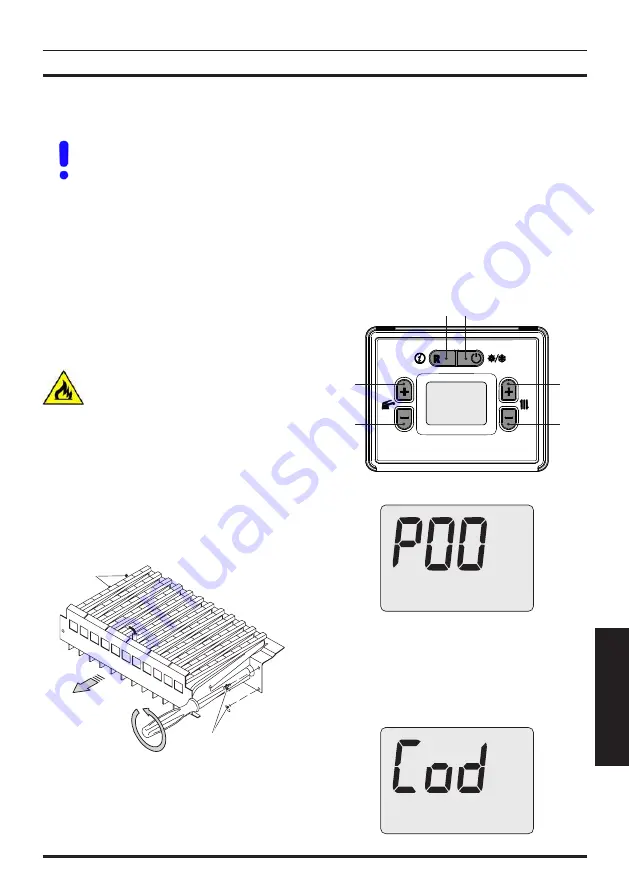
- 53 -
MAINTENANCE
GAS CONVERSION
8
GAS CONVERSION
8.1 Warnings
The operations to adapt the boil-
er to the type of gas available
must be carried out by an autho-
rised service centre.
The components used for adapting to the
type of gas available must only be original
spare parts.
For instructions regarding calibrating the
boiler gas valve, refer to section "CHECK-
ING THE GAS SETTING" on page 48.
8.2 Gas operations and setting
Check that the gas cock mount-
ed on the gas piping to the boil-
er is closed and that the unit is
not powered.
• Remove the front and side panels as
shown in section "Maintenance" on page
55.
• Remove the movable wall from the sealed
chamber.
• Remove the front panel from the combus-
tion chamber and the burner in Figure 8.1.
Figure 8.1
A
A
• Convert the type of gas by correctly re-
placing the burner nozzles and gaskets.
• Reassemble the burner Figure 8.1, the
front combustion chamber panel and the
movable wall of the sealed chamber.
• Restore electric power to the boiler.
The boiler is factory set to operate with
natural gas (G20).
To set boiler operation to
LPG gas (G31)
,
carry out the following settings:
•
Enter “programming mode” by holding
down buttons 17 and 18 for 5 seconds at
the same time (Figure 8.2). The code
P00
appears on the display, indicating entry
into “parameter P00” (Figure 8.3).
Figure 8.2
12
13
15
16
17
18
Figure 8.3
bar
RESET
• Scroll through the various parameters us-
ing 12 or 13 until the LCD display shows
the message
Cod
, indicating entry into
“parameter Cod” (Figure 8.4), and then
displays three dashes “
- - -
”.
Figure 8.4
bar
RESET
Summary of Contents for RINNOVA M290E.24CM
Page 1: ...User manual and installation instructions RINNOVA...
Page 63: ......