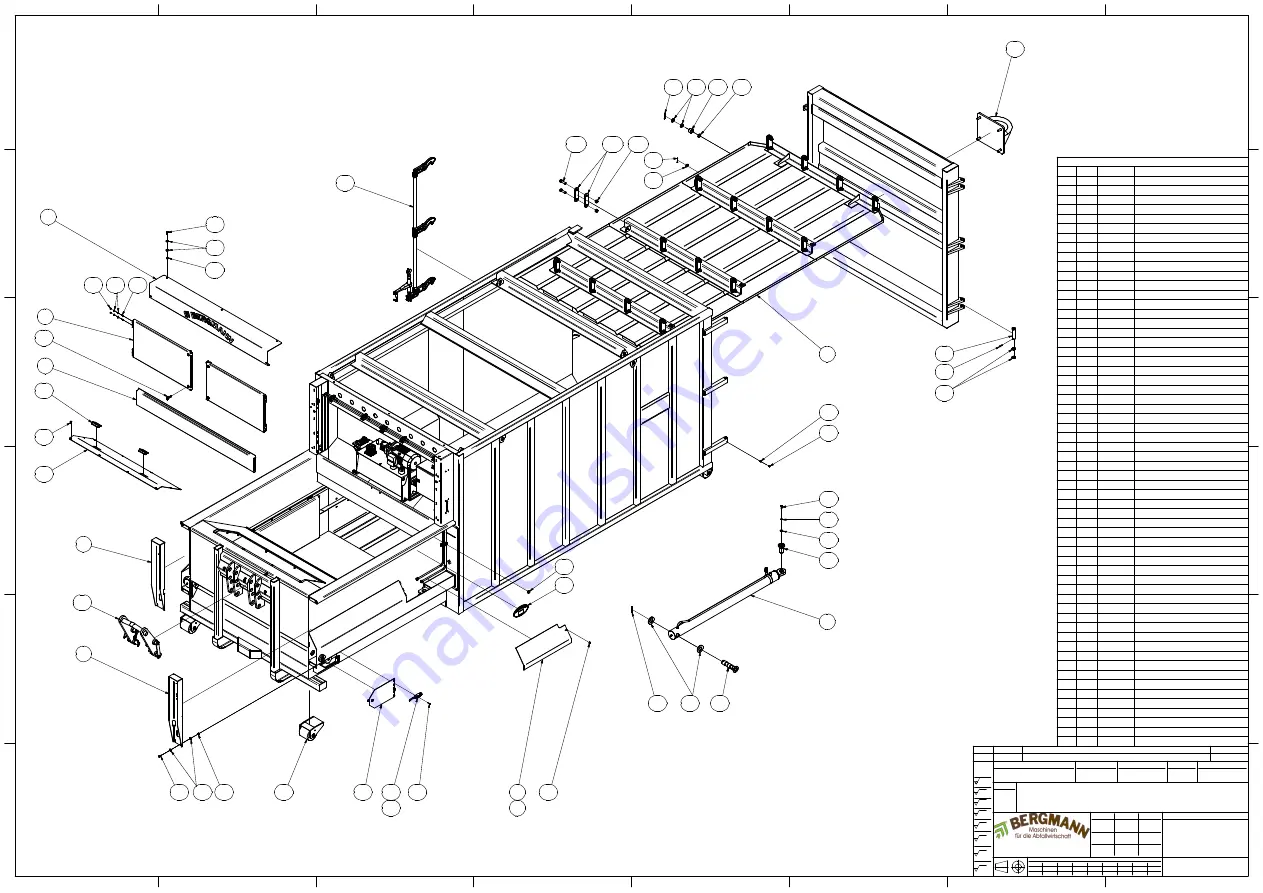
1
1
2
2
3
3
4
4
5
5
6
6
7
7
8
8
A
A
B
B
C
C
D
D
E
E
F
F
Datum
Werkstoff
Bezeichnung
Abmessung
BA17901_1-Z
Zeichnungsnummer
Diese Zeichnung hat gesetzl. Schutz DIN 34
Norm / Bemerkung
Masse
Name
16
z
R
flächenschleifen
geschliffen
polieren
4
z
R
geschliffen
schruppen
z 4
R
schlichten
flächenschleifen
kontrolliert
gezeichnet
gesehen
1302 - 3
DIN ISO
z 63
R
sauber roh
16
z
R
schruppen
z 4
R
feinschlichten
poliert
schlichten
Maßstab
Maschinenübersicht - APB 616
Maschinenübersicht - APB 616
Explosionszeichnung
15.09.2014
Krallmann
5648.007 kg
Verwendungsbereich
www.bergmann-online.com
Telefon: +49 5933 955 0 Fax: +49 5933 1826
Von-Arenberg-Straße 7 D-49762 Lathen/Ems
schruppen
flächenschleifen
z 16
R
geschliffen
über
bis
Allgemeintoleranzen nach DIN ISO 2768 - mittel
30
`0,1
0,5
120
6
315
`0,2
1000
2000
4000
`0,3
`0,8
`1,2
`2,0
`3,0
`0,5
6
30
120
315
1000
2000
4000
8000
Stückliste
Bezeichnung
Teilenummer
Menge
Pos.
APB 616-SN/20
179000003
1
1
Tankraumhaube
096003001
1
1.1
Tankraumklappe kpl.
096005000
2
1.2
Blende
096004001
1
1.3
Abdeckung rechts
179012000
1
1.4
Abdeckung links
179013000
1
1.5
Pendeldach 15 kpl.
103157000
1
1.6
Pendeldack 18 kpl.
103158000
1
1.6
Pendeldach 20 kpl.
103159000
1
1.6
Pendeldach 22 kpl.
103160000
1
1.6
Pendel
060039020
32
1.6.1
Sechskantschraube
000000059
32
1.6.2
Sicherungsmutter
000002037
32
1.6.3
Tastaturblech für Not-Halt
103020055
1
1.7
Tastaturblech für Bedienung
103020056
1
1.8
Hydraulikzylinder
003003672
2
1.9
Bolzen kpl.
060117000
2
1.10
Spannhülse
000004014
4
1.11
U-Scheibe
000003027
4
1.12
Bolzen kpl.
060019000
2
1.13
Kegel-Schmiernippel
000007003
3
1.14
Schmiernippelkappe
000007005
5
1.15
Kunststoffrolle kpl.
060056000
2
1.16
Stahlrolle kpl.
060177000
2
1.16
Kunststoffrolle kpl.
103178000
2
1.16
Stahlrolle kpl.
103113000
2
1.16
Kunststoffrolle kpl.
103672000
2
1.16
Kunststoffrolle kpl.
103681000
2
1.16
Stahlrolle kpl.
103705000
2
1.16
Stahlrolle kpl.
060200000
2
1.16
Deckelblech
179007001
1
1.17
Sechskantschraube
000000049
23
1.18
Sicherungsmutter
000002027
19
1.19
K-Scheibe
000003045
43
1.20
Federring
000003070
4
1.21
Ripp-Schraube
000001061
6
1.22
Verschluss seitliche Tür kpl.
094011000
1
1.23
Aufnahmebügel rund
132058000
1
1.24
Scheibe
000003034
3
1.25
Buchse
001023006
1
1.26
Splint
000006012
1
1.27
U-Scheibe
000003010
1
1.28
Splint
000006005
1
1.29
Firmenschild
005000040
1
1.30
Bügel
001018000
1
1.31
Sechskantschraube
000000050
9
1.32
Schlüssel
096005003
1
1.33
Sicherungsmutter
000002024
8
1.34
K-Scheibe
000003065
16
1.35
Sechskantschraube
000000029
8
1.36
Griffmulde
000005219
2
1.37
Endschalter Inspektionstür L
179004000
1
1.38
Endschalter Inspektionstür R
179009000
1
1.39
Zylinderschraube
000000010
4
1.40
Inspektionstür
179017000
2
1.41
Senkschraube
000010033
10
1.42
Scharnierbolzen
060138000
3
1.43
Spannhülse
000004008
3
1.44
Scheibe
000003034
6
1.45
Verschlussschraube
003001088
1
1.46
1.2
1.1
1.17
1.7
1.31
1.8
1.19
1.20
1.32
1.33
1.42
1.3
1.37
1.18
1.20
1.19
1.16
1.41
1.39
1.38
1.40
1.4
1.5
1.22
1.30
1.10
1.12
1.11
1.9
1.13
1.20
1.21
1.18
1.14
1.15
1.23
1.6
1.24
1.6.1
1.6.2
1.6.3
1.28
1.29
1.25
1.26
1.25
1.27
1.36
1.35
1.34
1.43
1.44
1.45
1.46
Summary of Contents for ALPHA-PACK-BIN
Page 2: ......
Page 6: ......
Page 16: ......
Page 20: ......
Page 28: ......
Page 34: ......
Page 50: ......
Page 52: ......
Page 53: ...10 Dimensions 10 01 Illustration standard version deviations are possible ...
Page 54: ......
Page 60: ......
Page 64: ......
Page 66: ......
Page 68: ......
Page 70: ......
Page 72: ......
Page 74: ......
Page 76: ......
Page 78: ......
Page 80: ......
Page 82: ......
Page 84: ......
Page 86: ......
Page 88: ......
Page 90: ......
Page 92: ......
Page 94: ......
Page 96: ......