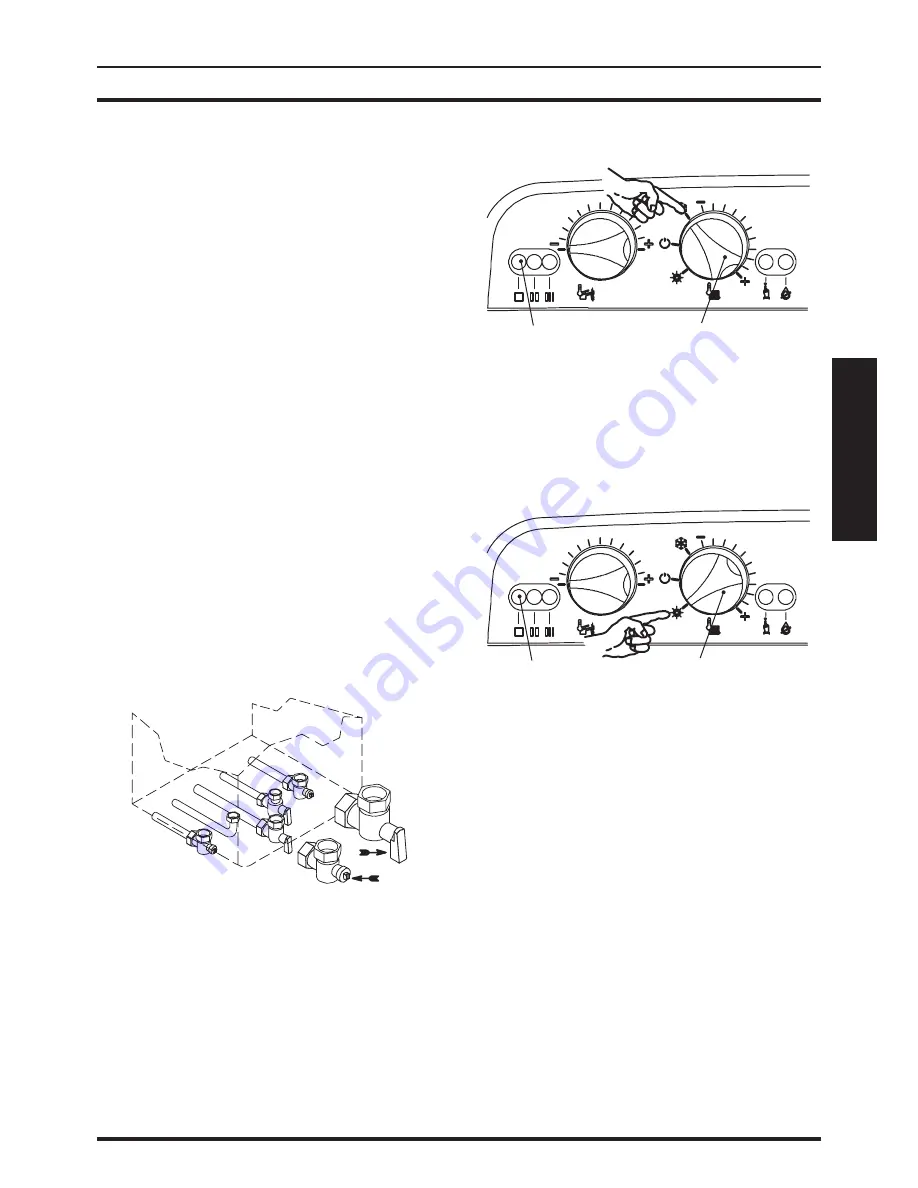
- 11 -
USE
INSTRUCTIoNS FoR USE
• Close the valves and remove the filling
loop.
If you experience any difficulty with the
operation of the boiler, switch off the boil-
er immediately at the fused spur isolation
switch and contact your Installer or an
approved Service Engineer.
Air introduced into the boiler during this fill-
ing process will vent through the automatic
air purger fitted to the boiler. You may also
find it necessary to vent air from your radia-
tor circuit using your radiator key, however
be aware that excessive venting will cause
the pressure in the system to drop.
Always ensure that the pressure gauge is set
at the required pressure.
2.3 Ignition
• Check that the valves located in the lower
part of the boiler are open Fig. 2.3.
Fig. 2.3
open position
• Turn on the electricity supply to the boil-
er switching on the fused spur isolation
switch. The appliance operation light 10
(Fig. 2.4) will flash every 4 seconds (stand-
by condition).
• If the boiler is to be used for c.h. and d.h.w,
position the function selector 8 as in Fig.
2.4. The appliance operation light 10 will
flash every 2 seconds (operating boiler).
Fig. 2.4
10
8
• If d.h.w. supply only is required, position
the function selector 8 as in Fig. 2.5. The
appliance operation light 10 will flash every
2 seconds (operating boiler).
Fig. 2.5
10
8
2.4 C.h. circuit temperature
The output temperature of c.h. water is ad-
justable from a minimum of about 40°C to a
maximum of about 85°C (Fig. 2.6), by turning
the function selector (8).
Adjustment of c.h. output on the boiler is au-
tomatic.
The greatest output pre-set in the factory
can, however, be reduced in level according
to actual system requirements; this does not
affect the maximum output in d.h.w. opera-
tion.
Such adjustments must be carried out by a
qualified person; therefore we advise you to
contact your installer or Service Agent.
Adjustment of the boiler temperature alters
Summary of Contents for Riva Plus HE M296.24SC
Page 56: ...56 NOTES...
Page 57: ...57 NOTES...