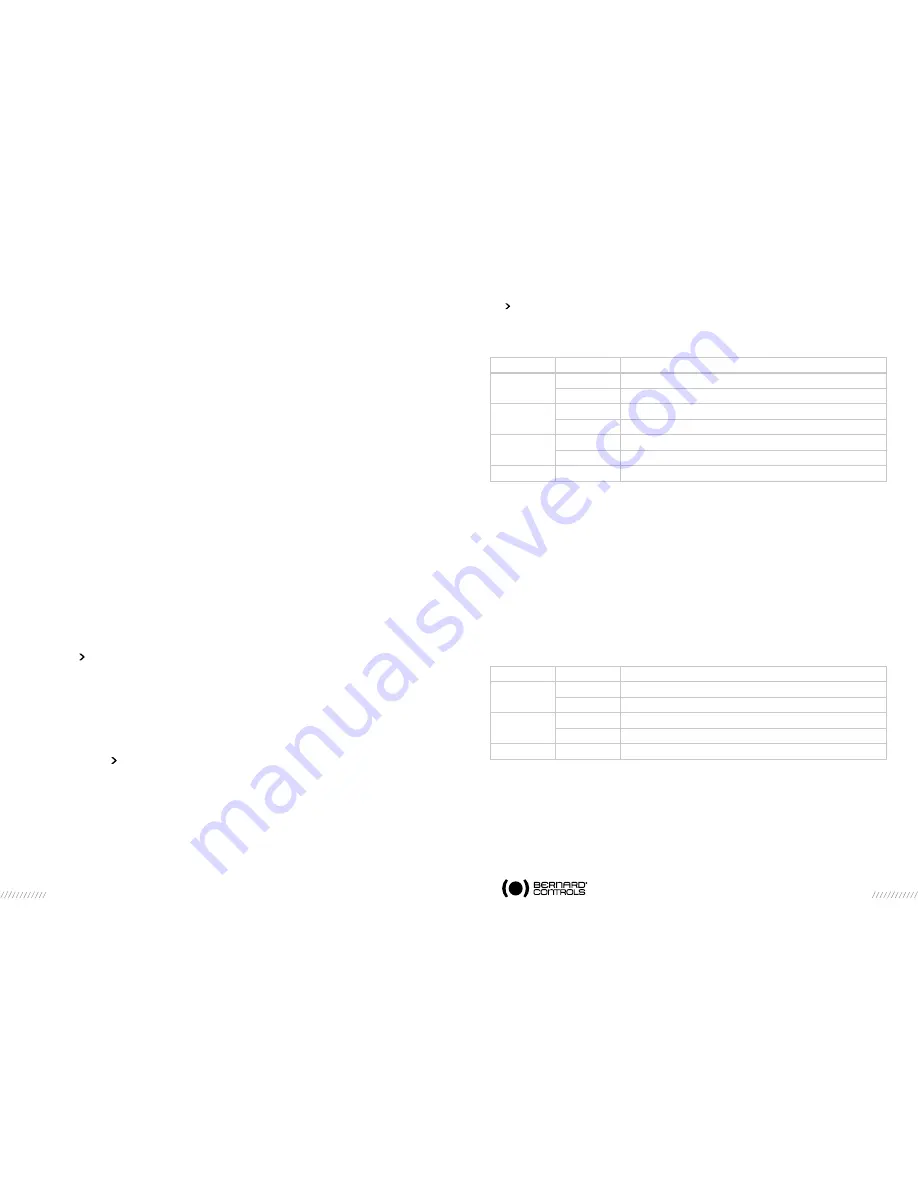
8
9
For one actuator the address is the same on both lines. When the actuator is powered on, the
INTELLIBUS module tries to get the communication on a first line and toggles between both lines
until to find the communication. It is the INTELLIBUS module that decides to communicate with one
line or the other. Like this, all the actuators are not obliged communicating one the same line and
both lines are working simultaneously. There is not a main line and a backup line, each line has the
same level. On the other hand the actuator interface has a primary channel (the one that got a data
exchange state) and a backup channel.
Information supplied by the primary or the backup channel:
- This channel (or slave) is primary or this channel is backup
- 2 channels available or only one.
- FR mode (Flying redundancy) or SR mode (System redundancy).
See details at § «Command and Signalling»
Redundancy management must be performed by the PLC. To manage the line redundancy a PLC
could be used with different level of equipment.
- One PLC with 2 Profibus DPV1 Interface. For example a CPU 317-2 DP from Siemens
that includes 2 Profibus DPV1 interfaces. The PLC is single and interface is doubled.
PLC should be programmed to manage the redundancy.
If the PLC doesn’t support the special redundancy extensions of the Profibus Guide
Line «Slave redundancy» then INTELLIBUS module will be used as a classical
redundancy. To do that there is to load in the PLC the appropriate GSD file for classical redun-
dancy: LBVR0ACC.GSD
- Two PLC with each a Profibus DPV1 interface. A link between both PLC through an auxiliary
communication port allows the redundancy monitoring. Example 2 CPU 317-2 DP from
Siemens. PLC should be programmed to manage the redundancy.
If the PLC doesn’t support the special redundancy extensions of the Profibus Guide Line «Slave
Redundancy» then INTELLIBUS module will be used as a classical redundancy. To do that
there is to load in the PLC the appropriate GSD file for classical redundancy: LBVR0ACC.GSD
- Two PLC fault tolerant like the CPU 414 H from Siemens and optic fibre between them. In that
case no programming is necessary to manage the redundancy.
This PLC supports the special redundancy extensions. The INTELLIBUS module will be used
with RedCom and extensions, and to do that there is to load the appropriate GSD file in the
PLC : LBRE0ACC.GSD.
4
CONTROLS AND INDICATIONS
The Profibus DPV1 system has a cyclic communication (compatible with Profibus DP) and acyclic
communication. The cyclic communication is mainly use for the Process. Data are read and written
in a well-defined timing. The useful data are selected in the list below and transmitted in a cyclic
way. The selection of only a few data also increases the communication speed.
The acyclic communication is mainly use for maintenance. The data are collected only on request
that avoid to reduce the cyclic communication speed. See below «§ 5 Acyclic communication»
4.1
CONTROLS
Valve control by the Profibus fieldbus is possible only if the actuator rotating selector is on the
«remote» position.
Conditions which can prevent a command to be executed:
- Actuator rotating selector on «local» or «OFF».
- Alarm tripped (motor thermal overload)
- Emergency command received (ESD)
Control byte description
Actuators controls are located at the addresses 0 to 4 on the INTELLIBUS module. These controls are:
Address 0: ON-OFF control
OPEN / CLOSE: Open and close command. According to the actuator configuration, it is possible to
select a priority to the opening or to the closing command (refer to NR1151)
By default there is no priority given to either opening or closing.
Priority can be used to:
- Allow to reverse the actuator rotation direction during a manoeuvre without having to use
the stop command. In this case it is necessary to set a priority to the opening or to the closing
direction.
- Give priority to one or the other rotation direction: if the actuator receives the open and close
commands simultaneously and the priority has been given to the opening, the actuator will
run the open position.
STOP: if this command is maintained at 0 (most common case), the open and close commands have
to be maintained. If this command is set to 1, a short duration open / close command pulse is suf-
ficient to drive the valve to the open or closed position. In this case, the stop command (0) can be
used to stop the actuator during the travel in its current position.
Address 1: Auxiliary commands
By default, auxiliary command 1 is assigned to local control (actuator selector) inhibited.
By default, auxiliary command 2 is not assigned to a Profibus command but to an emergency
command (ESD): This command is hardwired (separate wiring) and directly connected to the control
box main strip.
These commands depend of actuator configuration (refer to NR1151) and can be assigned to the
following functions.
Bit n°
Value
Description
Bit 0
0
NO COMMAND
1
OPEN COMMAND
Bit 1
0
NO COMMAND
1
CLOSE COMMAND
Bit 2
0
STOP ( OR MAINTAINED COMMAND MODE)
1
NO STOP (OR PULSE COMMAND MODE)
Bit 3 to 7
-
NOT USED
Bit n°
Value
Description
Bit 0
0
NO COMMAND
1
AUXILIARY COMMAND 1
Bit 1
0
NO COMMAND
1
AUXILIARY COMMAND 2
Bit 2 to 7
-
NOT USED