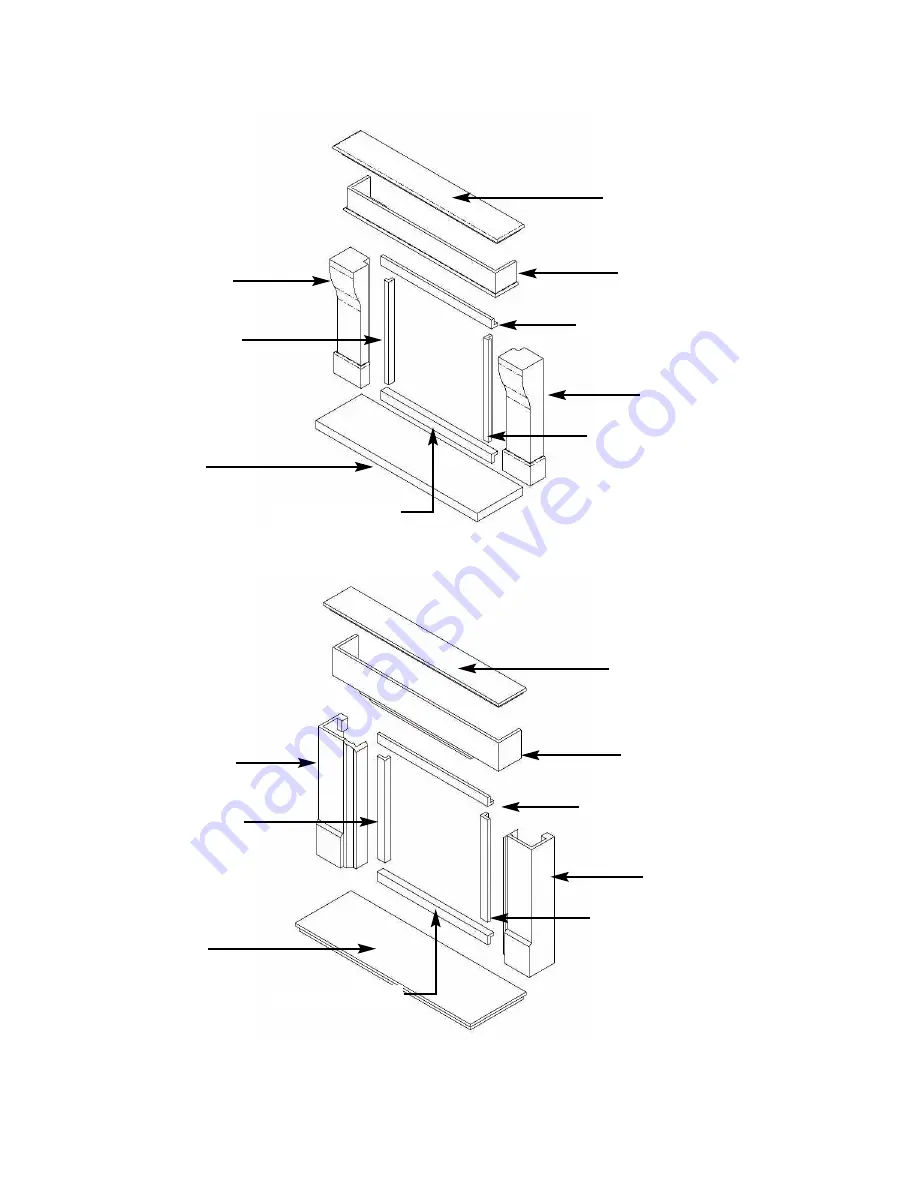
Fig. 20
Fig. 21
23
Shelf Top Section
L/H Leg
R/H Leg
Hearth Panel
Bottom Infill Section
Top Infill Section
Shelf Infill Section
NOTE : It is recommended
that a spillage test is
completed before fixing /
sealing the fire surround
in place.
R/H Infill Section
L/H Infill Section
Shelf Top Section
L/H Leg
R/H Leg
Hearth Panel
Bottom Infill Section
Top Infill Section
Shelf Infill Section
R/H Infill Section
L/H Infill Section