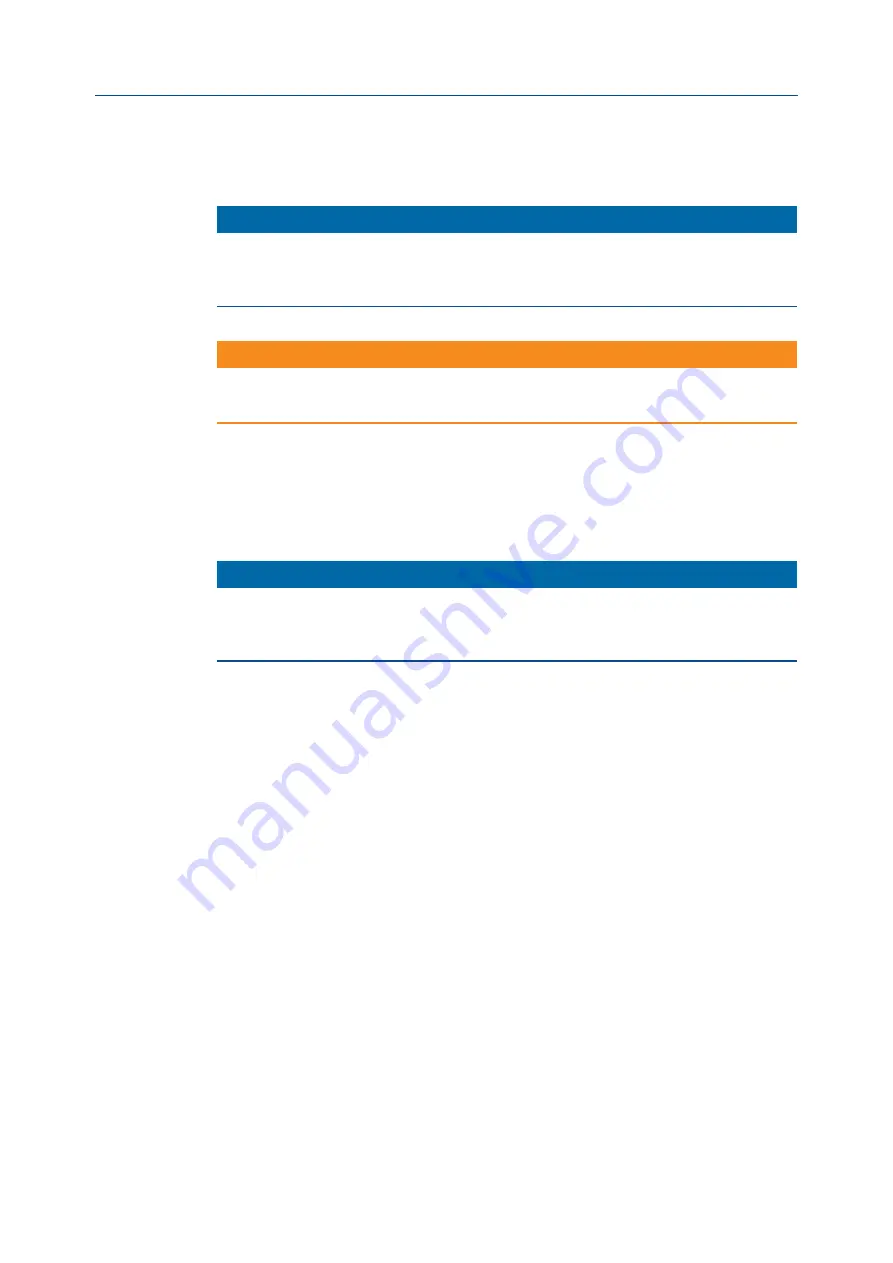
June 2021
Installation, Operation and Maintenance Manual
MAN 689 Rev. 6
26
Maintenance
Section 5: Maintenance
Section 5: Maintenance
NOTICE
Before carrying out any maintenance operation, it is necessary to close the pneumatic
feed line and exhaust the pressure from the actuator cylinder and from the control unit,
to ensure safety of maintenance staff.
!
WARNING
Installation, commissioning and maintenance and repair works should be carried out by
qualified staff.
5.1
Routine Maintenance
actuators have been designed to work for long periods in the severest conditions with no
need for maintenance.
NOTICE
Periodicity and regularity of inspections is particularly influenced by specific environmental
and working conditions. They can be initially determined experimentally and then be
improved according to actual maintenance conditions and needs.
Anyway every 2 years of operation the following is recommended:
1.
Check that the actuator operates the valve correctly and with the required
operating times. If the actuator operation is very infrequent, carry out a few
opening and closing operations with all the existing controls (remote control, local
control, emergency controls, etc.), if this is allowed by the conditions of the plant.
2.
Check that the signals to the remote control desk are correct.
3.
Check that the air supply pressure value is within the required range.
4.
If there is an air filter on the actuator, bleed the condense water accumulated in
the cup by opening the drain cock. Disassemble the cup periodically and wash
it with soap and water; disassemble the filter: if this is made up of a sintered
cartridge, wash it with nitrate solvent and blow through with air. If the filter is
made of cellulose, it must be replaced when clogged.
5.
Check that the external components of the actuator are in good conditions.
6.
Check all the paint-coat of the actuator. If some areas are damaged, repair the
paint-coat according to the applicable specification.
7.
Check that there are no leaks in the pneumatic connections. If necessary, tighten
the nuts of the pipe fittings.