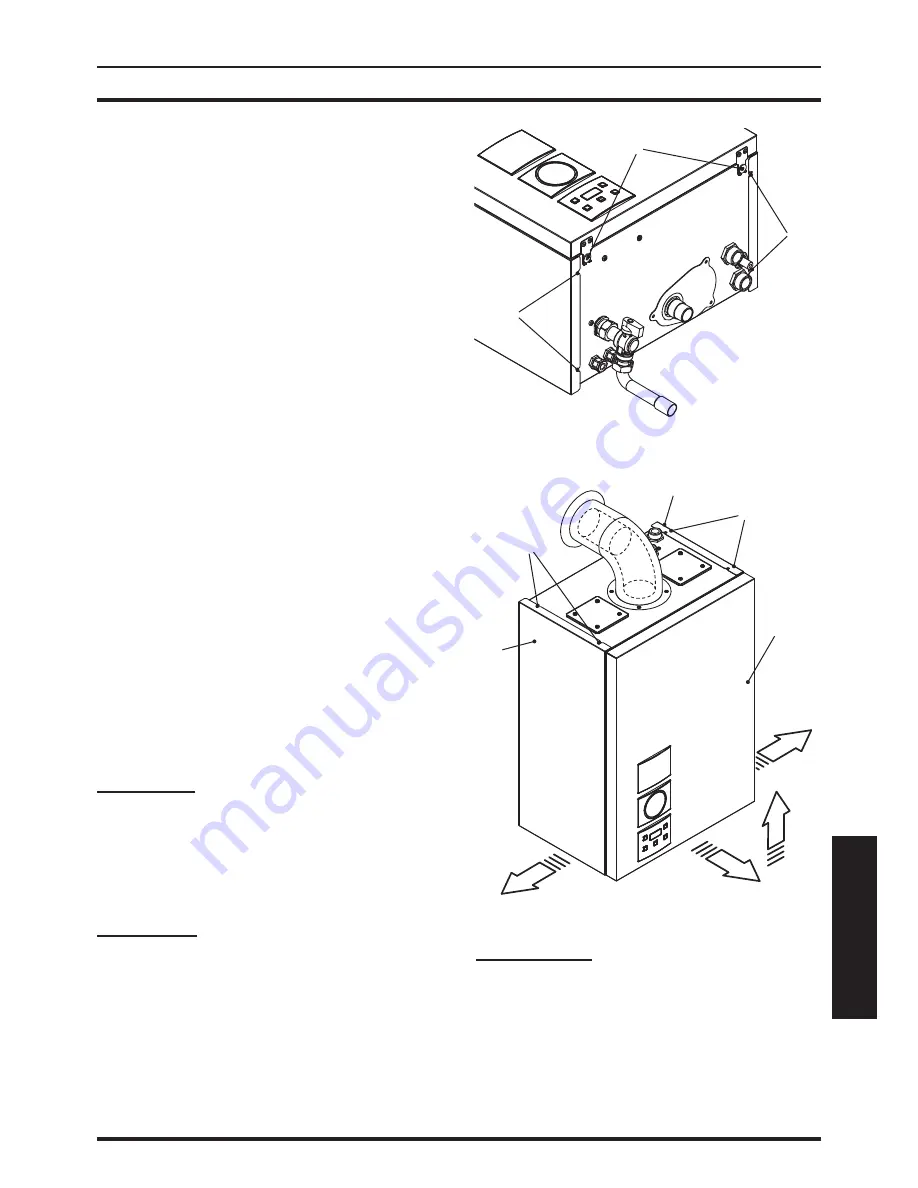
- 73 -
MAINTENANCE
MAINTENANCE
9
MAINTENANCE
9.1 Warnings
The procedures detailed in this chapter
must be carried out only Gas Safety Reg-
istered Engineer
. Thus you are advised to
contact an Authorised Service Agent.
For Ireland (IE), the servicing work must
be carried out by a competent Person.
For effi cient and continuous operation of the
boiler you are advised to have, at least once
a year, maintenance and cleaning done by
an Approved Service Engineer.
Isolate the appliance from the electricity
supply
by turning off the fused spur isola-
tion switch adjacent to the appliance and
turn off the gas cock, before carrying out
any procedures, whatsoever, for cleaning,
maintenance, opening or dismantling boiler
panels. The Engineer should complete the
Service Interval Record at the back of the
manual.
9.2
Dismantling the external
panels
Front panel
• Unscrew screws A and remove the front
panel
D by pulling it and pushing it to-
wards the top so that it is freed from the
top housings ( Fig. 9.1 and Fig. 9.2 ).
Side panels
Loosen screws "
B
-
F
"
and " C
-
H
"
in Fig. 9.1
and remove the two side panels E and G by
pulling towards the outside.
Fig. 9.1
A
B
C
Fig. 9.2
D
E
F
G
H
Control panel
Turn the controls panel I , as shown in fi gure
Fig. 9.3 , to access in an optimal manner the
components inside the boiler.
Summary of Contents for Activ A 120V
Page 20: ...20 USE USEFUL ADVICE Fig 3 7 14...
Page 81: ...81 NOTES...
Page 82: ...82 NOTES...
Page 83: ......