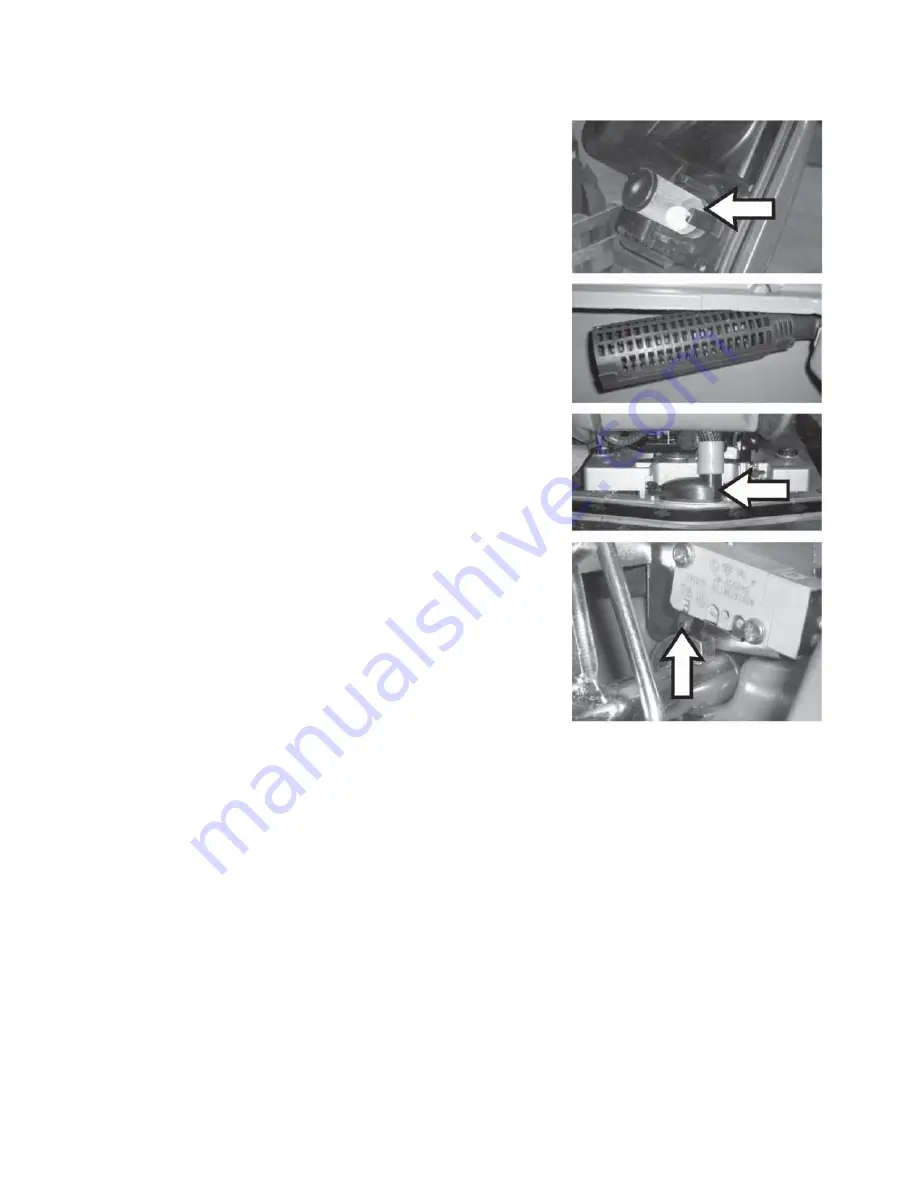
46
VACUUM SYSTEM INSPECTION
1. Verify the cleanliness and functionality of the
fl oat fi lter
.
2. Check the air sealing of the
vacuum head
on the recovery tank.
3. Verify the connections and the sealing of the vacuum hoses and the squeegee
hoses.
4. Check the sealing of the
squeegee hose adapter
.
5. Check the sealing of the exhaust hose and exhaust hose plug.
6. Vacuum micro switch adjustment:
Adjust the vacuum micro switch in way that when the cam on the squeegee
lever
push the micro switch
there is about 0.5 mm of clearance of the micro
switch lever.
Summary of Contents for STEALTH ASD20B
Page 20: ...20 BRUSH DECK DIAGRAM ...
Page 26: ...26 SQUEEGEE YOKE DIAGRAM ...
Page 36: ...36 SOLUTION DELIVERY DIAGRAM 8 ...
Page 50: ...50 ...
Page 51: ...51 ...